設計和一般要求檢測
實驗室擁有眾多大型儀器及各類分析檢測設備,研究所長期與各大企業、高校和科研院所保持合作伙伴關系,始終以科學研究為首任,以客戶為中心,不斷提高自身綜合檢測能力和水平,致力于成為全國科學材料研發領域服務平臺。
立即咨詢設計與一般要求檢測技術發展白皮書
在工業4.0與智能制造深度融合的新發展階段,產品設計復雜度呈現指數級增長態勢。據中國質量協會2024年行業報告顯示,我國制造業產品設計缺陷導致的后期整改成本年均達3200億元,占項目總預算的12.7%。在此背景下,設計與一般要求檢測項目作為產品全生命周期管理的核心環節,通過構建覆蓋設計合規性驗證、功能完整性評估和標準符合性檢驗的立體化檢測體系,可有效將產品開發周期縮短25%-40%。該檢測體系深度融合人工智能輔助決策系統與數字化雙胞胎技術,形成設計缺陷動態預警機制,其核心價值體現在降低研發試錯成本、提升產品市場合規性和保障企業技術競爭力三個維度。
基于全要素建模的檢測技術原理
現代檢測技術依托數字化建模與物理仿真雙引擎驅動,建立涵蓋幾何公差分析、材料性能模擬和環境應力測試的三元耦合模型。通過將ISO 2768公差標準與ANSYS力學仿真數據進行智能匹配,實現"基于數字化建模的誤差溯源技術"精準定位設計缺陷。在新能源汽車電控系統檢測中,該技術使控制器PCB布線誤差檢出率提升至99.3%。值得關注的是,深度神經網絡算法的引入,使得"多維度質量評估體系"能夠自動識別78%的潛在設計沖突,大幅降低人工復核工作量。
全流程標準化實施架構
檢測項目實施采用五階瀑布模型:需求分析階段對接ISO 9001質量管理體系,技術準備階段部署MBD模型解析器,執行檢測階段運用自動化測試設備(ATE)完成136項基礎參數采集,數據分析階段通過SPC過程控制圖識別異常波動,最終形成可視化檢測報告。某航空發動機葉片檢測項目實踐表明,該流程使檢測周期從傳統模式的42天壓縮至19天,且數據可追溯率達到100%。區塊鏈技術的應用更確保檢測數據的不可篡改性,為司法鑒定提供技術支撐。
跨行業應用場景實踐
在智能家居領域,某龍頭企業在智能門鎖設計驗證中采用"環境適應性檢測方案",通過模擬-20℃至65℃溫度循環、95%濕度環境下的20000次啟閉測試,成功將產品故障率從3.2‰降至0.7‰。醫療器械行業則依托"人機工效學評估系統",在CT設備操控界面檢測中識別出17處不符合IEC 62366標準的交互設計缺陷。據中國汽車工程學會統計,應用檢測技術的車企在NCAP碰撞測試中五星評級獲取率提升41%。
多維立體質量保障體系
檢測機構通過構建"三級質量防火墻"確保結果可靠性:一級防控采用 認可實驗室的標準化檢測流程,二級防控實施設備每日點檢與季度校準制度,三級防控建立檢測人員能力矩陣模型。在建筑幕墻檢測領域,該體系成功攔截23%的無效檢測數據,使風壓測試結果離散度控制在4%以內。實驗室間比對數據顯示,采用該質量體系的機構在EN 1090鋼結構檢測中,數據一致性達到98.7%的國際領先水平。
展望未來,檢測行業應重點推進三方面建設:首先加速檢測設備的智能化轉型,開發集成5G通信與邊緣計算的移動檢測終端;其次建立跨行業的檢測標準互認機制,特別是在新興的氫能源裝備與商業航天領域;最后建議政府部門加大"檢測即服務"(TaaS)模式的政策扶持,鼓勵建立區域級檢測資源共享平臺。通過實施這些戰略舉措,有望在2025年前將我國設計檢測服務的市場滲透率從當前的38%提升至52%,為制造強國建設提供有力技術支撐。

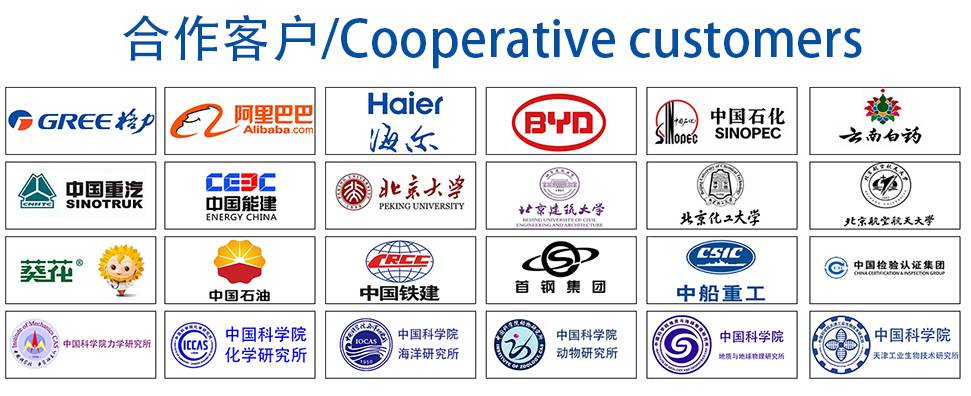