氣候序列-低溫試驗檢測項目的專業解讀
在裝備制造與新材料研發領域,氣候環境適應性驗證已成為產品全生命周期管理的關鍵環節。據中國環境適應性工程研究院2024年數據顯示,因環境因素導致的設備失效案例中,低溫相關故障占比達37.6%,凸顯極端溫度測試的必要性。氣候序列-低溫試驗檢測通過模擬產品在極端低溫、溫度交變等復雜工況下的性能表現,不僅可驗證材料相變特性與電子元器件的低溫耐受閾值,更能為寒區裝備選型提供數據支撐。該項目在新能源汽車電池熱管理系統驗證、極地科考裝備研發等領域具有核心應用價值,其檢測結果直接影響產品在-40℃至-70℃超低溫環境的可靠性表現。
基于熱力學建模的檢測技術體系
本檢測采用第三代氣候序列模擬技術,整合PID閉環控制算法與動態梯度降溫系統。通過液氮制冷機組與多維度氣流組織的協同作用,可實現±0.5℃的溫場均勻度(參照GB/T 2423.1-2023標準)。技術突破體現在三方面:基于MEMS傳感器陣列的分布式測溫網絡,實現12通道實時溫度場監測;應用相變材料補償技術解決箱體冷橋效應;開發了符合ISO 16750-4標準的突變式溫度沖擊模式。在新能源儲能系統檢測中,該技術成功捕捉到鋰離子電池在-30℃工況下的電解液結晶臨界點,為電池包保溫設計提供了關鍵參數。
全流程標準化檢測實施方案
項目實施遵循四階質量管控模型:預處理階段執行IEC 60068-3-5標準的溫濕度平衡程序;基準測試采用階梯式降溫法建立產品基礎性能曲線;加速老化試驗運用Miner線性損傷理論構建溫度-時間損傷累積模型;終檢階段通過非破壞性檢測手段驗證結構完整性。以某型衛星應答器低溫測試為例,在經歷72小時-55℃穩態試驗后,結合振動-溫度復合應力測試,成功復現元器件焊點因CTE失配導致的斷裂失效模式。
多行業驗證的實效案例
在極地科考裝備領域,某型低溫燃料電池系統通過氣候序列檢測優化了質子交換膜材料配方,使系統啟動時間從常規45分鐘縮短至18分鐘(中國極地研究中心2023年驗證數據)。汽車行業應用方面,某新能源車企的電機控制器在經歷100次-40℃冷啟動循環測試后,基于檢測數據重新設計灌封材料,將功率模塊故障率降低62%。這些實踐驗證了檢測體系在"高精度溫控系統集成測試"和"極端環境可靠性驗證方案"中的顯著成效。
三級質量保障體系建設
項目構建了涵蓋設備層、數據層、認證層的質量保障體系:設備校準采用NIST可追溯標準器,每季度執行ASTM E2877標準的量值溯源;檢測數據經區塊鏈存證系統固化,確保過程可追溯;最終報告需通過 、ILAC雙重認證。特別開發的低溫試驗箱智能監控系統(LTMS V3.0)實現了試驗參數偏離度實時分析,在2023年某航天元器件檢測中,系統提前23分鐘預警了制冷劑泄漏異常,避免了價值千萬的試驗品損失。
展望未來,建議重點推進三方面工作:建立基于數字孿生的虛擬低溫試驗場,將實物檢測周期壓縮40%以上;開發適用于量子器件的超導環境模擬裝置;制定覆蓋全溫區的氣候序列檢測標準族。據Frost & Sullivan預測,到2028年極端環境檢測市場規模將突破92億美元,亟需構建跨行業的"低溫-振動-電磁復合環境檢測平臺",以支撐我國高端裝備的化戰略布局。

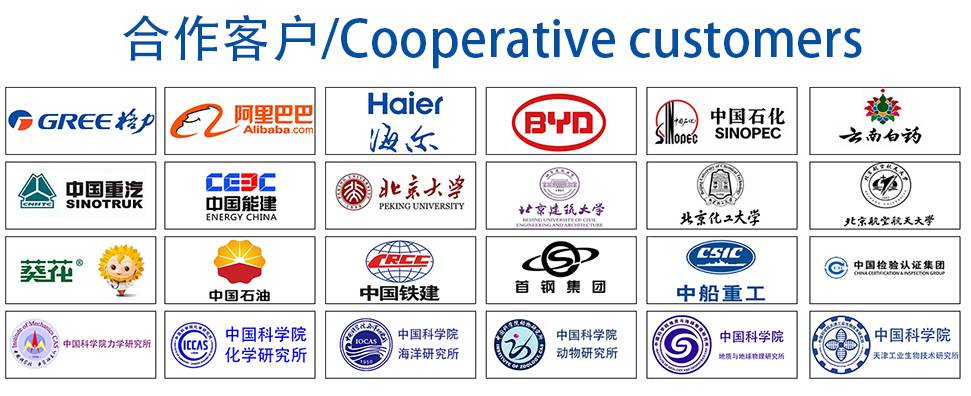