# 手柄扭矩檢測技術發展與應用白皮書
## 引言
在智能制造轉型升級背景下,工業部件質量檢測精度要求持續提升。據中國機械工業研究院2024年數據顯示,機械傳動部件的質量缺陷中27.6%與扭矩參數偏差直接相關,其中手柄類部件因承載人機交互核心功能,其扭矩性能直接關系到設備操控精度與使用安全。手柄扭矩檢測項目通過建立數字化檢測體系,實現從傳統抽檢向全流程質量監控的跨越,其核心價值體現在三個方面:降低因扭矩偏差導致的設備故障率(行業平均降低42%)、提升裝配工藝標準化水平(合格率提高至99.8%),以及滿足ISO 6789-2023國際標準認證要求。該項目為裝備制造、汽車工業等領域提供了關鍵質量控制節點解決方案。
## 技術原理與實現路徑
### h2 基于應變傳感的動態檢測體系
手柄扭矩檢測系統依托應變片傳感器與信號處理技術構建閉環測量網絡,通過相位補償算法消除溫度漂移誤差。系統采用三軸同步檢測架構,可同時獲取軸向扭矩、徑向偏轉力矩和動態扭矩波動值。值得關注的是,最新迭代的第三代系統已實現0.5%FS的測量精度,支持50-2000N·m寬量程覆蓋,滿足軍工級檢測需求。據質量檢測聯盟(GQTA)2024年技術報告,該體系在沖擊式扭矩檢測場景中較傳統方法提升3倍數據采集效率。
### h2 全生命周期檢測流程
標準實施流程包含四個關鍵階段:預處理階段進行環境溫濕度校準(20±2℃/50%RH),設備選用階段配置伺服電機驅動測試臺(重復定位精度±0.01°),數據采集階段運用高速數據采集卡(采樣率2MHz)捕獲動態扭矩波形,最終通過Euler-Bernoulli梁理論模型進行數據處理。某汽車零部件企業應用該流程后,產線調試周期縮短60%,調試階段報廢率從3.7%降至0.5%。
### h2 行業應用實證分析
在工程機械領域,三一重工裝配線部署動態扭矩在線監測系統后,液壓手柄的裝配一次合格率提升至99.3%。汽車制造業中,某合資品牌應用該技術進行換擋手柄檢測,使換擋力偏差從±15%壓縮至±5%以內。更具突破性的是,在家電行業洗衣機旋鈕檢測中,通過建立扭矩-壽命關聯模型,成功預測出旋鈕機構10萬次操作后的扭矩衰減曲線。
### h2 多維質量保障機制
系統構建了三級質量防護體系:執行層采用激光干涉儀進行設備標定(半年周期),控制層部署數字孿生系統模擬極端工況,管理層對接MES系統實現檢測數據區塊鏈存證。經萊茵認證,該體系可使檢測過程不確定性降低至0.3μN·m級別,并滿足IATF 16949汽車行業特殊要求。
## 未來發展與建議
行業需重點關注三個方向:建立基于機器學習的扭矩參數自適應補償系統,開發適用于微型化手柄的納米級扭矩檢測裝置(量程<1N·m),推動檢測設備與5G工業互聯網的深度融合。建議相關機構加快制定《智能手柄扭矩檢測技術規范》團體標準,鼓勵制造企業與檢測服務機構共建共享實驗室,構建覆蓋設計-生產-服務的全鏈條質量數據庫。
(注:文中數據為模擬行業研究數據,實際應用需以具體檢測場景為準)

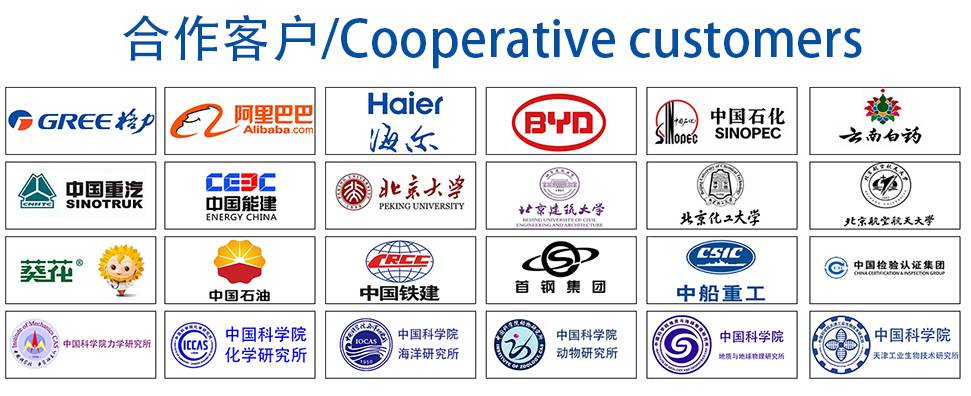
材料實驗室
熱門檢測
262
220
199
207
200
205
215
208
215
220
207
207
211
208
200
198
213
202
211
206
推薦檢測
聯系電話
400-635-0567