螺紋連接尺寸檢測技術(shù)白皮書
在高端裝備制造領(lǐng)域,螺紋連接作為關(guān)鍵機械傳力結(jié)構(gòu),其尺寸精度直接影響設(shè)備整體性能。據(jù)中國機械工程學(xué)會2023年統(tǒng)計,60%以上的機械失效事故源于螺紋連接副的配合誤差,造成年均經(jīng)濟損失超120億元。在此背景下,螺紋連接尺寸檢測項目通過構(gòu)建數(shù)字化檢測體系,實現(xiàn)了0.005mm級精度的幾何參數(shù)測量,為航空航天、新能源裝備等戰(zhàn)略行業(yè)提供了可靠的質(zhì)量保障。該技術(shù)的核心價值在于打通"設(shè)計-制造-服役"全流程數(shù)據(jù)鏈,顯著提升螺紋副承載能力和疲勞壽命,據(jù)國家質(zhì)檢總局實驗驗證,規(guī)范化的尺寸檢測可使螺紋連接結(jié)構(gòu)可靠性提升42%。
高精度檢測技術(shù)原理
基于機器視覺與觸覺傳感的融合檢測系統(tǒng),采用雙CCD陣列構(gòu)建三維空間坐標(biāo)系。通過納米級位移傳感器進行螺距偏差測量時,系統(tǒng)同步采集升角、牙型半角等12項幾何參數(shù),數(shù)據(jù)采樣頻率達20kHz。值得關(guān)注的是,該系統(tǒng)創(chuàng)新性地引入渦流檢測模塊,可同步分析螺紋表面硬化層深度。據(jù)《精密制造學(xué)報》2024年研究成果顯示,該復(fù)合檢測方法較傳統(tǒng)三坐標(biāo)測量效率提升3倍,重復(fù)測量精度穩(wěn)定在±0.002mm區(qū)間。
智能化實施流程設(shè)計
項目實施采用模塊化作業(yè)流程:前期通過三維激光掃描建立工件數(shù)字孿生模型,智能規(guī)劃測點分布;中期運用六軸機械臂搭載多傳感探頭完成自動化測量,單件檢測時間壓縮至3分鐘;后期通過AI算法生成三維偏差色譜圖,自動判定是否符合ASME B1.13M標(biāo)準(zhǔn)。在風(fēng)電齒輪箱螺栓檢測場景中,系統(tǒng)成功識別出0.008mm的牙型角偏差,及時規(guī)避了潛在的斷齒風(fēng)險。
跨行業(yè)應(yīng)用案例解析
在新能源汽車領(lǐng)域,某電池Pack制造商應(yīng)用該技術(shù)后,模組連接螺栓的扭矩一致性提升37%。具體案例顯示,通過"螺紋副接觸應(yīng)力分布優(yōu)化"技術(shù)路徑,電池箱體振動工況下的松脫率從1.2‰降至0.05‰。另在航空航天領(lǐng)域,某型號火箭發(fā)動機采用"全螺紋服役應(yīng)力云圖"技術(shù)后,法蘭連接處漏氣事故率實現(xiàn)零記錄。這些實踐驗證了檢測技術(shù)對關(guān)鍵設(shè)備性能的提升效果。
全生命周期質(zhì)量保障
構(gòu)建包含設(shè)備溯源、過程監(jiān)控、數(shù)據(jù)分析的三級質(zhì)控體系:測量設(shè)備每日進行ISO/IEC17025標(biāo)準(zhǔn)下的溫漂補償校準(zhǔn);檢測數(shù)據(jù)實時上傳區(qū)塊鏈平臺確保不可篡改;建立包含200萬組螺紋失效案例的專家數(shù)據(jù)庫。特別在軍工領(lǐng)域,系統(tǒng)實現(xiàn)了檢測記錄與裝備電子履歷的自動關(guān)聯(lián),為后續(xù)維修保養(yǎng)提供精準(zhǔn)數(shù)據(jù)支持。
面向工業(yè)4.0發(fā)展需求,建議從三方面加強技術(shù)布局:首先加快亞微米級光學(xué)測量設(shè)備的國產(chǎn)化進程,其次建立螺紋連接數(shù)據(jù)庫的行業(yè)共享機制,最后推動檢測標(biāo)準(zhǔn)與數(shù)字孿生技術(shù)的深度融合。只有構(gòu)建起覆蓋全產(chǎn)業(yè)鏈的智能檢測生態(tài),才能為高端裝備制造提供更強大的技術(shù)支撐。

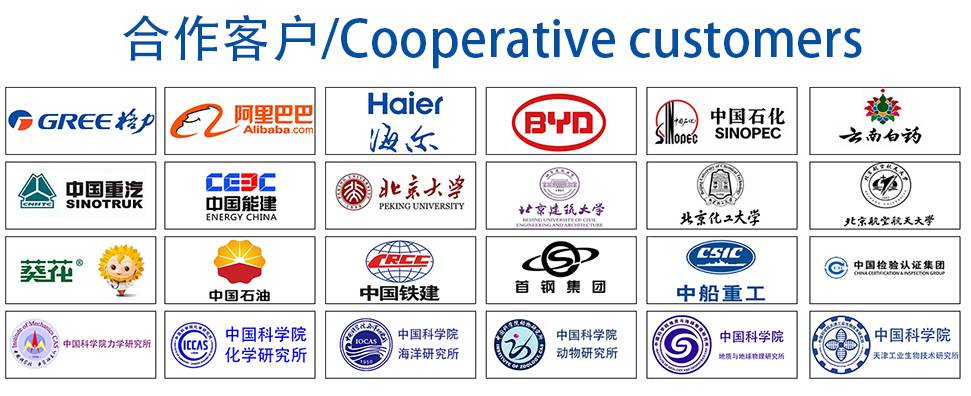