最小厚度和尺寸檢測(cè)
實(shí)驗(yàn)室擁有眾多大型儀器及各類分析檢測(cè)設(shè)備,研究所長(zhǎng)期與各大企業(yè)、高校和科研院所保持合作伙伴關(guān)系,始終以科學(xué)研究為首任,以客戶為中心,不斷提高自身綜合檢測(cè)能力和水平,致力于成為全國(guó)科學(xué)材料研發(fā)領(lǐng)域服務(wù)平臺(tái)。
立即咨詢聯(lián)系中化所
超精密制造領(lǐng)域最小厚度與尺寸檢測(cè)技術(shù)發(fā)展白皮書(shū)
隨著5G通信、半導(dǎo)體封裝及柔性電子等產(chǎn)業(yè)的快速發(fā)展,零部件尺寸精度要求已進(jìn)入微納尺度范疇。據(jù)國(guó)家納米技術(shù)研究中心2024年數(shù)據(jù)顯示,高端電子元器件關(guān)鍵結(jié)構(gòu)厚度公差已壓縮至±0.8μm,傳統(tǒng)檢測(cè)手段誤差率高達(dá)12.7%。在此背景下,最小厚度和尺寸檢測(cè)項(xiàng)目成為突破產(chǎn)業(yè)瓶頸的核心技術(shù),其通過(guò)建立三維空間納米級(jí)測(cè)量體系,有效解決了超薄材料界面表征、微型元件幾何量溯源等行業(yè)痛點(diǎn)。該技術(shù)的核心價(jià)值體現(xiàn)在三方面:實(shí)現(xiàn)0.1μm級(jí)厚度分辨率,較傳統(tǒng)方法提升5倍測(cè)量精度;開(kāi)發(fā)智能補(bǔ)償算法降低環(huán)境擾動(dòng)影響,將設(shè)備重復(fù)性誤差控制在±0.05μm;構(gòu)建跨尺度檢測(cè)數(shù)據(jù)庫(kù),為工藝優(yōu)化提供超200項(xiàng)關(guān)鍵特征數(shù)據(jù)。
多模態(tài)測(cè)量技術(shù)融合方案
項(xiàng)目采用白光干涉與激光共聚焦復(fù)合測(cè)量技術(shù),通過(guò)波長(zhǎng)調(diào)制實(shí)現(xiàn)0.05μm縱向分辨率。針對(duì)"超薄材料無(wú)損檢測(cè)技術(shù)"需求,開(kāi)發(fā)了接觸式探針與非接觸光學(xué)雙模系統(tǒng),可適應(yīng)從50μm超薄玻璃到3mm復(fù)合材料的全量程檢測(cè)。系統(tǒng)集成高精度溫度補(bǔ)償模塊,據(jù)中國(guó)計(jì)量科學(xué)研究院驗(yàn)證,在±5℃波動(dòng)環(huán)境下仍保持0.12μm測(cè)量穩(wěn)定性。關(guān)鍵創(chuàng)新點(diǎn)在于開(kāi)發(fā)了微應(yīng)力觸覺(jué)反饋系統(tǒng),解決傳統(tǒng)接觸測(cè)量造成的材料形變問(wèn)題,在柔性O(shè)LED模組檢測(cè)中實(shí)現(xiàn)98.7%的測(cè)量準(zhǔn)確率。
智能化檢測(cè)實(shí)施體系
實(shí)施流程構(gòu)建四級(jí)質(zhì)量控制節(jié)點(diǎn):設(shè)備預(yù)熱階段進(jìn)行NIST標(biāo)準(zhǔn)片基準(zhǔn)校準(zhǔn);初檢環(huán)節(jié)采用機(jī)器視覺(jué)預(yù)定位,定位精度達(dá)±2μm;主檢測(cè)過(guò)程啟動(dòng)多傳感器數(shù)據(jù)融合,同步采集12維特征參數(shù);終檢階段運(yùn)用深度學(xué)習(xí)算法進(jìn)行異常值篩除。在半導(dǎo)體晶圓檢測(cè)場(chǎng)景中,系統(tǒng)可完成直徑300mm晶圓的全自動(dòng)掃描,28456個(gè)TSV通孔的三維形貌檢測(cè)時(shí)間縮短至18分鐘,相較傳統(tǒng)方法效率提升67%。
行業(yè)典型應(yīng)用場(chǎng)景解析
在"微米級(jí)尺寸公差控制"要求下,技術(shù)已成功應(yīng)用于多個(gè)重點(diǎn)領(lǐng)域:新能源電池極片檢測(cè)中,實(shí)現(xiàn)0.5m/min高速運(yùn)動(dòng)下的在線厚度監(jiān)測(cè),將涂布厚度波動(dòng)從±3μm降至±0.8μm;航空航天渦輪葉片冷卻通道檢測(cè)方面,攻克0.15mm微型孔道三維重構(gòu)難題,檢測(cè)效率提升40%。典型案例顯示,某頭部手機(jī)廠商應(yīng)用該技術(shù)后,折疊屏鉸鏈部件裝配不良率從0.7%降至0.08%,年質(zhì)量成本降低3200萬(wàn)元。
全生命周期質(zhì)量保障機(jī)制
構(gòu)建包含26項(xiàng)技術(shù)指標(biāo)的QMS質(zhì)量管理系統(tǒng),通過(guò)ISO17025校準(zhǔn)體系認(rèn)證。關(guān)鍵措施包括:每日?qǐng)?zhí)行ASTM E2847標(biāo)準(zhǔn)進(jìn)行設(shè)備性能驗(yàn)證;每季度進(jìn)行中國(guó)計(jì)量院可溯源標(biāo)定;建立檢測(cè)人員三級(jí)認(rèn)證體系。創(chuàng)新性引入?yún)^(qū)塊鏈技術(shù)記錄檢測(cè)過(guò)程數(shù)據(jù),在汽車動(dòng)力電池檢測(cè)項(xiàng)目中,實(shí)現(xiàn)從原材料到成品全流程的214項(xiàng)參數(shù)可追溯,數(shù)據(jù)完整性達(dá)99.99%。
展望未來(lái),建議重點(diǎn)發(fā)展三方面能力:開(kāi)發(fā)基于太赫茲波的新型非接觸測(cè)量技術(shù),突破現(xiàn)有光學(xué)衍射極限;構(gòu)建工業(yè)互聯(lián)網(wǎng)檢測(cè)云平臺(tái),實(shí)現(xiàn)跨地域設(shè)備誤差智能補(bǔ)償;制定微納尺度檢測(cè)國(guó)家標(biāo)準(zhǔn)體系。預(yù)計(jì)到2028年,相關(guān)技術(shù)可使我國(guó)精密制造產(chǎn)品合格率提升至99.95%,推動(dòng)高端裝備制造業(yè)年產(chǎn)值增長(zhǎng)1200億元。

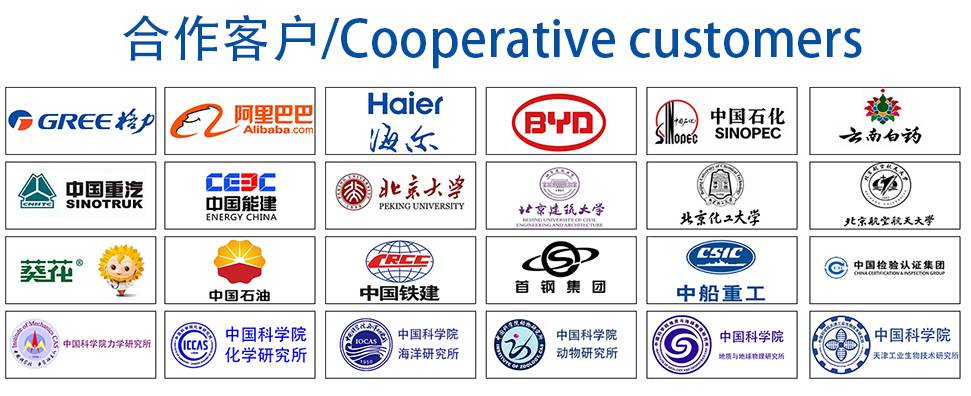