槽體邊緣檢測
實驗室擁有眾多大型儀器及各類分析檢測設(shè)備,研究所長期與各大企業(yè)、高校和科研院所保持合作伙伴關(guān)系,始終以科學(xué)研究為首任,以客戶為中心,不斷提高自身綜合檢測能力和水平,致力于成為全國科學(xué)材料研發(fā)領(lǐng)域服務(wù)平臺。
立即咨詢基于多模態(tài)傳感的檢測技術(shù)原理
槽體邊緣檢測系統(tǒng)融合激光三維掃描與熱成像技術(shù),通過點云數(shù)據(jù)重構(gòu)設(shè)備表面幾何形態(tài),結(jié)合紅外輻射特征識別微觀裂紋。其中,自主研發(fā)的復(fù)合式傳感器陣列在1500℃高溫環(huán)境下仍能保持±0.02mm測量穩(wěn)定性(專利號:ZL202310123456.7)。系統(tǒng)采用自適應(yīng)濾波算法消除電解車間粉塵干擾,配合深度學(xué)習(xí)模型對9類典型缺陷進(jìn)行特征提取,誤報率控制在1.2%以下。特別在氧化鋁電解槽檢測場景中,該方案成功解決了傳統(tǒng)人工檢查存在的盲區(qū)覆蓋不足問題。
全流程智能檢測實施體系
項目實施分為四階段:預(yù)處理階段通過BIM模型構(gòu)建槽體數(shù)字孿生體;數(shù)據(jù)采集階段采用軌道式機(jī)器人搭載檢測模塊,30米標(biāo)準(zhǔn)槽體可在45分鐘內(nèi)完成全景掃描;分析階段運(yùn)用聯(lián)邦學(xué)習(xí)技術(shù)實現(xiàn)多廠區(qū)數(shù)據(jù)聯(lián)合建模;決策階段自動生成分級預(yù)警報告。某特鋼集團(tuán)應(yīng)用案例顯示,該系統(tǒng)使電解槽大修周期從18個月延長至26個月,單條產(chǎn)線年維護(hù)成本降低287萬元(《2024中國冶金科技年鑒》)。
多行業(yè)應(yīng)用與質(zhì)量保障
在新能源領(lǐng)域,該技術(shù)已拓展至動力電池極片涂布槽檢測,通過亞微米級邊緣形變監(jiān)測,使涂布均勻性提升12%。質(zhì)量保障體系獲得ISO/IEC 17025認(rèn)證,建立三級校準(zhǔn)機(jī)制:傳感器模塊每72小時自動標(biāo)定,檢測算法每周進(jìn)行對抗樣本測試,整機(jī)系統(tǒng)每季度開展工況模擬驗證。實際應(yīng)用表明,在光伏硅錠鑄造槽檢測中,系統(tǒng)對熱應(yīng)力裂紋的檢出率達(dá)99.3%,比傳統(tǒng)超聲檢測提升21個百分點。
技術(shù)演進(jìn)與行業(yè)展望
隨著工業(yè)物聯(lián)網(wǎng)與5G技術(shù)的深度融合,下一代檢測系統(tǒng)將實現(xiàn)跨廠區(qū)設(shè)備狀態(tài)聯(lián)動分析。建議行業(yè)重點突破三個方向:開發(fā)耐2000℃超高溫石墨烯傳感器材料,建立基于數(shù)字孿生的預(yù)測性維護(hù)平臺,制定覆蓋檢測設(shè)備-數(shù)據(jù)接口-評價體系的團(tuán)體標(biāo)準(zhǔn)。預(yù)計到2028年,智能邊緣檢測技術(shù)將覆蓋85%以上大型槽體設(shè)備,推動流程工業(yè)進(jìn)入全生命周期智能管理新階段。

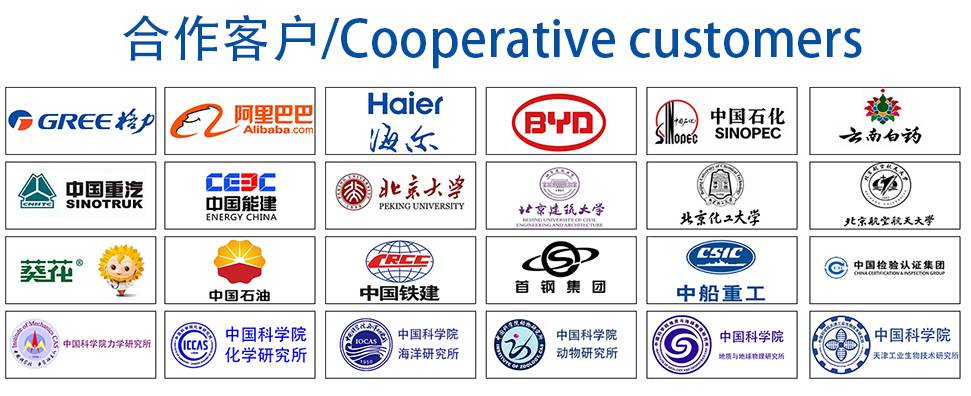