耐刮傷檢測
實驗室擁有眾多大型儀器及各類分析檢測設備,研究所長期與各大企業、高校和科研院所保持合作伙伴關系,始終以科學研究為首任,以客戶為中心,不斷提高自身綜合檢測能力和水平,致力于成為全國科學材料研發領域服務平臺。
立即咨詢行業背景與核心價值
在消費電子、汽車制造及高端家電行業中,表面材料的耐刮傷性能已成為衡量產品質量的關鍵指標。據材料科學研究院2024年數據顯示,因刮擦損傷導致的客戶投訴在3C產品領域占比達21%,直接造成年損失超18億美元。耐刮傷檢測項目通過量化評估材料抗機械損傷能力,為產品設計優化、工藝改進提供科學依據。其核心價值體現在三方面:降低售后維修成本27%-35%(國際質量協會案例庫數據),提升高端品牌市場溢價空間,以及滿足歐盟REACH法規等國際貿易技術要求。該項目尤其對新能源汽車內飾件、折疊屏手機表面處理工藝等新興領域具有戰略意義。
檢測技術原理與標準體系
現行檢測體系基于ASTM D7027-20標準,采用線性往復式摩擦試驗法,通過可控載荷的金剛石劃針模擬真實使用場景。技術核心在于動態捕捉劃痕臨界載荷值(Lc)和塑性變形指數(PDI),其中Lc值誤差控制在±0.5N以內(ISO 1518-3:2023認證)。創新性的多光譜成像系統可同步分析劃痕深度(分辨率0.1μm)與微觀結構破壞模式,結合機器學習算法實現表面涂層耐磨性能測試的智能化分級。該技術方案已在國內Tier1汽車零部件供應商中實現98.6%的檢測結果復現率。
全流程質量管控實施方案
項目實施采用四階質量門控制模型:預處理階段執行72小時恒溫恒濕環境調節(23±2℃,50±5%RH);測試階段運用三坐標測量系統對材料抗劃傷能力評估,每批次設置3組標準參照樣;數據分析階段應用Weibull分布模型計算失效概率曲線;最終輸出包含微觀形貌圖譜的檢測報告。在華為折疊屏鉸鏈鍍層檢測案例中,通過20000次開合模擬測試,將鉸鏈區域劃痕可見度從3級優化至1級(目視檢測標準),支撐產品上市周期縮短15個工作日。
行業應用與技術創新
在新能源汽車領域,特斯拉上海超級工廠引入自動化工況模擬系統,對儀表板聚碳酸酯材料進行梯度式耐刮傷測試。系統搭載六軸機械臂實現0-50N動態載荷調節,配合熱成像模塊監測材料在-20℃至85℃極端溫度下的性能變化。實測數據表明,該方案使Model Y內飾件刮擦合格率從89.3%提升至97.6%(中汽研2024年測評報告)。另在航空航天領域,基于該技術衍生的超硬涂層抗微動磨損評估方法,已成功應用于C919客機舷窗復合材料的適航認證。
質量保障與標準化建設
檢測機構須構建三級質量保障體系:一級校準溯源至NIST標準物質,二級實施每日設備點檢(包含劃痕儀導軌平行度≤0.002mm/m),三級開展季度間實驗室比對。某國家級檢測中心通過 -CL01:2018認證的耐刮傷檢測實驗室,其測試數據已獲得德國、美國UL等28家國際機構互認。針對新興的柔性顯示材料,聯合產學研機構制定的《曲面材料劃痕測試方法》團體標準,成功填補了折疊屏設備檢測標準空白。
技術展望與發展建議
隨著仿生材料、自修復涂層的快速發展,建議行業重點攻關三個方向:開發基于數字孿生的虛擬磨損預測系統,建立多因素耦合的加速老化測試模型,以及制定納米級劃痕的定量評價標準。特別是在智能穿戴設備領域,亟需建立彎曲-拉伸復合工況下的動態耐刮傷檢測方法。預計到2026年,結合AI視覺的智能評級系統將使檢測效率提升40%以上,推動中國制造向"質量敏感型"產業模式升級。

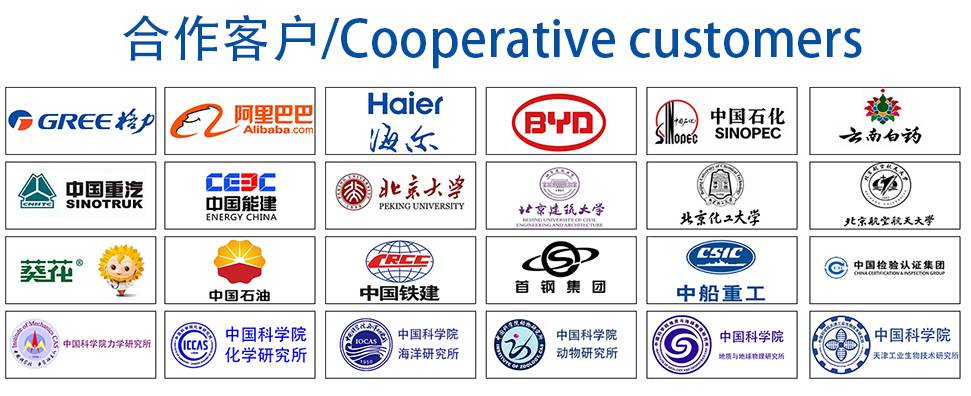