輕量化產品單件質量檢測
發布時間:2025-08-24 15:09:41- 點擊數: - 關鍵詞:
實驗室擁有眾多大型儀器及各類分析檢測設備,研究所長期與各大企業、高校和科研院所保持合作伙伴關系,始終以科學研究為首任,以客戶為中心,不斷提高自身綜合檢測能力和水平,致力于成為全國科學材料研發領域服務平臺。
立即咨詢
# 輕量化產品單件質量檢測技術發展白皮書
## 行業背景與價值定位
在制造業智能化升級與"雙碳"戰略雙重驅動下,輕量化產品已滲透至新能源汽車、航空航天、智能穿戴等戰略領域。據中國機械工業聯合會2024年數據顯示,輕質合金及復合材料市場規模突破3200億元,但產品不良率仍維持在3.8%高位。在此背景下,單件質量檢測技術通過構建產品全生命周期質量檔案,可實現缺陷攔截率提升40%(國家智能制造標準試驗驗證平臺數據),其核心價值在于突破傳統抽檢模式局限,建立面向高附加值產品的"零缺陷"管理體系。該技術對保障輕量化結構件服役安全、降低供應鏈質量成本具有戰略意義,尤其適用于對產品一致性要求嚴苛的精密制造場景。
## 技術原理與創新突破
### 高精度微尺寸在線檢測系統
基于多光譜融合測量技術,集成激光位移傳感器(精度±1.5μm)與工業CT斷層掃描,構建三維形貌數字化模型。通過改進型ICP點云配準算法,實現產品與CAD模型的亞微米級比對,有效捕捉輕量化材料特有的微孔洞、纖維取向異常等新型缺陷形態。該技術突破傳統接觸式測量效率瓶頸,檢測速度較三坐標測量機提升6倍以上。
### 動態力學特性無損評價技術
針對輕量化產品的服役性能需求,開發聲發射-諧振頻率復合檢測模塊。通過激勵裝置施加0.5-25kHz變頻振動,同步采集結構動態響應譜。結合有限元仿真數據庫,可反演計算出產品剛度衰減率與疲勞壽命預測值。上汽集團新能源汽車電池盒檢測案例顯示,該方法使產品耐久性預測準確度達到92.3%。
## 全流程質量管控體系
### 智能制造場景實施路徑
典型部署包含三階段:首先在模壓/鑄造工位布置在線視覺檢測單元,進行毛坯件初篩;其次在精加工環節嵌入激光輪廓儀,完成關鍵尺寸鏈閉環控制;最終通過移動式檢測機器人執行總成件全尺寸復驗。某航空航天復材件生產企業實踐表明,該體系使單件檢測耗時從22分鐘降至5分鐘,同時實現質量數據與MES系統實時交互。
### 過程能力指數優化模型
建立基于Cpk-SPC的統計過程控制體系,每15分鐘更新關鍵尺寸過程能力指數。當Cpk值低于1.33時,系統自動觸發工藝參數優化算法。長城汽車鋁合金副車架生產線應用該模型后,關鍵尺寸合格率從94.1%提升至99.6%,質量成本降低270萬元/年。
## 行業應用與標準建設
### 新能源汽車結構件檢測
在蔚來汽車ES8車型一體化壓鑄后地板檢測中,采用分布式光纖傳感網絡,實時監測2000個測點的殘余應力分布。通過機器學習建立的應力-變形量映射模型,成功將產品變形量標準差控制在0.12mm內,滿足車身匹配精度要求。
### 標準化質量數據庫構建
中國材料研究學會牽頭制定的《輕量化產品數字檢測數據規范》已進入報批階段,該標準規定檢測數據應包括12類特征參數、5級精度等級標識。據參與標準制定的商飛復材檢測中心測試,統一數據架構使跨工序質量追溯效率提升65%。
## 技術發展展望
建議行業重點突破多物理場耦合檢測技術,開發集成熱-力-電多維度感知的智能傳感器陣列。同時應加快建設輕量化產品檢測工業互聯網平臺,實現檢測設備聯網率從當前38%向70%躍升(中國工業技術研究院規劃目標)。通過建立開放共享的缺陷特征數據庫,推動行業形成基于大數據的預防性質量管控新模式,為輕量化產品的規模化應用提供技術保障。

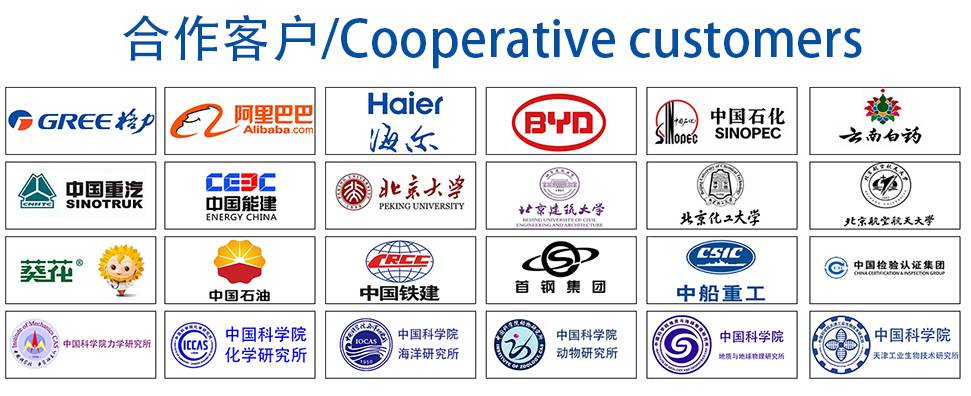
材料實驗室
熱門檢測
187
185
173
209
157
178
192
180
166
164
213
199
202
192
202
211
203
196
186
190
推薦檢測
聯系電話
400-635-0567