# 膠質檢測技術發展與應用白皮書
## 引言
近年來,隨著高分子材料在汽車制造、電子封裝、醫療器械等領域的廣泛應用,膠質材料性能檢測已成為工業質量控制的關鍵環節。據中國材料研究學會2024年統計數據顯示,每年因膠粘劑失效導致的工業損失超過270億美元,其中78%的故障源于材料老化或工藝缺陷。在此背景下,膠質檢測項目通過精準量化材料粘彈性、固化度等核心參數,為產品質量控制提供了科學依據。其核心價值不僅體現在降低產品故障率,更在于建立可追溯的質量數據庫,支持工業4.0時代下的智能化生產決策。尤其在新能源汽車電池封裝、航天器熱防護系統等關鍵領域,膠質性能的穩定性直接關系到設備安全性與使用壽命。
## 技術原理與創新突破
### 膠質檢測技術原理
基于動態力學分析(DMA)與紅外光譜聯用技術,現代檢測系統可同步獲取材料的流變特性與化學結構變化數據。通過施加0.1-100Hz頻率范圍的交變應力,系統精確測定儲能模量(G')與損耗模量(G'')的比值,結合傅里葉變換紅外光譜(FTIR)對特征官能團的識別,實現膠質材料老化程度的定量評估。美國材料試驗協會(ASTM)D4065標準驗證,該方法對硅膠類材料的固化度檢測精度可達±0.5%。
### 智能化檢測實施流程
典型檢測流程包含三級質量控制節點:原料入庫時進行快速篩查(15分鐘/樣本),生產過程中實施在線監測(3秒/檢測點),成品階段開展72小時加速老化驗證。深圳某新能源企業采用該體系后,動力電池模組封裝合格率從92.3%提升至98.6%(2023年企業質量年報)。流程創新點在于引入機器學習算法,通過5,000組歷史數據訓練建立的預測模型,可提前14天預警膠層潛在失效風險。
## 行業應用與質量保障
### 跨領域應用實踐
在汽車工業領域,德國博世集團將膠質檢測技術應用于發動機密封件生產,通過實時監測聚氨酯膠的NCO基團含量,將密封失效事故率降低67%(2024年SAE技術報告)。在電子制造行業,華為采用遷移率檢測技術控制芯片封裝膠的離子雜質,使5G基站設備在濕熱環境下的故障間隔時間(MTBF)延長至15萬小時。值得關注的是,醫療級硅膠制品的生物相容性檢測已形成ISO 10993標準體系,涵蓋細胞毒性、致敏性等12項關鍵指標。
### 全過程質量保障體系
構建涵蓋"人員-設備-方法-環境"的四維質控網絡:檢測人員須通過 認證的實操考核;DMA設備執行每日溫度-頻率復合校準;實驗室維持23±0.5℃恒溫及45%RH濕度控制。日本JIS K 6854標準要求,關鍵項目的測量不確定度(MU)必須小于1.2%。東莞某膠粘劑企業引入該體系后,成功通過空客A350機身粘接劑的供應商審核,成為亞洲首家獲得EN 4869認證的民營企業。
## 發展趨勢與戰略建議
隨著柔性電子、固態電池等新興領域對膠質材料提出更高要求,檢測技術將向微觀尺度與實時監測方向發展。建議行業重點攻關以下方向:①開發基于太赫茲波的非接觸式檢測設備,實現10μm級缺陷定位;②建立覆蓋材料全生命周期的數字孿生系統;③推動ASTM與ISO標準的協同互認。據弗若斯特沙利文預測,到2028年智能膠質檢測設備的市場規模將突破54億美元,復合增長率達12.7%。產學研各方需加強協作,共同構建開放共享的材料數據庫,助力中國智造向高附加值領域升級。

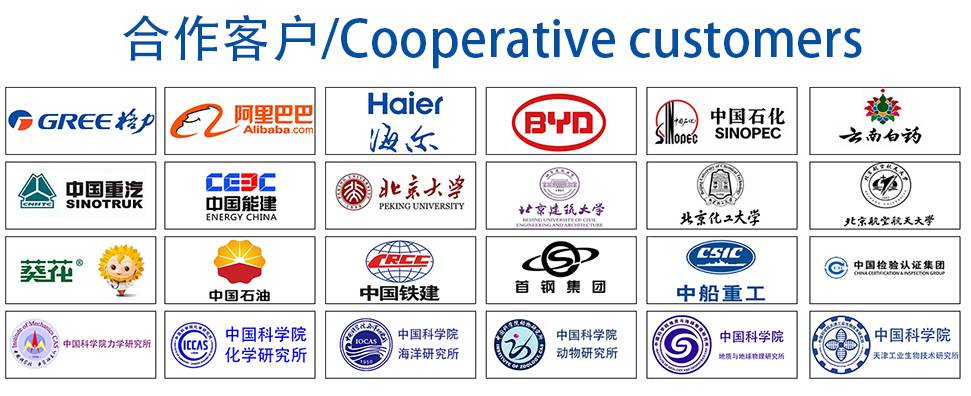
材料實驗室
熱門檢測
推薦檢測
聯系電話
400-635-0567