開槽機檢測的重要性與實施流程
開槽機作為工業制造、建筑裝修及管道安裝等領域的關鍵設備,其性能穩定性直接影響加工效率和產品質量。隨著設備使用時間的增加,零部件磨損、傳動系統誤差、電氣控制異常等問題可能逐漸顯現,因此定期開展開槽機檢測是保障安全生產、延長設備壽命的必要措施。通過系統化的檢測項目,企業能夠精準定位設備隱患,優化維護策略,避免因設備故障導致的生產停滯或安全事故。
核心檢測項目分類
1. 機械結構完整性檢測
采用激光對中儀和振動分析儀對主軸同心度、導軌平行度進行測量,要求徑向跳動量≤0.02mm。使用超聲波探傷儀對機身焊接部位進行無損檢測,發現裂紋深度超0.5mm需立即修復。同步檢查刀盤鎖緊裝置的有效性,測試夾持力是否達到設計標準的1200N·m。
2. 動力系統性能測試
通過功率分析儀監測電機負載特性,在額定轉速3000rpm工況下,三相電流不平衡度應<5%。使用紅外熱像儀對傳動皮帶輪進行溫度掃描,異常溫升超過環境溫度30℃需排查軸承狀態。液壓系統需檢測壓力波動范圍,確保工作壓力穩定在15±0.5MPa區間。
3. 加工精度驗證
采用標準試件進行切削試驗,用三坐標測量機評估槽寬公差(±0.05mm)和槽深一致性(±0.1mm)。通過表面粗糙度儀檢測加工面Ra值,要求不超過3.2μm。動態測試時,用高速攝影機記錄刀頭振動頻率,振幅超過50μm需進行動平衡校正。
4. 安全防護裝置檢測
測試急停按鈕響應時間不超過0.5秒,防護罩聯鎖裝置需保證開門斷電時間<0.1秒。使用接地電阻測試儀驗證設備接地連續性,要求電阻值≤1Ω。對光電保護裝置進行遮蔽試驗,確保有效觸發距離誤差在±10mm范圍內。
5. 智能化功能診斷
通過PLC通訊接口讀取設備運行日志,分析伺服系統定位誤差歷史數據。測試數控系統G代碼執行精度,驗證圓弧插補軌跡偏差是否在0.02mm以內。對自動潤滑系統進行流量監測,單點注油量誤差不得超過標稱值的15%。
檢測周期與標準參考
建議連續作業設備每500小時進行預防性檢測,參照GB 5226.1-2019機械電氣安全標準、JB/T 8832-2019組合機床通用技術條件等規范。對于關鍵安全部件,如制動器和過載保護裝置,應縮短至每300小時專項檢查。所有檢測數據需建立電子檔案,運用大數據分析預測主要部件剩余壽命。

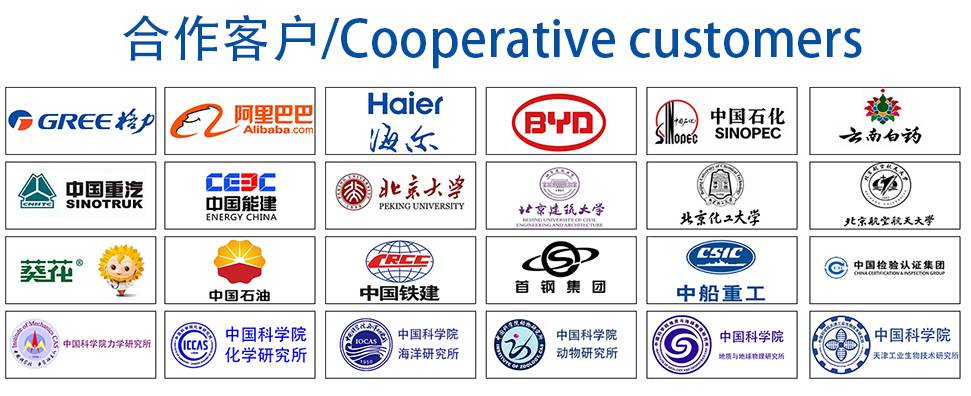