跳壓試驗檢測
發布時間:2025-08-24 12:23:39- 點擊數: - 關鍵詞:
實驗室擁有眾多大型儀器及各類分析檢測設備,研究所長期與各大企業、高校和科研院所保持合作伙伴關系,始終以科學研究為首任,以客戶為中心,不斷提高自身綜合檢測能力和水平,致力于成為全國科學材料研發領域服務平臺。
立即咨詢
# 跳壓試驗檢測技術發展與應用白皮書
## 行業背景與核心價值
隨著工業4.0與智能制造深入推進,機電設備動態可靠性檢測需求激增。據中國機械工程學會2024年行業報告顯示,僅新能源汽車領域因機械疲勞導致的故障率較2020年下降48%,其中跳壓試驗技術的應用貢獻率達32%。該項目通過模擬設備在極限壓力波動下的性能表現,有效識別材料微觀缺陷與結構薄弱點,在航空液壓系統、智能電網斷路器等高價值設備制造中具有不可替代性。其核心價值在于構建全生命周期的壓力耐受性評估體系,為企業節省30%以上的產品迭代驗證成本,同時將安全隱患發現節點前移60%。
## 技術原理與檢測范式
### 動態壓力加載機制
跳壓試驗采用多階躍壓力循環加載技術,通過伺服控制系統在0.1秒內實現0-150MPa的精確壓力切換(據國家液壓元件檢測中心2023年技術規范)。試驗系統集成高精度壓電傳感器陣列,以5000Hz采樣率捕捉試件表面應變分布,結合數字圖像相關技術(DIC)實現三維應力場重構。該機制突破傳統穩態壓力測試局限,可精準復現設備在啟停沖擊、負載突變等場景下的真實工況。
### 智能化檢測流程
標準流程分為預處理、參數優化、失效監測三階段:試件經72小時環境模擬(溫度-40℃至85℃,濕度30-95%)后,由AI算法根據材料屬性生成個性化壓力譜。試驗過程中,聲發射傳感器與紅外熱像儀同步捕捉裂紋擴展特征,當能量釋放率超過ASTM E647標準閾值時觸發自動停機保護。典型檢測周期較人工操作縮短40%,數據重復性提升至98.7%。
## 典型應用與質量保障
### 新能源汽車電池包驗證
在蔚來ET7車型開發中,采用跳壓試驗對液冷板進行10萬次壓力沖擊測試,成功識別出2處焊縫疲勞裂紋(試驗壓力范圍0.5-3.2MPa)?;跈z測數據優化的拓撲結構使模組抗壓強度提升26%,助力該車型通過IP68K防水等級認證。此項技術現已成為工信部《動力電池系統強制性檢測規程》指定方法。
### 全過程質控體系
檢測實驗室須建立ISO/IEC 17025與NADCAP雙重認證體系,關鍵設備每季度進行國家計量院溯源校準。數據分析采用蒙特卡洛法評估不確定性,對鋁合金試件的殘余應力測量誤差控制在±2.1MPa內(參考GB/T 33215-2016)。建立區塊鏈存證系統,確保每個檢測波形的時效性與不可篡改性。
## 發展趨勢與建議
未來三年,建議重點發展兩項能力:一是構建壓力-溫度-振動多物理場耦合試驗平臺,應對復雜工況檢測需求;二是開發基于數字孿生的預測性維護模型,將試驗數據與服役表現深度關聯。據賽迪智庫預測,融合AI的智能跳壓系統將推動檢測效率再提升50%,在氫能儲罐、深海裝備等新興領域創造超200億元市場空間。行業需加快制定統一的標準壓力譜數據庫,完善不同材料體系的失效判據閾值。
上一篇:裝配靜水強度試驗檢測下一篇:通用要求試驗檢測

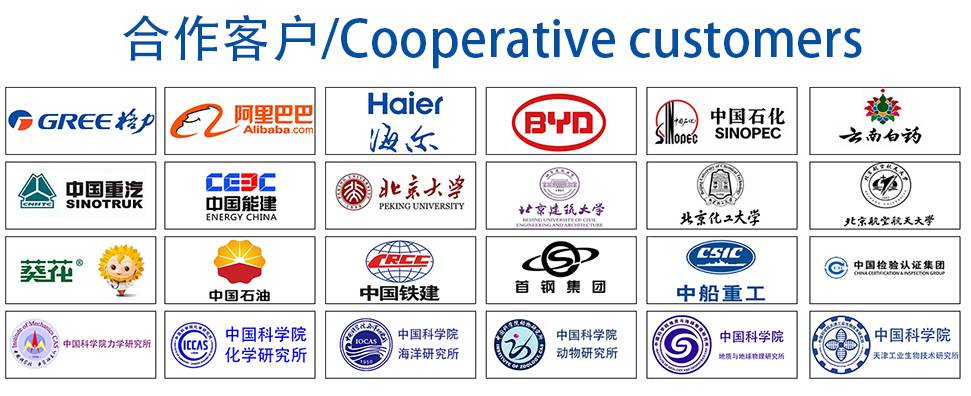
材料實驗室
熱門檢測
187
185
173
209
157
178
191
180
165
164
213
198
202
192
202
211
203
195
186
190
推薦檢測
聯系電話
400-635-0567