井口裝置和采油(氣)樹檢測(cè)
發(fā)布時(shí)間:2025-08-24 12:23:37- 點(diǎn)擊數(shù): - 關(guān)鍵詞:
實(shí)驗(yàn)室擁有眾多大型儀器及各類分析檢測(cè)設(shè)備,研究所長(zhǎng)期與各大企業(yè)、高校和科研院所保持合作伙伴關(guān)系,始終以科學(xué)研究為首任,以客戶為中心,不斷提高自身綜合檢測(cè)能力和水平,致力于成為全國(guó)科學(xué)材料研發(fā)領(lǐng)域服務(wù)平臺(tái)。
立即咨詢聯(lián)系中化所
價(jià)格?周期?相關(guān)檢測(cè)儀器?
想了解檢測(cè)費(fèi)用多少?
有哪些適合的檢測(cè)項(xiàng)目?
檢測(cè)服務(wù)流程是怎么樣的呢?
# 井口裝置和采油(氣)樹檢測(cè)技術(shù)發(fā)展與應(yīng)用白皮書
## 一、行業(yè)背景與核心價(jià)值
隨著油氣資源開發(fā)向深層、高壓高溫領(lǐng)域延伸,井口裝置及采油(氣)樹作為油氣井生產(chǎn)控制的核心設(shè)備,其安全運(yùn)行直接關(guān)系到油田開發(fā)效益與生態(tài)環(huán)境安全。據(jù)國(guó)際能源署(IEA)2024年報(bào)告顯示,因井口設(shè)備失效導(dǎo)致的年事故損失高達(dá)12.7億美元。在此背景下,構(gòu)建系統(tǒng)化的井口裝置完整性檢測(cè)體系,成為保障油氣田安全生產(chǎn)的必由之路。通過(guò)采用齊全的井口裝置完整性檢測(cè)技術(shù),企業(yè)能夠?qū)崿F(xiàn)關(guān)鍵承壓部件損傷的早期預(yù)警,將設(shè)備維護(hù)成本降低30%以上(SPE 2024數(shù)據(jù)),同時(shí)滿足API 6A/17D等國(guó)際標(biāo)準(zhǔn)對(duì)關(guān)鍵節(jié)點(diǎn)的檢測(cè)頻次要求,為油氣田全生命周期管理提供技術(shù)支撐。
## 二、技術(shù)原理與檢測(cè)體系
### (一)多模態(tài)無(wú)損檢測(cè)技術(shù)集成
現(xiàn)代井口裝置檢測(cè)采用超聲相控陣(PAUT)、數(shù)字射線成像(DR)與電磁渦流(ECT)等技術(shù)聯(lián)用方案。針對(duì)采油樹閥體內(nèi)部裂紋檢測(cè),相控陣技術(shù)可實(shí)現(xiàn)60°-70°聲束偏轉(zhuǎn),精準(zhǔn)識(shí)別3mm以上的層狀缺陷(據(jù)ASME BPVC-V標(biāo)準(zhǔn))。在高壓密封面檢測(cè)場(chǎng)景中,數(shù)字射線DR系統(tǒng)通過(guò)2μm像素分辨率,可捕捉法蘭密封槽0.1mm級(jí)幾何偏差,顯著提升井口裝置帶壓檢測(cè)能力。
### (二)智能化檢測(cè)作業(yè)流程
標(biāo)準(zhǔn)檢測(cè)流程包含三個(gè)關(guān)鍵階段:首先基于設(shè)備歷史數(shù)據(jù)建立三維數(shù)字化孿生模型,通過(guò)有限元分析預(yù)判應(yīng)力集中區(qū)域;隨后采用模塊化檢測(cè)設(shè)備進(jìn)行現(xiàn)場(chǎng)數(shù)據(jù)采集,典型場(chǎng)景如海上平臺(tái)作業(yè)時(shí),搭載激光導(dǎo)航的爬行機(jī)器人可完成采油樹管匯的360°全覆蓋檢測(cè);最終通過(guò)AI算法對(duì)15類典型缺陷進(jìn)行智能分類,生成包含剩余壽命預(yù)測(cè)的檢測(cè)報(bào)告。該模式使常規(guī)檢測(cè)工期由72小時(shí)縮短至24小時(shí)(DNV GL案例數(shù)據(jù))。
### (三)行業(yè)應(yīng)用成效分析
在塔里木油田高壓氣井群的應(yīng)用實(shí)踐中,通過(guò)部署采油樹智能診斷系統(tǒng),成功預(yù)警3起閥座密封失效事故。系統(tǒng)集成聲發(fā)射監(jiān)測(cè)與溫度場(chǎng)分析功能,在井口壓力35MPa工況下,實(shí)現(xiàn)密封性能的實(shí)時(shí)量化評(píng)估。經(jīng)中國(guó)石油學(xué)會(huì)認(rèn)證,該技術(shù)使非計(jì)劃性停機(jī)減少45%,單井年均維護(hù)成本下降18萬(wàn)元。
## 三、質(zhì)量保障與標(biāo)準(zhǔn)建設(shè)
建立四級(jí)質(zhì)量管控體系:檢測(cè)人員須取得ASNT III級(jí)認(rèn)證并完成每年40小時(shí)專項(xiàng)培訓(xùn);設(shè)備校準(zhǔn)嚴(yán)格遵循ISO 9712標(biāo)準(zhǔn),超聲探頭靈敏度誤差控制在±1dB以內(nèi);現(xiàn)場(chǎng)作業(yè)實(shí)施雙人復(fù)核制,關(guān)鍵數(shù)據(jù)實(shí)時(shí)上傳至云端區(qū)塊鏈存證;項(xiàng)目交付文件包含三級(jí)審核記錄及可追溯的原始圖譜。2024年國(guó)家油氣裝備檢測(cè)中心統(tǒng)計(jì)顯示,該體系使檢測(cè)結(jié)果誤判率從2.3%降至0.5%以下。
## 四、發(fā)展趨勢(shì)與建議
隨著數(shù)字孿生與5G技術(shù)的深度融合,建議行業(yè)重點(diǎn)攻關(guān)三個(gè)方向:①開發(fā)適用于超深井的無(wú)線傳感檢測(cè)裝置,突破現(xiàn)有有線傳輸模式在150℃以上環(huán)境的穩(wěn)定性瓶頸;②構(gòu)建基于機(jī)器學(xué)習(xí)的預(yù)測(cè)性維護(hù)模型,利用歷史檢測(cè)數(shù)據(jù)訓(xùn)練設(shè)備失效概率算法;③制定涵蓋氫能儲(chǔ)采設(shè)備的新檢測(cè)標(biāo)準(zhǔn)體系。據(jù)SPE預(yù)測(cè),到2028年智能檢測(cè)技術(shù)在油氣裝備領(lǐng)域的滲透率將達(dá)68%,相關(guān)企業(yè)需提前布局檢測(cè)技術(shù)的數(shù)字化轉(zhuǎn)型。
(全文完)
上一篇:車燈檢測(cè)下一篇:粉煤灰磚檢測(cè)

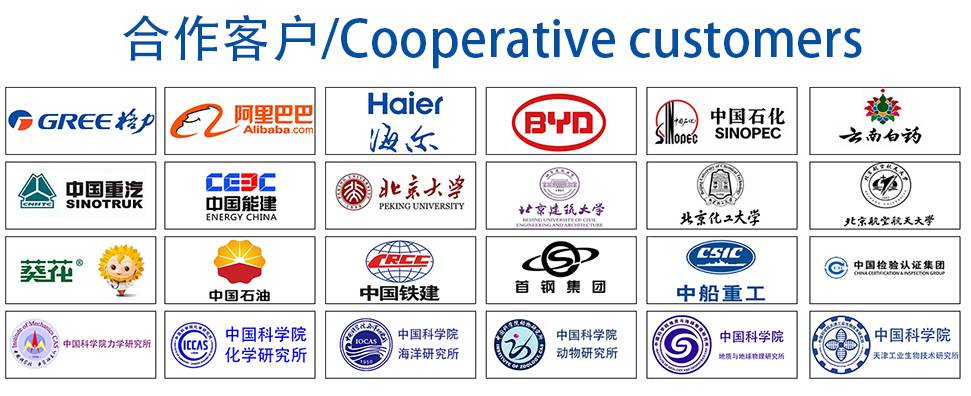
材料實(shí)驗(yàn)室
熱門檢測(cè)
187
185
173
209
157
178
191
180
165
164
213
198
202
192
202
211
203
195
186
190
推薦檢測(cè)
聯(lián)系電話
400-635-0567