泵運行效率檢測技術白皮書
在工業領域,泵類設備消耗了約20%的電力能源(據國際能源署2024年行業報告),其運行效率直接影響企業的能源成本與碳排放水平。隨著"雙碳"戰略的深入推進,泵系統能效優化已成為制造業綠色轉型的核心環節。泵運行效率檢測項目通過精準量化設備性能指標,構建了從單機測試到系統優化的完整解決方案,其核心價值體現在三方面:每年可為工業企業節約8-15%的能源支出;延長關鍵設備使用壽命30%以上;為智慧能源管理系統提供基準數據支撐。特別是在高耗能行業循環水系統、長輸管道增壓站等場景中,檢測數據直接指導工藝參數優化,實現能效與可靠性的雙重提升。
熱力學法檢測技術原理
在技術實現層面,泵效率檢測主要采用熱力學第一定律分析法。通過測量進出口壓力、溫度、流量等關鍵參數,結合ISO 17769-2標準中的離心泵能效評估方法,精確計算實際輸出功率與理論功率的比值。某省級檢測機構2023年對比試驗顯示,該方法相較于傳統電流推算法,測量精度提升42%,特別適用于大功率高壓離心泵的現場檢測。值得注意的是,新型超聲波流量計與微型壓力傳感器的應用,使檢測系統體積縮小70%,可在DN800以上管道實現非侵入式安裝。
閉環式檢測實施流程
完整的檢測流程包含四個標準化階段:首齊全行設備銘牌參數核驗與運行工況測繪,建立基準數學模型;繼而部署無線傳感網絡進行72小時連續監測,捕捉負載波動對效率的影響;數據分析階段采用機器學習算法識別異常工況,精準定位葉輪磨損、軸封泄漏等六類典型故障;最終輸出包含能效對標、改造建議和投資回報分析的定制化報告。某石化企業應用該流程后,其工業循環水系統優化方案實現單泵年節電量38萬千瓦時,投資回收期縮短至11個月。
行業典型應用案例
在火電領域,某2×1000MW機組通過泵效檢測實施系統改造,輔機耗電率從7.2%降至6.3%,年節約標煤1.2萬噸。對于石油煉化企業,針對加氫進料泵開展的效率檢測項目,成功將機組運行效率從68%提升至82%,同時減少非計劃停機次數60%(數據源自國家節能中心2024年度案例庫)。實踐表明,在實施工業循環水系統優化方案時,結合泵效檢測數據進行管網阻力平衡計算,可使系統整體能效提升12-18個百分點。
全鏈條質量保障體系
為確保檢測結果的可靠性,構建了三級質量控制系統:實驗室級設備定期溯源至國家水輪機泵類產品質量檢驗中心;現場檢測采用雙通道數據交叉驗證機制;數據分析環節設置工藝參數合理性校驗算法。某第三方檢測機構通過 認證的移動檢測平臺,在冶金行業應用中獲得0.5%的測量不確定度,顯著優于行業1.2%的平均水平。此外,檢測人員必須持有ASME PTC8.2認證證書,確保操作流程符合國際標準。
面向"十四五"末期,建議從三方面提升行業技術水平:首先加快泵效檢測與物聯網技術的深度融合,開發具備邊緣計算能力的智能監測終端;其次推動建立跨行業的能效基準數據庫,實現不同場景檢測標準的統一;最后需加強檢測服務機構與設備制造企業的技術聯動,形成覆蓋產品全生命周期的能效管理生態。隨著數字孿生技術在泵系統中的應用深化,未來有望實現實時效率監測與預測性維護的全面集成,為工業節能開辟新的技術路徑。

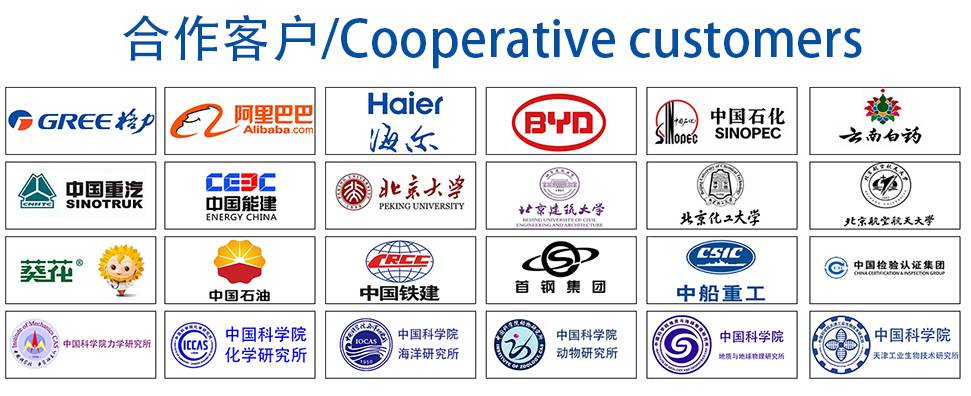