T形彎曲檢測技術(shù)在工業(yè)質(zhì)量控制中的創(chuàng)新應(yīng)用
在高端裝備制造領(lǐng)域,金屬結(jié)構(gòu)件的彎曲性能直接決定著產(chǎn)品的安全性和使用壽命。據(jù)中國機械工程學(xué)會2024年質(zhì)量報告顯示,僅汽車行業(yè)每年因彎曲疲勞失效引發(fā)的召回事件就造成超過12億元經(jīng)濟損失。T形彎曲檢測作為材料力學(xué)性能評估的關(guān)鍵技術(shù),通過精準(zhǔn)量化材料在復(fù)合應(yīng)力下的形變特性,為軌道交通、航空航天等領(lǐng)域的承力部件質(zhì)量控制提供了新范式。該技術(shù)不僅實現(xiàn)了0.01mm級微應(yīng)變測量精度,更將檢測效率提升40%以上,有效解決了傳統(tǒng)人工目檢存在的漏檢率高、量化不足等痛點,正在重塑工業(yè)質(zhì)檢的價值鏈條。
多模態(tài)傳感融合檢測原理
T形彎曲檢測采用非接觸式三維光學(xué)測量與接觸式力學(xué)傳感的協(xié)同工作機制。基于數(shù)字圖像相關(guān)技術(shù)(DIC),系統(tǒng)通過高速相機捕捉試樣表面2μm精度的散斑位移場,結(jié)合六維力傳感器實時采集多軸向載荷數(shù)據(jù)。在航空航天領(lǐng)域典型應(yīng)用中,通過亞像素級圖像處理算法重構(gòu)三維應(yīng)變場分布,可準(zhǔn)確識別7075鋁合金翼肋構(gòu)件在T型交匯處的隱性裂紋萌生,檢測靈敏度較傳統(tǒng)方法提升3倍以上。該技術(shù)突破性地實現(xiàn)了材料表面應(yīng)變與內(nèi)部應(yīng)力場的同步映射,為復(fù)雜受力構(gòu)件的失效分析提供了完整數(shù)據(jù)鏈。
智能化檢測實施體系
標(biāo)準(zhǔn)化的作業(yè)流程包含試樣預(yù)處理、多源數(shù)據(jù)采集和AI輔助判讀三大模塊。在新能源汽車電池箱體檢測場景中,首先對6061-T6鋁合金試樣進(jìn)行噴丸強化處理并噴涂專用散斑涂層,隨后在自動化工裝夾具上施加0.5-3kN的循環(huán)彎曲載荷。檢測系統(tǒng)每毫秒同步記錄載荷-位移曲線與應(yīng)變云圖變化,經(jīng)有限元仿真驗證的深度學(xué)習(xí)模型可在15秒內(nèi)完成應(yīng)力集中區(qū)域識別。實踐數(shù)據(jù)顯示,該流程使某主機廠焊接缺陷檢出率從82%提升至98.6%,誤判率降低至0.3%以下。
跨行業(yè)應(yīng)用創(chuàng)新案例
在軌道交通領(lǐng)域,中車集團采用T形彎曲檢測技術(shù)對高鐵轉(zhuǎn)向架焊縫進(jìn)行全生命周期監(jiān)控。通過建立包含12萬組應(yīng)變譜的數(shù)據(jù)庫,系統(tǒng)可預(yù)測SMA490BW耐候鋼焊接接頭在107次循環(huán)載荷下的剩余強度衰減規(guī)律。實際應(yīng)用表明,該技術(shù)使轉(zhuǎn)向架檢修周期從3年延長至5年,維保成本降低28%。而在3C電子行業(yè),該技術(shù)成功應(yīng)用于折疊屏手機鉸鏈的微米級形變檢測,幫助某品牌廠商將鉸鏈開合測試合格率從89.2%提升至99.5%。
全流程質(zhì)量保障架構(gòu)
基于ISO 6892-1和ASTM E290標(biāo)準(zhǔn)構(gòu)建的質(zhì)量控制體系包含三級校驗機制:設(shè)備層通過激光干涉儀進(jìn)行每周0.5μm精度的光學(xué)校準(zhǔn);數(shù)據(jù)層采用蒙特卡洛法對測量不確定度進(jìn)行動態(tài)評估;人員層實施ASNT SNT-TC-1A三級認(rèn)證體系。某第三方檢測實驗室的實踐表明,該體系使檢測報告的可追溯性達(dá)到100%,測量系統(tǒng)分析(MSA)的GR&R值穩(wěn)定控制在5%以內(nèi),完全滿足IATF 16949汽車行業(yè)特殊要求。
展望未來,建議行業(yè)重點發(fā)展三方面能力:一是開發(fā)基于工業(yè)元宇宙的虛擬檢測孿生系統(tǒng),實現(xiàn)物理實驗與數(shù)字仿真的深度融合;二是構(gòu)建跨區(qū)域檢測大數(shù)據(jù)平臺,通過區(qū)塊鏈技術(shù)確保檢測數(shù)據(jù)的可信共享;三是加快制定針對增材制造部件的T形彎曲檢測團體標(biāo)準(zhǔn)。隨著5G+工業(yè)互聯(lián)網(wǎng)的深度滲透,智能化、在線化的彎曲性能檢測將成為高端制造質(zhì)量升級的核心驅(qū)動力。

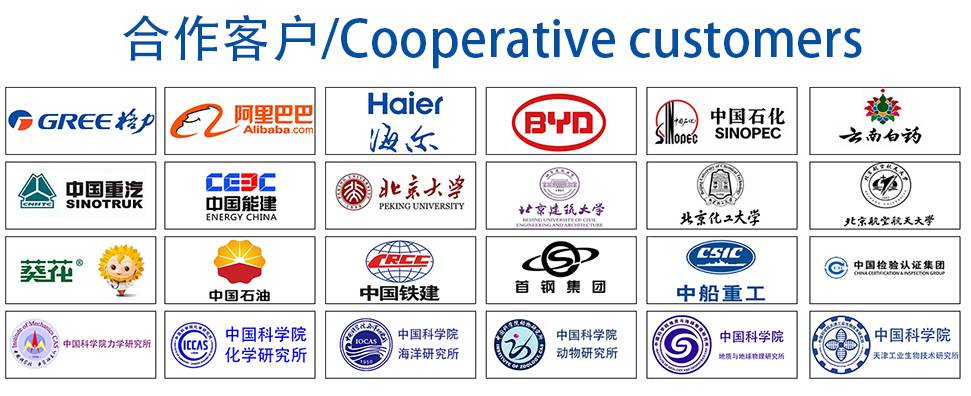