汽車用制動器襯片檢測的重要性
作為汽車制動系統的核心安全部件,制動器襯片的性能直接關系到行車安全與駕駛體驗。根據國家強制標準GB 5763-2018《汽車用制動器襯片》規定,所有上市銷售的剎車片必須通過20余項嚴格檢測,涉及摩擦性能、耐久性、環保指標等關鍵參數。隨著汽車工業向新能源、輕量化方向發展,對剎車片的熱穩定性、抗衰減能力和NVH(噪音振動)表現提出了更高要求,這使得檢測工作不僅要符合現行標準,更要適應技術迭代帶來的新型檢測需求。
核心檢測項目解析
1. 摩擦性能測試
采用定速式摩擦試驗機,在100-350℃溫度范圍內模擬不同工況,檢測摩擦系數(μ)隨溫度變化的穩定性。依據QC/T 237-2021標準,要求摩擦系數波動范圍≤±15%,特別在高溫段(300℃以上)不得出現明顯衰減。最新檢測方法增加了制動壓力脈動模擬,更真實反映緊急制動時的動態摩擦特性。
2. 磨損率測定
通過臺架試驗累計500次制動循環,使用激光輪廓儀測量襯片厚度變化。行業標準要求乘用車剎車片平均磨損率≤0.15mm/萬公里,商用車重型剎車片需≤0.25mm/萬公里。值得注意的是,新型陶瓷配方材料的磨損率檢測需特別關注冷態磨損特性,這與傳統半金屬材料存在顯著差異。
3. 熱穩定性驗證
在650℃高溫爐中進行連續24小時老化試驗,檢測材料膨脹率、硬度變化及表面裂紋情況。優質產品熱膨脹系數應≤3×10??/℃,硬度變化率≤15%。針對電動汽車能量回收系統導致的低頻次高負荷制動特點,新增了間歇性高溫沖擊試驗(650℃→常溫循環100次)。
4. 剪切強度檢測
使用萬能材料試驗機進行背板與摩擦材料的剝離測試,根據GB/T 22309標準,剪切強度需≥6.5MPa。新能源汽車因整備質量增加,部分車型要求提升至8.0MPa以上。檢測過程中需特別注意界面粘接層的微觀結構分析,防止出現氣孔、夾雜等隱性缺陷。
5. 環保性能評估
依據歐盟REACH法規和GB/T 30512-2014標準,重點檢測銅含量(需<0.5%)、石棉殘留(必須未檢出)及揮發性有機物(VOCs)。最新檢測體系新增了制動粉塵PM2.5排放測試,要求每公里制動產生的可吸入顆粒物≤5mg,這對摩擦材料的配方設計提出了革命性要求。
檢測技術發展趨勢
隨著智能化檢測設備的普及,基于機器視覺的表面缺陷自動識別系統已實現97%以上的檢測準確率。虛擬現實(VR)技術被應用于臺架試驗工況模擬,可精確還原冰雪路面、連續彎道等復雜場景。2023年實施的《智能網聯汽車制動系統檢測規范》更要求剎車片配備芯片級傳感器,實現磨耗狀態的實時監測與預警。
專業的檢測機構不僅需要配備價值千萬的慣性試驗臺、噪聲振動分析系統等硬件設備,更要建立覆蓋原材料采購、生產工藝、成品檢測的全鏈條質量追溯體系。消費者在選擇剎車片時,應重點關注檢測報告中的摩擦系數曲線、高溫衰減率、環保認證等核心指標,確保產品既符合國標要求,又能滿足特定車型的個性化制動需求。

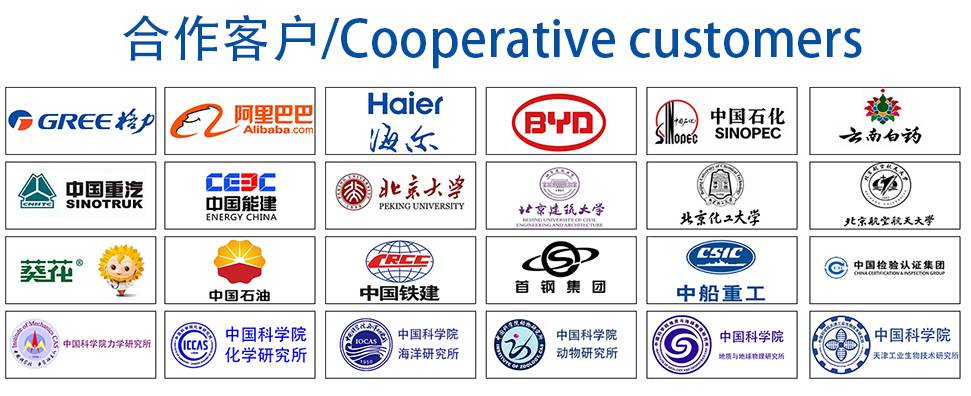