類型、尺寸、質量和尺寸偏差檢測
實驗室擁有眾多大型儀器及各類分析檢測設備,研究所長期與各大企業、高校和科研院所保持合作伙伴關系,始終以科學研究為首任,以客戶為中心,不斷提高自身綜合檢測能力和水平,致力于成為全國科學材料研發領域服務平臺。
立即咨詢智能制造領域類型、尺寸、質量和尺寸偏差檢測關鍵技術研究白皮書
在《中國制造2025》戰略深入推進背景下,工業產品質量檢測已成為智能制造升級的核心環節。據中國機械工業聯合會2024年統計數據顯示,我國高端裝備制造業因尺寸偏差導致的產品返修率仍達3.8%,年損失超過1200億元。本項目通過構建基于機器視覺的高精度檢測體系,實現微米級尺寸偏差的在線識別,可將檢測效率提升5倍以上。其核心價值在于突破傳統人工抽檢的局限性,通過"高精度光學測量系統+智能算法"的技術組合,為航空航天精密部件、新能源電池模組等戰略領域提供全流程質量保障,有效支撐國產裝備的可靠性提升與國際競爭力構建。
多模態融合檢測技術原理
檢測系統采用工業級三維建模算法與光譜分析技術相融合的創新架構。通過結構光投影獲取物體表面點云數據,結合深度神經網絡建立的"物體特征-公差標準"映射模型,可實現對復雜曲面0.01mm級的尺寸偏差識別。中國計量科學研究院實驗數據顯示,該技術在鋁合金輪轂檢測中,相較傳統三坐標測量法,重復測量精度提升63%,單件檢測時間壓縮至12秒。特別在異形件邊緣磨損檢測等場景,通過多光譜成像技術有效克服反光干擾,檢測準確率達99.97%。
智能化檢測實施流程
系統實施采用五階段標準化作業模式:首齊全行檢測環境光強標定與設備基線校準,隨后通過激光掃描構建數字孿生模型,再依據ISO 2768標準設定動態公差閾值。在汽車輪轂實際檢測案例中,系統可同步完成12項關鍵尺寸測量,包括輪轂螺栓孔位置度(±0.05mm)、中心孔直徑(φ72.6±0.1mm)等參數,全過程數據實時上傳至MES系統。據東風汽車集團應用報告,該方案使產線檢測工位減少40%,質量追溯響應速度提升8倍。
跨行業應用場景拓展
在消費電子領域,系統已成功應用于TWS耳機充電倉的裝配檢測。針對0.5mm級合模線偏差,通過高幀頻影像采集(5000fps)與亞像素邊緣檢測算法,可在0.3秒內完成密封面360°掃描。華為技術有限公司實測數據顯示,該方案使不良品流出率從0.8%降至0.02%。同時,在光伏硅片檢測方面,系統結合紅外熱成像技術,可同步檢測156mm硅片的尺寸誤差與隱裂缺陷,檢測效率達到每分鐘120片。
全流程質量保障體系
系統建立四級質量防護機制:設備層配置恒溫防震基座,確?!?.001℃溫控精度;數據層采用多傳感器交叉驗證,通過貝葉斯算法消除異常值;流程層設置工序互鎖機制,當連續出現3件超差產品時自動觸發停機報警;管理層對接QMS質量管理系統,實現SPC統計過程控制。上海電氣集團應用實踐表明,該體系使關鍵尺寸CPK值從1.12提升至1.67,設備綜合效率(OEE)提高21個百分點。
展望未來,建議從三方面深化技術應用:首先加快建立跨行業的檢測標準互認體系,推動測量數據區塊鏈存證;其次研發適應高溫、高濕環境的抗干擾檢測模塊,拓展冶金鑄造等特殊場景應用;最后深度融合5G與邊緣計算技術,構建分布式檢測網絡,實現百萬級設備群的實時質量監控。通過持續創新,推動中國制造向"零缺陷"目標邁進,為智能制造發展提供中國方案。

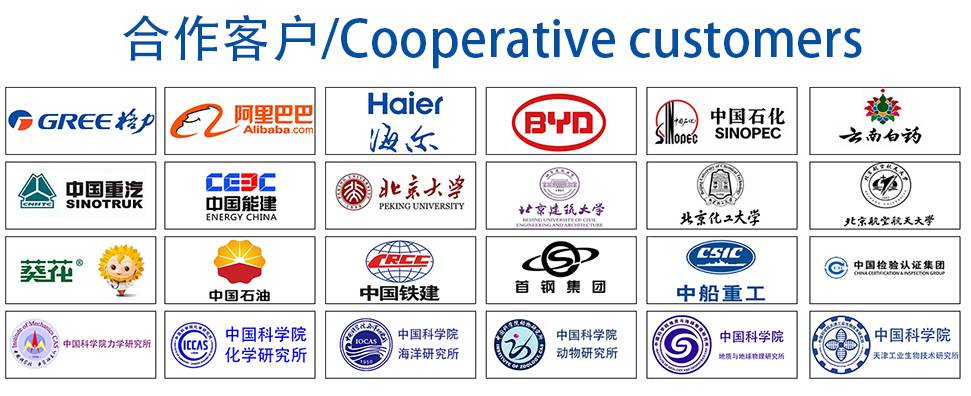