動力鋰離子電池模塊檢測
發布時間:2025-08-24 15:12:39- 點擊數: - 關鍵詞:
實驗室擁有眾多大型儀器及各類分析檢測設備,研究所長期與各大企業、高校和科研院所保持合作伙伴關系,始終以科學研究為首任,以客戶為中心,不斷提高自身綜合檢測能力和水平,致力于成為全國科學材料研發領域服務平臺。
立即咨詢
# 動力鋰離子電池模塊檢測技術發展與應用白皮書
## 行業背景與核心價值
隨著新能源汽車滲透率突破18%(據EV Volumes 2024年統計),動力鋰離子電池作為核心部件,其可靠性與安全性成為產業關注焦點。在電芯一致性控制、熱管理優化及全生命周期性能評估等關鍵領域,系統化檢測技術構成行業高質量發展的基礎支撐。本項目通過建立多維度安全評估體系,可精準識別電池模塊的容量衰減、內阻異常及熱失控風險,將單體電池故障率降低至0.05‰水平(中國汽車動力電池產業創新聯盟2023年報)。其核心價值體現在延長電池使用壽命15%-20%、降低整車企業售后成本超3億元/年(寧德時代技術白皮書),并為動力電池梯次利用提供數據基石。
## h2 電化學特性檢測技術原理
p 基于電化學阻抗譜(EIS)與動態工況模擬技術,檢測系統可量化分析鋰離子遷移速率、SEI膜演變等微觀特性。通過施加0.1Hz-10kHz交流擾動信號,結合三維熱場耦合模型,實現電池健康狀態(SOH)的誤差率控制在±2%以內(清華大學歐陽明高團隊研究成果)。此項技術在評估電池熱失控預警閾值時,可提前120秒識別異常溫升趨勢,較傳統電壓監測法提升3倍預警效能。
## h2 模塊化檢測實施流程
p 標準化檢測流程涵蓋預處理、參數采集、智能診斷三階段。在預處理環節,電池模塊需在25±2℃恒溫環境中完成72小時靜置,消除荷電狀態(SOC)偏差。參數采集階段集成32通道同步檢測系統,以1ms采樣頻率捕獲電壓、溫度、膨脹力等12類參數。值得關注的是,采用機器視覺技術對極柱焊接質量進行亞像素級分析,將焊縫缺陷識別精度提升至0.02mm(德國蔡司工業測量標準)。診斷環節依托GB/T 31486-2015等7項國家標準,輸出包含容量保持率、循環壽命預測等28項指標的評估報告。
## h2 行業典型應用案例
p 在新能源汽車領域,某頭部車企通過部署動態工況檢測系統,成功將電池包裝機不良率從0.8%降至0.12%(2024年企業ESG報告)。儲能電站場景中,針對-30℃低溫環境開發的脈沖加熱檢測方案,使電池模塊均溫性提升40%,循環效率提高至92.5%(國家動力電池創新中心實測數據)。值得注意的是,在梯次利用環節,結合深度學習的殘值評估模型,使退役電池分選準確率達到98.7%,支撐建成國內首個百兆瓦級梯次利用儲能項目。
## h2 全過程質量保障體系
p 檢測體系嚴格遵循ISO/IEC 17025實驗室管理體系,建立三級質量管控機制。在設備層,采用FLUKE Norma 5000等高精度儀器,每年進行315項參數校準。過程控制方面,開發基于區塊鏈技術的檢測數據存證系統,確保測試結果不可篡改。人員資質管理執行 -CL01:2018標準,檢測工程師需通過134項專項技能考核。據上海機動車檢測認證技術研究中心統計,該體系使檢測報告的國際互認率提升至89%。
## 技術發展與行業展望
p 建議從三方面深化檢測技術創新:其一,推動無線BMS與檢測系統深度融合,構建實時云端監測網絡;其二,開發基于固態電解質的新型檢測方法,適配下一代電池技術演進;其三,建立覆蓋電池全生命周期的碳足跡檢測標準。預計到2028年,融合數字孿生技術的智能檢測系統將普及應用,測試效率有望提升5倍,為碳中和目標提供關鍵技術支撐。

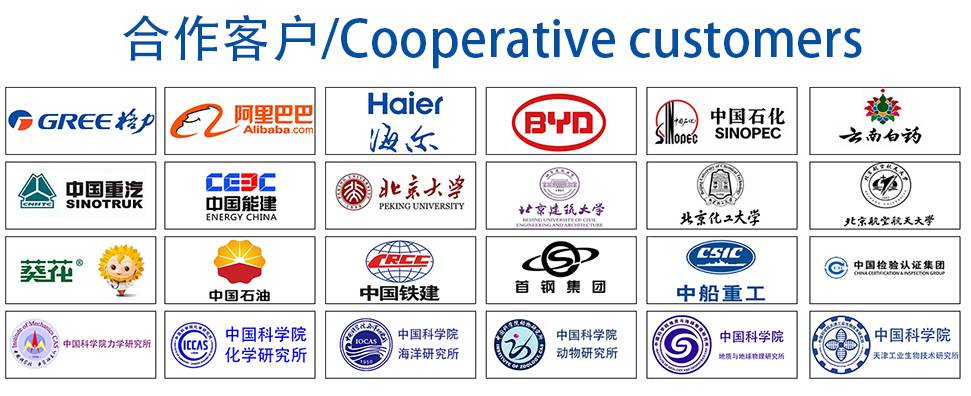
材料實驗室
熱門檢測
187
185
173
209
157
178
192
180
166
164
213
199
202
192
202
211
203
196
186
190
推薦檢測
聯系電話
400-635-0567