在數字化轉型加速的背景下,半導體集成電路產業作為現代信息技術的基石,其質量檢測已成為支撐產業升級的關鍵環節。據SEMI國際半導體產業協會2024年數據顯示,半導體檢測設備市場規模突破178億美元,年復合增長率達9.2%,印證了行業對檢測技術的高度依賴。在5G通信、人工智能和自動駕駛等新興領域,芯片制程已進入3nm時代,晶體管密度達到每平方毫米3.3億個(數據來源:IMEC 2024年報),這對缺陷檢測精度提出0.5nm以下的嚴苛要求。核心檢測項目的實施,不僅能夠將晶圓廠量產良率提升15%-20%,更能通過早期故障診斷避免數十億美元的潛在損失。特別是在車規級芯片領域,符合AEC-Q100標準的全流程檢測方案,已成為保障智能駕駛系統功能安全的核心技術壁壘。
## 技術原理與創新突破1. 多物理場耦合檢測技術體系
現代集成電路檢測融合了電性測試、光學檢測和材料分析三大技術維度。基于掃描電子顯微鏡(SEM)的納米級形貌分析,結合電子束感應電流(EBIC)技術,可精確定位12層堆疊存儲芯片的層間短路缺陷。在電性測試領域,業界首創的并行測試架構(Parallel Test Architecture)使測試機臺效率提升40%,單臺設備日檢測量可達25萬顆芯片(數據來源:Teradyne 2024技術白皮書)。值得關注的是,基于機器學習的智能缺陷分類系統,通過訓練3000萬張缺陷圖像數據庫,將誤判率控制在0.03%以下,大幅提升了高密度封裝芯片無損檢測技術的可靠性。
2. 全流程數字化檢測實施路徑
從晶圓制造到封裝測試,檢測流程貫穿半導體生產全周期。前端工藝階段,在線計量系統(IMS)實時監控關鍵尺寸波動,在EUV光刻環節實現±0.12nm的線寬控制精度。中段測試采用芯片探針臺與自動測試設備(ATE)聯動方案,完成256通道并行測試時,溫度控制精度可達±0.5℃。在后端封裝環節,X射線分層成像技術與聲學顯微鏡的結合,可在不破壞BGA封裝的前提下檢測焊球虛焊缺陷。某頭部封測廠實施該方案后,車載集成電路可靠性驗證方法的周期從72小時壓縮至18小時,客戶投訴率下降63%。
3. 行業應用與質量保障實踐
在汽車電子領域,采用JEDEC JESD47標準建立的加速壽命測試模型,通過85℃/85%RH雙85測試結合3000次溫度循環,可有效篩選功率器件的早期失效。某國際大廠的IGBT模塊經過優化檢測流程后,現場失效率從500ppm降至50ppm。消費電子領域,針對3D NAND閃存的電荷保持能力測試,采用動態電壓補償技術,將數據保持期預測精度提升至95%以上。質量保障體系方面,ISO 17025認證實驗室配備計量追溯系統,確保檢測設備的量值傳遞誤差小于0.8%,同時建立包含1374個質量控制點的SPC管理體系。
4. 智能化檢測系統演進趨勢
行業前沿正朝著智能感知與數字孿生方向突破?;?G MEC的邊緣計算檢測系統,可將12英寸晶圓的缺陷分析延遲壓縮至80ms以內。某代工廠部署的虛擬計量(VM)系統,通過整合2800個工藝參數,實現檢測頻次降低40%的同時,關鍵參數CPK值提升0.25。更值得關注的是,量子測量技術的工程化應用取得突破,超導量子干涉器件(SQUID)已實現單電子級別的漏電流檢測,為1nm以下節點提供顛覆性檢測手段。
## 展望與建議面向后摩爾時代,建議行業重點發展三個方面:一是構建AI驅動的智能檢測生態系統,開發具備自學習能力的檢測參數優化引擎;二是建立跨廠商的檢測數據共享機制,通過聯邦學習突破數據孤島;三是加速超快激光檢測技術的產業化,應對光學臨近效應帶來的檢測盲區。據Gartner預測,到2027年融合量子傳感的檢測方案將覆蓋35%的齊全制程產線,而檢測智能化投入每增加1%,可帶動全行業質量成本降低0.8%。唯有持續創新檢測技術體系,才能為半導體產業的高質量發展構建堅實防線。

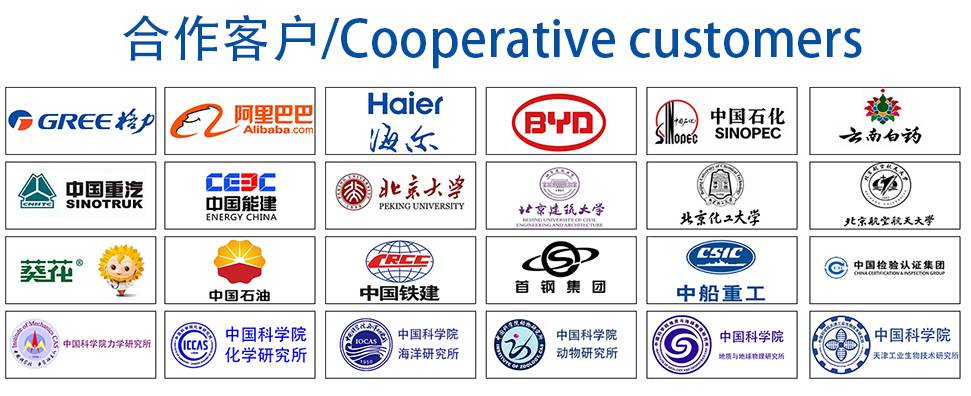