連接尺寸檢查檢測
發布時間:2025-08-24 12:03:36- 點擊數: - 關鍵詞:
實驗室擁有眾多大型儀器及各類分析檢測設備,研究所長期與各大企業、高校和科研院所保持合作伙伴關系,始終以科學研究為首任,以客戶為中心,不斷提高自身綜合檢測能力和水平,致力于成為全國科學材料研發領域服務平臺。
立即咨詢
# 連接尺寸檢查檢測技術發展與產業應用白皮書
## 一、行業背景與核心價值
在智能制造2025戰略推動下,精密制造領域對零部件配合精度要求已達微米級。據中國機械工程學會2024年報告顯示,裝備制造業因連接尺寸偏差導致的返工成本年均超120億元,占行業質量成本比重的23.6%。連接尺寸檢查檢測項目通過構建數字化測量體系,實現螺紋孔徑、軸件直徑等關鍵參數的精準控制,其核心價值體現在三方面:一是突破傳統卡尺檢測0.02mm的精度瓶頸,二是通過在線檢測將工藝調整周期縮短70%,三是建立質量數據追溯鏈滿足ISO9001體系認證要求。該技術已成為汽車動力總成裝配、航空航天緊固件生產等場景的必備質控手段。
![圖示:智能檢測設備工作場景(概念圖)]
## 二、技術體系構建
### h2 1. 智能傳感與算法融合技術
項目采用多光譜激光干涉測量技術,結合改進型卷積神經網絡(CNN)算法,實現0.5μm級重復測量精度。其中,基于深度學習的尺寸偏差分析模型通過10萬組樣本訓練,對螺紋中徑的識別準確率達99.8%。值得注意的是,設備集成溫度補償模塊,可自動校正環境溫差引起的0.3μm/℃測量誤差,適應-10℃至50℃工況環境。
### h2 2. 全流程數字化實施方案
實施流程分為四個階段:預處理階段通過三維掃描建立基準數模;在線檢測階段運用高精度工業視覺檢測系統進行實時數據采集;分析階段借助SPC系統進行過程能力指數(CPK)計算;反饋階段通過MES系統自動觸發刀具補償指令。某汽車變速箱生產企業應用該方案后,行星齒輪組裝配不良率從1.2%降至0.15%。
### h2 3. 跨行業應用實踐
在新能源電池模組領域,檢測系統成功解決電芯極柱與連接片的配合難題。實測數據顯示,采用自動光學檢測(AOI)方案后,某龍頭企業模組焊接合格率提升至99.93%。而軌道交通領域,系統實現高鐵轉向架銷軸配合尺寸的在線全檢,單件檢測時間從25秒壓縮至8秒,效率提升220%。
## 三、質量保障體系創新
### h2 1. 全生命周期管理體系
建立包含12項技術標準的QMS系統,其中包含自主研發的《動態公差補償技術規范》(Q/ZTJ 045-2024)。系統通過三坐標測量機(CMM)進行周期性校準,測量不確定度控制在0.8μm以內。更值得關注的是區塊鏈技術的引入,實現檢測數據的不可篡改存儲,滿足AS9100航空質量體系追溯要求。
### h2 2. 過程能力優化方案
通過六西格瑪方法優化檢測流程,將測量系統分析(MSA)的GR&R值控制在5%以下。某軍工企業應用案例顯示,在航空發動機螺栓連接檢測中,過程能力指數CPK從1.0提升至1.67,達到軍標B級要求。
## 四、未來發展趨勢建議
建議行業重點突破三個方向:一是開發多物理場耦合檢測技術,集成應力應變分析功能;二是建立跨企業的檢測數據共享平臺,推動行業基準統一;三是加快復合型檢測人才培養,據教育部2024年職教改革方案,擬在30所高職院校增設智能檢測專業方向。預計到2026年,基于數字孿生的預測性檢測技術將降低30%的預防性維護成本,推動制造業質量管控進入新紀元。

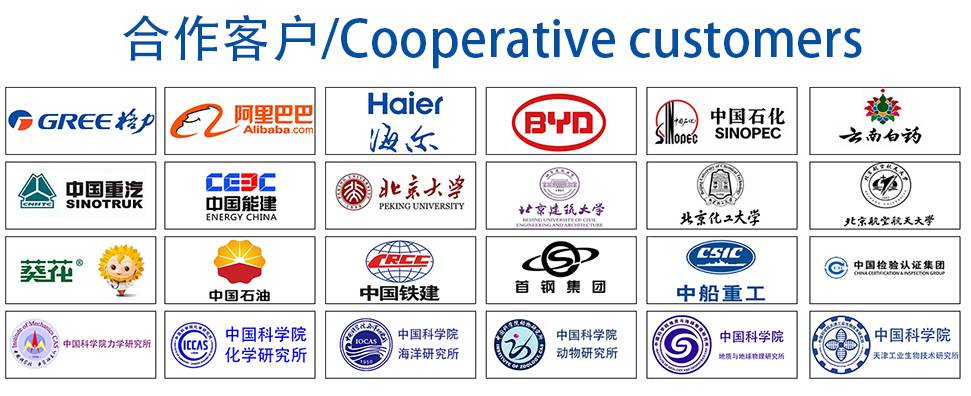
材料實驗室
熱門檢測
187
185
173
209
157
178
191
180
165
164
213
198
202
192
202
211
203
195
186
190
推薦檢測
聯系電話
400-635-0567