矩形壓力蒸汽滅菌器檢測
實(shí)驗(yàn)室擁有眾多大型儀器及各類分析檢測設(shè)備,研究所長期與各大企業(yè)、高校和科研院所保持合作伙伴關(guān)系,始終以科學(xué)研究為首任,以客戶為中心,不斷提高自身綜合檢測能力和水平,致力于成為全國科學(xué)材料研發(fā)領(lǐng)域服務(wù)平臺(tái)。
立即咨詢網(wǎng)頁字號(hào):【大 中 小 】 | 【打印】 【關(guān)閉】 微信掃一掃分享:
注意:因業(yè)務(wù)調(diào)整,暫不接受個(gè)人委托測試望見諒。
聯(lián)系中化所
矩形壓力蒸汽滅菌器檢測的重要性與核心內(nèi)容
矩形壓力蒸汽滅菌器作為醫(yī)療機(jī)構(gòu)、實(shí)驗(yàn)室和工業(yè)生產(chǎn)中關(guān)鍵的滅菌設(shè)備,其性能直接關(guān)系到物品的無菌性和操作安全性。由于滅菌器長期處于高溫、高壓的工作環(huán)境,內(nèi)部結(jié)構(gòu)、密封性能及控制系統(tǒng)均可能發(fā)生老化或故障,因此定期開展檢測是確保滅菌效果、延長設(shè)備壽命的必要措施。依據(jù)《壓力容器安全技術(shù)監(jiān)察規(guī)程》(TSG 21)和GB 8599-2008《大型蒸汽滅菌器技術(shù)要求》等標(biāo)準(zhǔn),檢測工作需涵蓋物理參數(shù)驗(yàn)證、生物監(jiān)測、化學(xué)監(jiān)測及安全性評(píng)估等多個(gè)維度,形成完整的質(zhì)量控制體系。
核心檢測項(xiàng)目及技術(shù)要求
1. 物理參數(shù)檢測
通過溫度-壓力數(shù)據(jù)記錄儀對滅菌過程的溫度均勻性、壓力穩(wěn)定性進(jìn)行全程監(jiān)測。要求滅菌室121℃條件下的溫度波動(dòng)范圍≤±1℃,壓力波動(dòng)控制在±0.01MPa以內(nèi),維持時(shí)間需達(dá)到滅菌程序設(shè)定值的±5%誤差范圍。特別關(guān)注滅菌器四角與中心點(diǎn)的溫度差異,最大偏差不得超過2℃。
2. 生物指示劑驗(yàn)證
采用嗜熱脂肪芽孢桿菌(ATCC 7953)作為標(biāo)準(zhǔn)生物指示物,按GB/T 19972要求進(jìn)行挑戰(zhàn)性測試。滅菌程序結(jié)束后,生物指示劑培養(yǎng)56℃±1℃環(huán)境下48小時(shí),所有樣本均需顯示無菌生長。檢測頻次建議每月至少1次,重大維修后須立即執(zhí)行。
3. 化學(xué)監(jiān)測系統(tǒng)校驗(yàn)
使用標(biāo)準(zhǔn)化學(xué)指示卡/膠帶驗(yàn)證蒸汽滲透性和溫度響應(yīng)特性,要求第5類綜合指示卡在滅菌周期結(jié)束后完全達(dá)到標(biāo)準(zhǔn)色塊變化。同時(shí)需檢測Bowie-Dick試驗(yàn)包的顯色均勻性,用于評(píng)估預(yù)真空型滅菌器的空氣排出效果。
4. 設(shè)備性能綜合測試
? 空載熱分布測試:驗(yàn)證腔體內(nèi)部溫度均勻性
? 滿載熱穿透測試:模擬實(shí)際裝載狀態(tài)下的滅菌效果
? 真空泄漏率檢測:預(yù)真空型設(shè)備需≤1.3mbar/min
? 干燥度評(píng)估:滅菌后器械包殘余濕度應(yīng)<3%
5. 安全防護(hù)裝置檢測
檢查壓力安全閥啟閉壓力(應(yīng)≤標(biāo)稱工作壓力的1.1倍)、壓力表精度等級(jí)(不低于1.6級(jí))、門密封系統(tǒng)完整性(保壓測試壓降≤0.5kPa/min)、聯(lián)鎖保護(hù)裝置響應(yīng)速度(緊急泄壓時(shí)間<10秒)等關(guān)鍵安全指標(biāo)。
6. 周期性強(qiáng)制檢測
根據(jù)TSG 21規(guī)定,壓力容器本體需每3年進(jìn)行耐壓試驗(yàn)(1.25倍工作壓力)和宏觀檢查;安全閥每年校驗(yàn)1次;壓力表每半年檢定1次。同時(shí)需定期更換門密封圈、過濾器等易損件,確保設(shè)備持續(xù)符合YY 0503-2016《醫(yī)用蒸汽滅菌器》要求。
檢測結(jié)果分析與改進(jìn)措施
每次檢測需形成包含原始數(shù)據(jù)、過程曲線、異常點(diǎn)分析的完整報(bào)告。對溫度均勻性不達(dá)標(biāo)的情況,需排查加熱管工作狀態(tài)或蒸汽飽和度;生物監(jiān)測陽性結(jié)果需立即啟動(dòng)滅菌程序有效性調(diào)查,追溯至少過去30天的滅菌記錄。建議建立設(shè)備性能趨勢分析數(shù)據(jù)庫,通過歷史數(shù)據(jù)比對提前預(yù)判潛在故障。

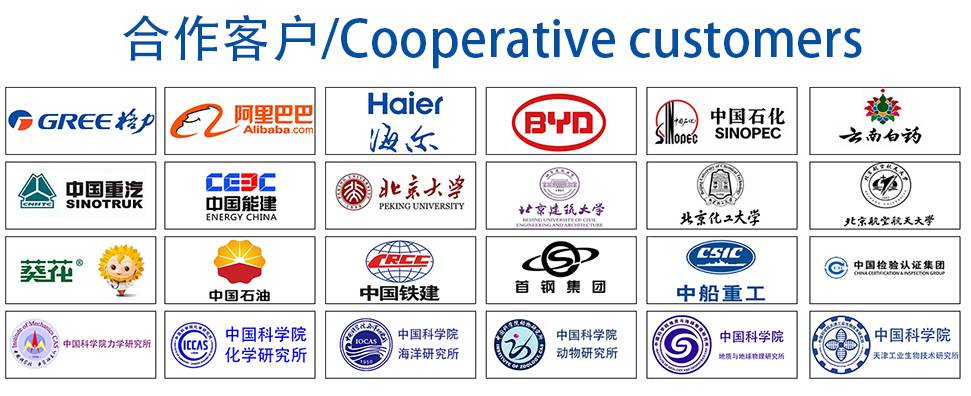