電子連接器和插座檢測
實驗室擁有眾多大型儀器及各類分析檢測設備,研究所長期與各大企業、高校和科研院所保持合作伙伴關系,始終以科學研究為首任,以客戶為中心,不斷提高自身綜合檢測能力和水平,致力于成為全國科學材料研發領域服務平臺。
立即咨詢電子連接器和插座檢測的技術創新與行業實踐
隨著智能化設備普及率持續攀升,電子連接器與插座作為關鍵電氣接口組件,其可靠性直接關系到新能源汽車、5G通信基站、工業自動化等領域的設備穩定性。據中國電子元件行業協會2024年數據顯示,連接器市場規模已突破900億美元,而因接觸不良引發的設備故障占比高達17.3%。在此背景下,專業檢測體系的價值愈發凸顯,通過精準評估接觸電阻、插拔壽命、環境耐受性等核心指標,可有效避免信號傳輸衰減、電弧放電等安全隱患。項目核心價值在于構建多維度質量驗證平臺,推動連接器行業實現從"經驗制造"到"數據驅動"的轉型升級,為國產高端連接器打入國際供應鏈提供技術背書。
多模態檢測技術體系構建
檢測系統基于IEC 60512、EIA-364等國際標準,整合接觸電阻動態監測(CRD)、機械壽命加速測試(MLAT)、三維形變分析(3D-DIC)等核心技術。通過微歐計實現0.1μΩ級接觸阻抗測量,配合高速攝像系統捕捉插拔過程中的微觀形變,可同步評估機械磨損與電氣性能劣化的關聯性。值得關注的是,采用溫度-濕度-振動三綜合試驗箱模擬極限工況,能夠在72小時內等效5年自然老化過程,較傳統檢測效率提升8倍。
全流程質量控制方案
檢測實施分為預處理、基準測試、環境模擬、失效分析四個階段。預處理階段需完成樣品清潔度檢驗與接觸表面形貌掃描(SEM檢測),確?;€數據準確性。在新能源汽車高壓連接器檢測中,需執行3000次插拔循環測試,每次插拔后測量接觸電阻波動值,據國家智能電網研究院測試報告顯示,合格產品ΔR應控制在初始值15%以內。針對戶外5G基站插座,則需通過IP68防水等級認證與-40℃~125℃溫度沖擊測試。
行業標桿應用實踐
在某頭部車企800V高壓平臺開發中,檢測機構通過接觸電阻溫升曲線分析,發現鍍銀層厚度不足導致的局部過熱現象。經工藝優化后,連接器在200A負載下的溫升從58℃降至32℃,達到VDA 305-100標準要求。另一典型案例是5G微基站防水插座檢測,采用氦質譜檢漏法精準定位密封圈0.02mm級尺寸偏差,使防水合格率從82%提升至99.6%,年故障率降低至0.3次/千臺。
數字化質量保障體系
檢測實驗室需建立ISO/IEC 17025認證體系,關鍵設備每日進行標準樣件校準,測量系統分析(MSA)的GR&R值嚴格控制在10%以內。更值得關注的是區塊鏈技術的應用,某檢測機構開發的e-Cert系統,可將測試數據實時上鏈存儲,確保檢測報告不可篡改。據統計,采用智能檢測系統的企業,質量問題追溯效率提升40%,客訴處理周期縮短65%。
展望未來,建議從三方面深化檢測能力建設:首先推動車規級連接器檢測標準與AEC-Q200體系接軌,突破車載高頻信號完整性測試技術瓶頸;其次研發基于數字孿生的智能預測系統,實現失效模式提前預警;最后構建行業級檢測數據庫,打通設計-制造-檢測數據鏈,為連接器微型化、高頻化發展提供決策支持。唯有持續創新檢測手段,方能護航中國智造走向高可靠性時代。

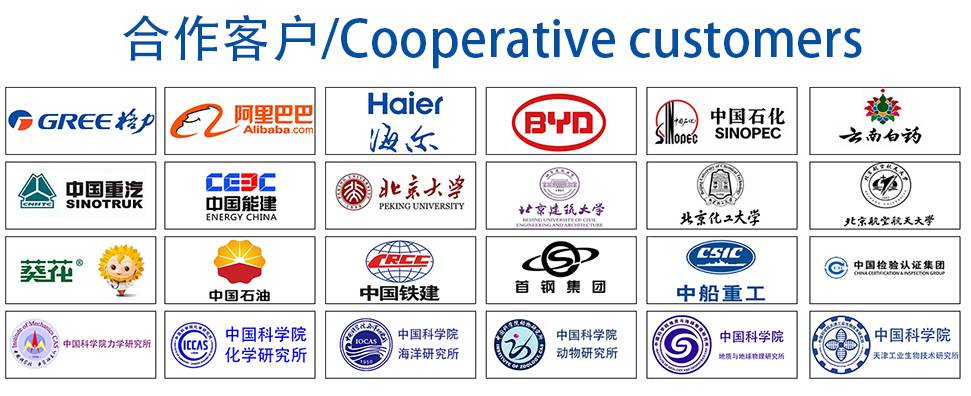