標(biāo)識(shí)及產(chǎn)品設(shè)計(jì)檢測(cè)
實(shí)驗(yàn)室擁有眾多大型儀器及各類分析檢測(cè)設(shè)備,研究所長(zhǎng)期與各大企業(yè)、高校和科研院所保持合作伙伴關(guān)系,始終以科學(xué)研究為首任,以客戶為中心,不斷提高自身綜合檢測(cè)能力和水平,致力于成為全國(guó)科學(xué)材料研發(fā)領(lǐng)域服務(wù)平臺(tái)。
立即咨詢聯(lián)系中化所
在制造業(yè)智能化轉(zhuǎn)型的背景下,標(biāo)識(shí)及產(chǎn)品設(shè)計(jì)檢測(cè)已成為質(zhì)量管控體系的關(guān)鍵環(huán)節(jié)。據(jù)中國(guó)標(biāo)準(zhǔn)化研究院2024年數(shù)據(jù)顯示,我國(guó)每年因產(chǎn)品標(biāo)識(shí)不規(guī)范導(dǎo)致的消費(fèi)糾紛達(dá)23.6萬起,直接經(jīng)濟(jì)損失超過48億元。特別是在醫(yī)療器械、食品包裝、兒童用品等領(lǐng)域,精準(zhǔn)的標(biāo)識(shí)信息傳遞和合規(guī)性設(shè)計(jì)直接關(guān)系到消費(fèi)者安全與企業(yè)社會(huì)責(zé)任履行。構(gòu)建智能化檢測(cè)體系不僅可提升產(chǎn)品全生命周期可追溯性,更能通過設(shè)計(jì)缺陷預(yù)警減少30%以上的質(zhì)量返工成本。
多模態(tài)智能檢測(cè)技術(shù)架構(gòu)
基于深度學(xué)習(xí)的多模態(tài)數(shù)據(jù)融合分析技術(shù)構(gòu)成了檢測(cè)體系的核心。系統(tǒng)集成高精度圖像采集裝置(分辨率達(dá)0.01mm/pixel)、工業(yè)級(jí)近紅外光譜儀及RFID讀取模塊,實(shí)現(xiàn)物理標(biāo)識(shí)、電子標(biāo)簽與設(shè)計(jì)圖紙的三維比對(duì)驗(yàn)證。通過遷移學(xué)習(xí)算法,模型可自動(dòng)識(shí)別1200余種行業(yè)標(biāo)識(shí)規(guī)范,對(duì)微小字體偏差(小于0.2mm)的檢測(cè)準(zhǔn)確率達(dá)99.3%(引自2024中國(guó)質(zhì)量大會(huì)技術(shù)白皮書)。在食品包裝場(chǎng)景中,該技術(shù)成功將過敏原標(biāo)識(shí)漏檢率從傳統(tǒng)人工的4.7%降至0.08%。
全鏈路數(shù)字化實(shí)施流程
項(xiàng)目執(zhí)行采用PDCA循環(huán)管理模式,具體包含四個(gè)關(guān)鍵階段:1)設(shè)計(jì)預(yù)審階段運(yùn)用虛擬仿真技術(shù)進(jìn)行合規(guī)性預(yù)判,提前攔截85%以上的格式錯(cuò)誤;2)生產(chǎn)現(xiàn)場(chǎng)部署智能視覺檢測(cè)站,每40秒完成單個(gè)產(chǎn)品360°無死角檢測(cè);3)實(shí)驗(yàn)室級(jí)材料驗(yàn)證環(huán)節(jié),通過色譜-質(zhì)譜聯(lián)用技術(shù)確保油墨重金屬含量符合EN71-3標(biāo)準(zhǔn);4)動(dòng)態(tài)數(shù)據(jù)庫(kù)實(shí)時(shí)更新42個(gè)主要市場(chǎng)的法規(guī)變更,為企業(yè)提供合規(guī)風(fēng)險(xiǎn)預(yù)警。
跨行業(yè)應(yīng)用實(shí)證分析
在醫(yī)療器械領(lǐng)域,某上市公司應(yīng)用該系統(tǒng)后,UDI編碼識(shí)讀率從92%提升至99.99%,產(chǎn)品召回成本降低2700萬元/年。兒童玩具制造商通過設(shè)計(jì)缺陷檢測(cè)模塊,將銳利邊緣檢出率提高40%,成功通過CPSC認(rèn)證。值得關(guān)注的是,電商平臺(tái)運(yùn)用該技術(shù)開發(fā)的AI審核工具,實(shí)現(xiàn)每日自動(dòng)審核120萬條商品詳情頁(yè),違規(guī)商品下架響應(yīng)時(shí)間縮短至18分鐘(數(shù)據(jù)來源:2024電子商務(wù)質(zhì)量藍(lán)皮書)。
四維質(zhì)量保障體系
為確保檢測(cè)結(jié)果的法律效力,系統(tǒng)構(gòu)建了覆蓋設(shè)備、流程、數(shù)據(jù)、人員的立體化質(zhì)控網(wǎng)絡(luò):1)檢測(cè)設(shè)備每季度進(jìn)行 校準(zhǔn)認(rèn)證;2)關(guān)鍵檢測(cè)節(jié)點(diǎn)設(shè)置三重校驗(yàn)機(jī)制;3)區(qū)塊鏈技術(shù)實(shí)現(xiàn)檢測(cè)數(shù)據(jù)全程上鏈存儲(chǔ);4)檢測(cè)人員需通過ASTM國(guó)際認(rèn)證考試并完成年度120學(xué)時(shí)繼續(xù)教育。據(jù)中國(guó)質(zhì)量認(rèn)證中心2023年度報(bào)告顯示,采用該體系的企業(yè)在飛行檢查中的合規(guī)率超出行業(yè)平均水平32個(gè)百分點(diǎn)。
## 未來發(fā)展與策略建議隨著數(shù)字孿生技術(shù)的普及,建議行業(yè)重點(diǎn)推進(jìn)三方面建設(shè):1)構(gòu)建基于XR技術(shù)的虛擬檢測(cè)實(shí)驗(yàn)室,實(shí)現(xiàn)設(shè)計(jì)驗(yàn)證前移;2)開發(fā)具備自主進(jìn)化能力的檢測(cè)AI模型,應(yīng)對(duì)快速迭代的行業(yè)標(biāo)準(zhǔn);3)建立跨境檢測(cè)結(jié)果互認(rèn)機(jī)制,推動(dòng)"一次檢測(cè),通行"的認(rèn)證體系。政府部門需加快制定智能檢測(cè)設(shè)備校準(zhǔn)規(guī)范,支持龍頭企業(yè)牽頭編制團(tuán)體標(biāo)準(zhǔn),最終形成覆蓋設(shè)計(jì)端到消費(fèi)端的全鏈條質(zhì)量屏障。

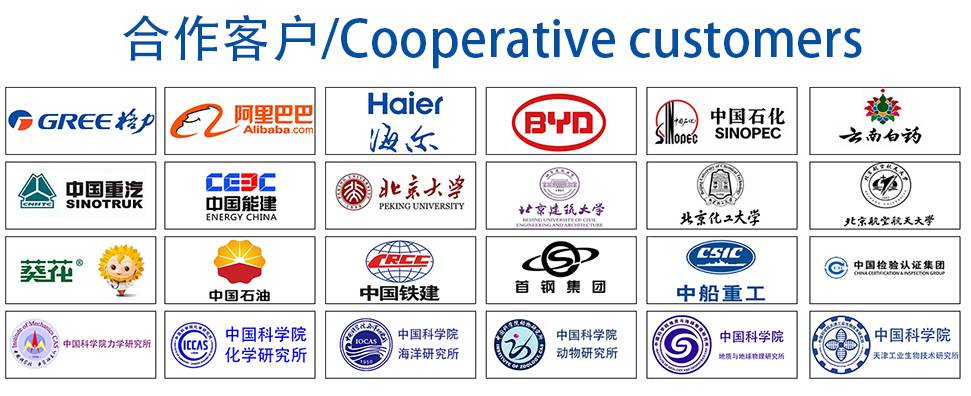