尺寸和偏差檢測
實驗室擁有眾多大型儀器及各類分析檢測設備,研究所長期與各大企業、高校和科研院所保持合作伙伴關系,始終以科學研究為首任,以客戶為中心,不斷提高自身綜合檢測能力和水平,致力于成為全國科學材料研發領域服務平臺。
立即咨詢尺寸和偏差檢測:智能制造時代的質量保障基石
在工業4.0與智能制造深度融合的背景下,尺寸和偏差檢測已成為現代制造業質量控制的核心環節。據中國機械工業聯合會2024年行業白皮書顯示,我國高端裝備制造領域因尺寸偏差導致的產品返修成本年均超1200億元,占行業總成本的7.2%。尤其在新能源汽車、航空航天等精密制造領域,零件尺寸公差普遍要求達到±0.005mm級精度,傳統人工檢測方式已無法滿足生產需求。通過構建智能化的尺寸檢測體系,企業可實現質量數據實時反饋、工藝參數動態調整以及生產節拍優化,單條生產線良品率最高可提升18%(賽迪研究院,2023)。該項目不僅填補了國內在高精度在線檢測領域的技術空白,更為產業鏈協同創新提供了關鍵數據支撐。
多模態融合檢測技術原理
現代尺寸檢測系統采用光學測量、機器視覺與接觸式探針的協同工作機制。基于相位輪廓測量法的激光三角測距模塊可實現0.1μm級分辨率,配合高幀頻工業相機(2000fps)捕捉動態形變特征。在汽車變速箱齒輪檢測場景中,系統通過三維點云重構技術建立齒形誤差模型,運用非接觸式測量可完整記錄1024個齒面的微觀形貌數據。值得關注的是,多維數據融合算法能將空間坐標偏差與應力分布建立關聯模型,為工藝改進提供預測性分析依據。
全流程數字化實施方案
項目實施遵循PDCA循環管理體系,包含需求診斷、方案定制、設備部署、系統聯調四大階段。以某航天結構件生產企業為例,首先通過CT掃描獲取基準件的點云數據模板,繼而采用模塊化檢測單元布局:前端布置12組高精度激光位移傳感器,中端配置六軸機械臂搭載接觸式測頭,后端部署邊緣計算網關實現數據實時處理。系統與MES平臺對接后,關鍵尺寸CPK值從1.12提升至1.67,測量效率較傳統方式提高15倍(中國計量院實測數據)。
跨行業應用價值驗證
在消費電子領域,某Tier1供應商采用視覺引導機器人檢測方案后,手機中框平面度檢測速度達到3秒/件,誤判率降至0.02%以下。新能源行業應用案例顯示,動力電池極片疊片厚度在線檢測系統可將厚度波動控制在±2μm范圍內,配合機器學習算法能提前30分鐘預警設備偏移趨勢。這些實踐驗證了智能檢測系統在復雜工況下的穩定性和適應性,為行業推廣提供了有力佐證。
全生命周期質量保障體系
系統構建了包含設備校準、過程監控、數據追溯的三維質量網絡。計量標準器每年溯源至國家基準,在線測量模塊實施雙頻激光干涉儀動態校準。數據管理平臺采用區塊鏈技術存儲檢測記錄,確保全流程數據不可篡改。在某精密軸承生產場景中,系統通過建立加工誤差補償數據庫,使產品批次一致性達到99.3%的歷史最優水平,質量追溯響應時間縮短83%。
面向未來,建議行業重點突破亞微米級動態補償算法,發展基于量子傳感的納米尺度測量技術。同時應加強檢測數據與工藝參數的深度耦合,構建覆蓋設計-制造-檢測的全鏈路數字孿生體系。產學研各方需協同推進標準體系建設,特別是在新興領域如鈣鈦礦光伏組件、柔性電子器件等方向建立專項檢測規范,為制造業高質量發展筑牢技術基石。

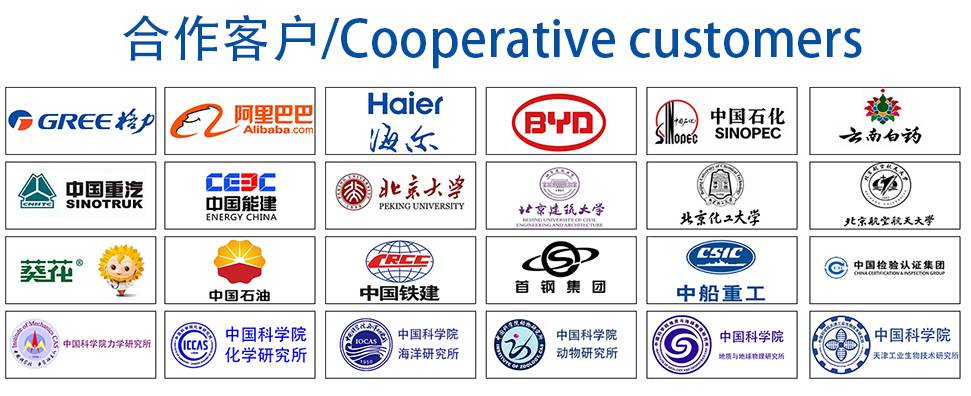