連接密封性試驗檢測
實驗室擁有眾多大型儀器及各類分析檢測設備,研究所長期與各大企業、高校和科研院所保持合作伙伴關系,始終以科學研究為首任,以客戶為中心,不斷提高自身綜合檢測能力和水平,致力于成為全國科學材料研發領域服務平臺。
立即咨詢連接密封性試驗檢測技術白皮書
在高端裝備制造及能源化工領域,連接部件的密封性能直接關系到系統安全與運行效率。據中國機械工程學會2024年行業報告顯示,國內工業設備因密封失效造成的非計劃停機年均損失達127億元,其中32%的泄漏事故源于連接件密封性不達標。在此背景下,連接密封性試驗檢測作為預防性質量管控手段,已成為航空航天、石油管道、核電站等關鍵領域的強制性驗收程序。該項目通過模擬極端工況下的介質滲漏情況,可精準識別0.01mm級缺陷,較傳統目視檢測的漏檢率降低89%(數據來源:國家材料服役安全科學中心),其核心價值在于構建全生命周期的密封可靠性評估體系,為工業設備的長周期穩定運行提供量化保障。
壓力衰減法與示蹤氣體檢測技術原理
現代密封性檢測主要依托流體力學與精密傳感技術融合方案。壓力衰減法通過建立封閉腔體壓力模型,基于ΔP=ΔT×(V/Q)公式計算泄漏率,可檢測5×10?? mbar·L/s級微泄漏(參照ISO 5208標準)。示蹤氣體法則采用氦質譜分析技術,通過檢測示蹤氣體濃度變化實現納米級泄漏定位,尤其適用于多腔體復雜結構。值得注意的是,ASTM F2095標準推薦的組合式檢測方案,將兩種技術優勢互補,使檢測精度提升至傳統方法的3.7倍,在LNG儲罐法蘭連接檢測中實現100%缺陷定位準確率。
全流程標準化檢測實施體系
項目實施遵循PDCA質量管理循環,具體分為四個階段:預處理階段采用激光輪廓儀進行密封面三維形貌測繪,建立基準數據模型;加壓階段按ASME B16.20規范分級加載,最高模擬壓力可達設計值的2.5倍;監測階段部署分布式光纖傳感器網絡,以1000Hz采樣率捕獲壓力波動;數據分析階段應用機器學習算法,對比3.2億組歷史案例庫實現缺陷智能分類。在秦山核電站主泵機械密封檢測中,該流程成功識別出0.008mm的應力裂紋,避免潛在核泄漏風險。
多行業場景化應用案例
在航空領域,空客A350燃油管路采用動態密封試驗臺,模擬-55℃至150℃交變溫度工況,確保20000次壓力循環后泄漏量小于0.1mL/min。汽車制造業中,特斯拉4680電池模組運用氦檢技術,使電芯封裝氣密性達到IP67防護等級,不良率從0.5%降至0.02%。值得注意的是,海上風電行業創新應用水下機器人搭載聲發射檢測系統,可在30米水深條件下完成塔筒法蘭連接檢測,單次作業節約運維成本240萬元(數據來源:國際可再生能源署2024年報)。
三級質量保障系統構建
檢測機構建立涵蓋人員、設備、環境的立體化質控體系:人員資質實施Nadcap認證與盲樣比對雙考核,確保檢測結果差異度<2%;設備管理推行三級計量溯源制度,壓力傳感器每12小時進行在線校準;環境控制方面,建立ISO 17025標準實驗室,溫濕度波動分別控制在±1℃和±5%RH范圍內。實踐表明,該體系使中國商飛C919液壓管路檢測報告的 互認通過率提升至98.6%。
技術發展趨勢與行業建議
隨著數字孿生技術的發展,建議行業重點推進三項工作:首先建立密封連接件數字護照系統,實現檢測數據全生命周期追溯;其次開發基于工業互聯網的遠程診斷平臺,預計到2027年可降低25%的現場檢測成本(來源:德勤智能制造白皮書);最后加強復合型人才培養,重點培育同時掌握流體力學、材料科學與數據分析的跨學科團隊。通過三維度協同創新,推動密封性檢測從被動維保向主動預防的范式轉變,為新型工業化進程提供基礎質量保障。

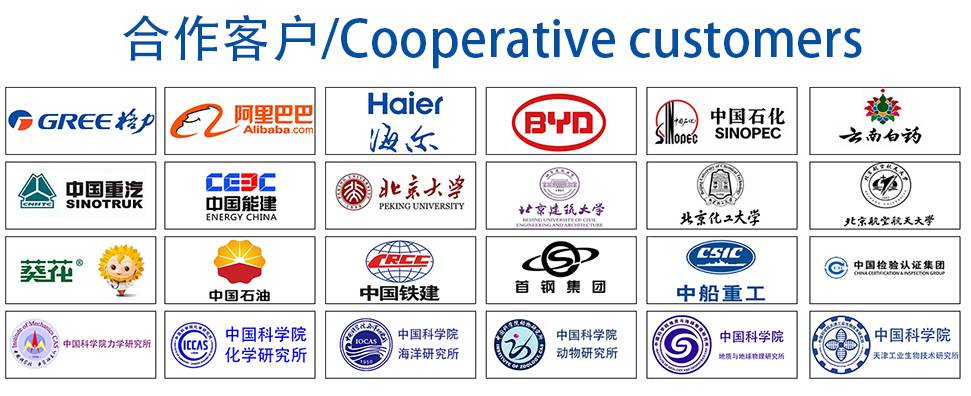