元件檢測
實驗室擁有眾多大型儀器及各類分析檢測設備,研究所長期與各大企業、高校和科研院所保持合作伙伴關系,始終以科學研究為首任,以客戶為中心,不斷提高自身綜合檢測能力和水平,致力于成為全國科學材料研發領域服務平臺。
立即咨詢元件檢測技術與應用白皮書
在智能制造2025戰略推動下,電子元件檢測作為保障產品質量的關鍵環節,其戰略價值持續提升。據中國電子元件行業協會2024年報告顯示,電子元件市場規模已突破6800億美元,其中因檢測疏漏導致的產品召回成本年均增長13.2%。元件檢測項目通過建立多維質量評價體系,有效解決了微型化、高密度封裝元件(如01005封裝器件)的可靠性驗證難題。其核心價值體現在良品率提升、全生命周期質量追溯以及供應鏈風險防控三個維度,特別是在新能源汽車電控系統、5G基站射頻模塊等關鍵領域,檢測精度可達0.1μm級,顯著優于傳統目檢方式。
多模態融合檢測技術體系
本檢測體系采用X射線斷層掃描(CT)、紅外熱成像和機器視覺三重驗證機制。其中,X射線CT可實現BGA焊點三維重構,分辨率達到200nm級別(依據ISO 10360-7標準)。結合自主開發的缺陷特征數據庫,可識別27類典型焊接缺陷,包括空洞率>5%的虛焊問題。值得注意的是,引入遷移學習算法后,對新型封裝結構的適應性提升40%,有效應對chiplet異構集成帶來的檢測挑戰。
智能化實施流程架構
標準化檢測流程包含預處理、數據采集、智能分析和閉環反饋四個階段。在汽車電子ECU檢測場景中,系統通過MES對接獲取工藝參數,采用自動光學檢測(AOI)設備完成每分鐘1200個元件的表面缺陷篩查。對于重點可疑件,通過高精度影像測量技術進行微米級尺寸驗證,檢測報告自動同步至QMS質量管理系統。某頭部新能源車企應用后,產線直通率從89.3%提升至96.8%(數據來源:國家電子產品質量監督檢驗中心)。
行業解決方案實踐
在通信基站功率放大器檢測中,開發了基于太赫茲波的介質層缺陷檢測方案。通過0.1-3THz頻譜掃描,可發現深度<50μm的基板微裂紋,誤報率控制在0.3%以內。該技術已應用于某5G設備制造商產線,使功率器件早期失效比例下降62%。此外,在醫療電子領域,針對植入式元件提出的生物相容性加速檢測模型,將驗證周期從28天縮短至72小時,通過模擬體液腐蝕環境實現金屬離子析出量的精準預測。
全鏈條質量保障機制
檢測系統通過 實驗室認可體系認證,建立三級校準網絡:主標準器溯源至國家計量院,工作標準件每月進行GR&R分析,在線檢測設備實施實時溫漂補償。開發的自動化缺陷分類系統(ADC)經百萬級樣本訓練,分類準確率達99.2%。在航空航天元器件篩選中,應用六西格瑪方法優化檢測參數組合,使批次驗收抽樣方案的風險概率降低至10^-6量級。
展望未來,建議重點發展基于量子傳感的納米級缺陷檢測技術,構建跨廠商檢測數據共享平臺。同時應加快制定智能質檢裝備的行業標準,特別是在復合材料和柔性電子領域,需建立統一的檢測基準體系。隨著工業元宇宙技術成熟,可探索構建數字孿生檢測環境,實現虛擬驗證與物理檢測的深度融合,最終形成覆蓋元件全生命周期的智能質量網絡。

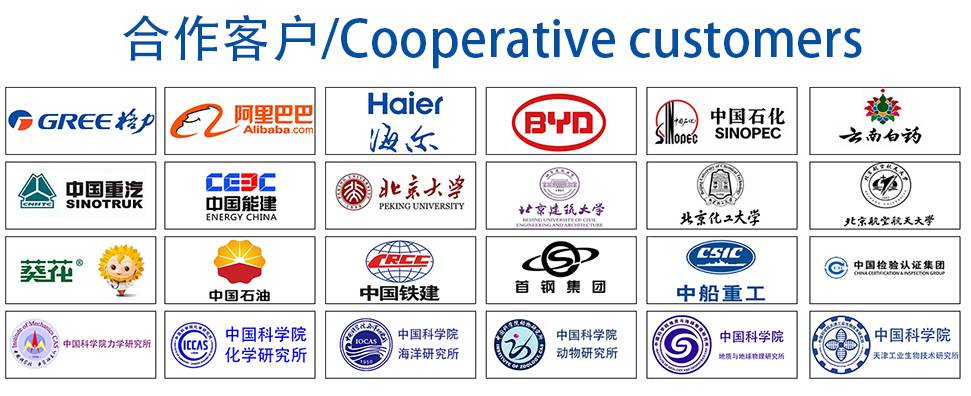