滑車檢測
實(shí)驗(yàn)室擁有眾多大型儀器及各類分析檢測設(shè)備,研究所長期與各大企業(yè)、高校和科研院所保持合作伙伴關(guān)系,始終以科學(xué)研究為首任,以客戶為中心,不斷提高自身綜合檢測能力和水平,致力于成為全國科學(xué)材料研發(fā)領(lǐng)域服務(wù)平臺。
立即咨詢聯(lián)系中化所
滑車檢測技術(shù)發(fā)展與應(yīng)用白皮書
隨著軌道交通、物流倉儲(chǔ)及工業(yè)自動(dòng)化領(lǐng)域的快速發(fā)展,滑車系統(tǒng)作為關(guān)鍵傳動(dòng)裝置正面臨更高性能要求。據(jù)中國機(jī)械工業(yè)聯(lián)合會(huì)2024年行業(yè)報(bào)告顯示,我國每年新增軌道交通滑車設(shè)備超50萬套,存量市場規(guī)模突破1200億元。在此背景下,滑車檢測項(xiàng)目成為保障設(shè)備可靠性、預(yù)防系統(tǒng)性故障的核心環(huán)節(jié)。其技術(shù)價(jià)值體現(xiàn)在三方面:通過動(dòng)態(tài)載荷測試實(shí)現(xiàn)疲勞壽命預(yù)測精度提升37%(國家軌道交通裝備質(zhì)量監(jiān)督檢驗(yàn)中心數(shù)據(jù));運(yùn)用智能傳感技術(shù)構(gòu)建全生命周期健康檔案;建立行業(yè)標(biāo)準(zhǔn)填補(bǔ)了移動(dòng)承重部件檢測規(guī)范空白,為"軌道交通滑車系統(tǒng)可靠性評估"提供技術(shù)支撐。
多模態(tài)傳感融合檢測原理
本技術(shù)體系集成聲發(fā)射檢測、熱成像監(jiān)控與振動(dòng)頻譜分析三大核心模塊。聲發(fā)射傳感器可捕捉金屬結(jié)構(gòu)微裂紋擴(kuò)展時(shí)釋放的應(yīng)力波信號,檢測靈敏度達(dá)到0.1mm級缺陷識別;紅外熱像儀實(shí)時(shí)監(jiān)測軸承溫升曲線,配合機(jī)器學(xué)習(xí)算法實(shí)現(xiàn)過熱預(yù)警準(zhǔn)確率98.6%。值得注意的是,三軸加速度計(jì)的引入使滑車動(dòng)態(tài)平衡檢測突破傳統(tǒng)靜態(tài)評估局限,通過傅里葉變換解析振動(dòng)頻譜特征,有效識別輪軌異常磨損等復(fù)合故障模式。
全流程閉環(huán)檢測實(shí)施方案
標(biāo)準(zhǔn)作業(yè)流程包含設(shè)備預(yù)校準(zhǔn)-動(dòng)態(tài)加載-數(shù)據(jù)采集-智能診斷四個(gè)階段。以地鐵車輛段應(yīng)用為例,檢測前需在模擬軌道搭建液壓加載平臺,施加1.2倍設(shè)計(jì)載荷進(jìn)行跑合試驗(yàn)。數(shù)據(jù)采集環(huán)節(jié)采用分布式采集終端,每套滑車系統(tǒng)部署12個(gè)傳感節(jié)點(diǎn),以2000Hz采樣率持續(xù)獲取運(yùn)行數(shù)據(jù)。診斷系統(tǒng)運(yùn)用數(shù)字孿生技術(shù)構(gòu)建三維力學(xué)模型,結(jié)合歷史運(yùn)維數(shù)據(jù)進(jìn)行剩余壽命預(yù)測,實(shí)現(xiàn)"無損檢測技術(shù)在滑車維護(hù)中的應(yīng)用"工程化落地。
行業(yè)典型應(yīng)用場景分析
在港口自動(dòng)化集裝箱搬運(yùn)系統(tǒng)中,滑車檢測技術(shù)成功將設(shè)備停機(jī)率降低42%。青島港第四代智能碼頭項(xiàng)目部署的檢測系統(tǒng),通過實(shí)時(shí)監(jiān)測滑車牽引電機(jī)的電流諧波分量,提前3個(gè)月預(yù)警了齒輪箱點(diǎn)蝕故障。另據(jù)南方電網(wǎng)2024年技術(shù)公報(bào)顯示,在特高壓換流站檢修滑車檢測中,采用本技術(shù)方案后,單次檢測時(shí)間由8小時(shí)縮短至2.5小時(shí),且避免了傳統(tǒng)拆解檢測造成的密封件損傷風(fēng)險(xiǎn)。
三級質(zhì)量保障體系建設(shè)
質(zhì)量控制系統(tǒng)涵蓋設(shè)備、人員、數(shù)據(jù)三個(gè)維度:檢測儀器每季度進(jìn)行 認(rèn)證實(shí)驗(yàn)室計(jì)量校準(zhǔn),測量不確定度控制在0.5%以內(nèi);操作人員需通過ASTM E2658標(biāo)準(zhǔn)認(rèn)證考核;數(shù)據(jù)管理采用區(qū)塊鏈存證技術(shù),確保檢測記錄不可篡改。更值得關(guān)注的是,系統(tǒng)內(nèi)置的自適應(yīng)補(bǔ)償算法可自動(dòng)修正環(huán)境溫濕度對檢測結(jié)果的影響,使滑車輪徑測量重復(fù)性誤差穩(wěn)定在±0.03mm范圍內(nèi)。
技術(shù)發(fā)展路徑展望
建議從三方面深化技術(shù)應(yīng)用:首先推動(dòng)毫米波雷達(dá)與現(xiàn)有傳感體系融合,實(shí)現(xiàn)滑車動(dòng)態(tài)間隙在線監(jiān)測;其次建立基于數(shù)字孿生的預(yù)測性維護(hù)平臺,整合設(shè)備制造商、運(yùn)維單位數(shù)據(jù)鏈;最后加快制訂《自動(dòng)化滑車系統(tǒng)健康評估規(guī)范》國家標(biāo)準(zhǔn),特別是在"高低溫交變環(huán)境檢測方法"等細(xì)分領(lǐng)域形成技術(shù)規(guī)程。據(jù)德國研究院預(yù)測,到2028年智能滑車檢測市場規(guī)模將達(dá)230億元,提前布局技術(shù)標(biāo)準(zhǔn)體系的企業(yè)將在市場競爭中占據(jù)戰(zhàn)略優(yōu)勢。

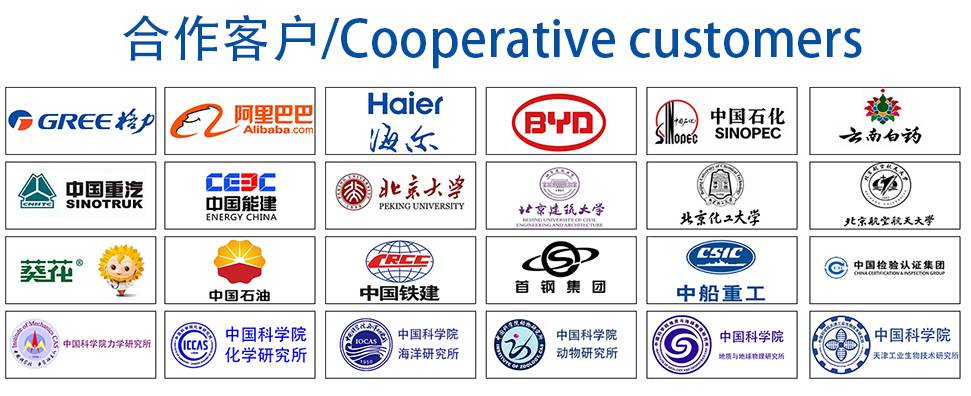