壓力容器熱應力檢測技術及其核心檢測項目
引言
一、熱應力產生的機理與檢測必要性
1. 熱應力成因
- ?E:彈性模量
- ?α:熱膨脹系數
- Δ?ΔT:溫差
- ?ν:泊松比
2. 失效風險
- 熱疲勞裂紋:交變溫度場引起應力循環(典型案例:加氫反應器內壁鱗狀裂紋)
- 局部蠕變:高溫區域材料持續變形(如鍋爐過熱器管束)
- 幾何失穩:非對稱溫度場導致結構翹曲
3. 檢測必要性
- 驗證設計階段的溫度場仿真準確性
- 在線監控運行中異常溫升熱點
- 評估殘余應力對設備壽命的影響
二、熱應力檢測核心技術體系
(一)溫度場測量
1. 紅外熱成像技術
- 原理:通過紅外輻射強度反演表面溫度分布
- 設備:高分辨率紅外熱像儀(建議選用320×240像素以上)
- 應用場景:
- 快速定位焊接殘余應力區的溫度異常帶
- 監測啟動/停機階段的瞬時溫度梯度
- 優勢:非接觸、全場測量,精度可達±1℃
- 案例:某煉廠重整反應器外壁檢測發現142℃高溫區,經內窺鏡確認內襯耐火層破損
2. 熱電偶陣列監測
- 布置方式:按ASME標準間距布置K型或T型熱電偶
- 數據采集:使用多通道巡檢儀(采樣率≥1Hz)
- 典型應用:
- 核容器穩態運行溫度場驗證
- 高溫氣冷堆壓力邊界實時監控
(二)機械應力檢測
1. 應變片法
- 選型原則:
- 高溫工況選用Karma合金應變片(工作溫度可達300℃)
- 高濕度環境采用防水封裝型號
- 布片方案:
- 在溫度梯度最大區域按0°-45°-90°三向布置
- 焊縫兩側對稱布置補償片消除熱輸出誤差
- 數據處理:通過廣義胡克定律計算主應力方向與大小
2. 超聲波殘余應力檢測
- 技術原理:利用聲彈性效應(聲速與應力呈線性關系)
- 設備要求:
- 配備雙晶探頭的便攜式應力儀(如美國AMSY-6)
- 校準試塊需與容器材料同質
- 檢出能力:可識別深度5mm內±50MPa應力變化
3. X射線衍射法(XRD)
- 適用條件:
- 表面殘余應力精確測定(測量深度約10-30μm)
- 需配合電解拋光去除表面氧化層
- 局限性:設備昂貴,需現場輻射防護
(三)數值模擬校準
1. 有限元建模要點
- 材料模型:定義溫度相關的彈性模量、泊松比、熱膨脹系數
- 邊界條件:
- 對流換熱系數依據介質流速計算
- 輻射散熱按斯蒂芬-玻爾茲曼定律設定
- 網格劃分:在溫度突變區進行局部加密(雅可比比>0.7)
2. 實驗數據融合
- 將實測溫度場作為輸入加載到FEA模型
- 通過反演算法修正熱邊界條件參數
- 輸出云圖與應變片數據誤差應<15%
三、關鍵檢測項目操作指南
1. 焊縫區域熱應力專項檢測
- 檢測步驟:
- 預熱階段監測HAZ(熱影響區)溫升速率(≤100℃/h)
- 使用磁記憶檢測(MMT)定位應力集中區
- XRD測定熔合線殘余應力分布
- 驗收標準:
- 殘余壓應力峰值≤0.8倍材料屈服強度
- 熱應力波動幅值<疲勞極限的30%
2. 局部過熱缺陷診斷
- 特征識別:
- 紅外圖像呈現"馬鞍形"溫度分布
- 聲發射監測捕捉微裂紋擴展信號
- 量化評估:
- 采用Paris公式計算熱疲勞裂紋擴展速率
- 參照API 579進行剩余壽命預測
3. 材料劣化關聯分析
- 耦合檢測方法:
- 硬度測試(布氏硬度計)評估蠕變損傷
- 金相復膜觀測碳化物聚集程度
- 退化模型:
- 建立應力-溫度-壽命(σ-T-N)三維關系圖譜
- Larson-Miller參數法預估高溫持久強度
四、檢測質量保障措施
- 環境控制:
- 避免強電磁干擾(距離高壓線>50m)
- 風速>3m/s時暫停紅外檢測
- 設備校驗:
- 熱電偶每年進行冰點-沸點雙點校準
- 應變儀橋路電阻平衡誤差≤0.1%
- 人員資質:
- 持有ASNT/EN473二級以上認證
- 具備熱力學與斷裂力學基礎
五、未來技術趨勢
- 智能傳感網絡:
- 植入式FBG光纖傳感器實現分布式監測
- 無線傳輸技術降低布線復雜度
- 數字孿生應用:
- 基于數字孿生的應力場實時可視化
- 機器學習預測熱應力演變路徑
結語
上一篇:熱循環金屬化孔電阻變化檢測下一篇:交變濕熱剩余循環檢測

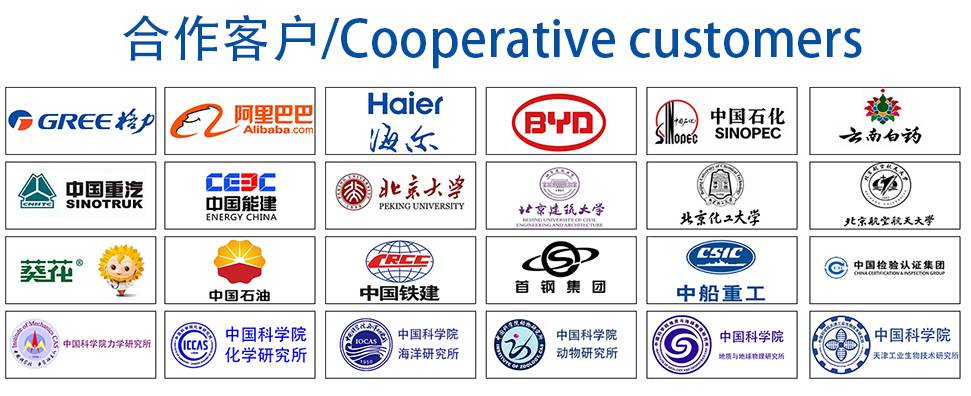
材料實驗室
熱門檢測
18
10
15
16
19
12
13
16
13
12
12
16
15
14
21
13
21
17
18
22
推薦檢測
聯系電話
400-635-0567