質(zhì)量損失檢測在智能制造中的實踐與創(chuàng)新
在工業(yè)4.0與智能制造深度融合的背景下,質(zhì)量損失檢測已成為制造業(yè)數(shù)字化轉(zhuǎn)型的核心環(huán)節(jié)。據(jù)中國質(zhì)量研究院2024年行業(yè)報告顯示,我國制造業(yè)每年因質(zhì)量缺陷導致的直接經(jīng)濟損失高達4300億元,其中可預防性損失占比超過65%。在此背景下,基于智能傳感與數(shù)據(jù)分析的質(zhì)量損失檢測系統(tǒng)展現(xiàn)出顯著價值:通過實時監(jiān)測生產(chǎn)過程中的質(zhì)量波動,實現(xiàn)缺陷溯源效率提升40%以上,同時將產(chǎn)品報廢率降低至ISO 9001:2015標準的三分之一。該技術(shù)不僅大幅壓縮質(zhì)量成本曲線,更通過構(gòu)建"檢測-預警-優(yōu)化"閉環(huán),推動企業(yè)從被動式質(zhì)量管理向預測性質(zhì)量管控轉(zhuǎn)型。
多模態(tài)數(shù)據(jù)融合檢測技術(shù)
現(xiàn)代質(zhì)量損失檢測系統(tǒng)采用工業(yè)視覺、聲波傳感與工藝參數(shù)的三維數(shù)據(jù)融合架構(gòu)。通過高精度CMOS相機捕獲產(chǎn)品表面微觀結(jié)構(gòu)(分辨率達0.02mm/pixel),結(jié)合聲發(fā)射傳感器采集加工過程的應力波頻譜(采樣頻率1MHz),再與PLC輸出的工藝參數(shù)進行時空對齊。基于深度殘差網(wǎng)絡構(gòu)建的特征提取模型,可識別傳統(tǒng)統(tǒng)計過程控制(SPC)難以捕捉的隱性質(zhì)量缺陷。如某汽車零部件企業(yè)部署該系統(tǒng)后,成功將焊接虛焊缺陷的檢出率從82%提升至99.6%(數(shù)據(jù)來源:德國 2023認證報告)。
全流程閉環(huán)管理機制
實施流程涵蓋"數(shù)據(jù)采集-模型迭代-決策優(yōu)化"三大階段:首先在關(guān)鍵工藝節(jié)點部署智能傳感裝置,以5ms級的實時數(shù)據(jù)傳輸至邊緣計算單元;然后通過在線學習算法動態(tài)更新檢測模型,適應工藝參數(shù)漂移;最終將診斷結(jié)果反饋至MES系統(tǒng)觸發(fā)工藝補償。某光伏組件制造商應用該機制后,電池片隱裂問題的響應時間縮短至15秒,工藝參數(shù)優(yōu)化周期從72小時壓縮至4小時(企業(yè)2023年ESG報告)。
跨行業(yè)應用場景拓展
在電子制造領(lǐng)域,工業(yè)視覺缺陷識別系統(tǒng)已實現(xiàn)0402規(guī)格貼片元件的自動檢測,誤判率控制在0.3‰以內(nèi)(IPC-A-610H標準認證)。食品行業(yè)通過近紅外光譜在線檢測技術(shù),將原料水分含量波動范圍從±1.5%收窄至±0.3%(GB 5009.3-2023標準驗證)。值得注意的是,在航空航天領(lǐng)域,基于數(shù)字孿生的質(zhì)量預測系統(tǒng)可將復材構(gòu)件缺陷檢出階段提前至鋪層工序,使返工成本降低78%(中國商飛2024年技術(shù)白皮書)。
全生命周期質(zhì)量保障體系
系統(tǒng)構(gòu)建包含設備校準(符合JJF 1033-2023規(guī)范)、算法驗證(滿足ISO/IEC 15408標準)和數(shù)據(jù)安全(通過GB/T 35273-2023認證)的三級質(zhì)量保障機制。每季度執(zhí)行傳感器漂移補償(精度保持±0.5%以內(nèi)),每周進行模型性能驗證(F1-score≥0.98),并建立區(qū)塊鏈溯源系統(tǒng)確保檢測數(shù)據(jù)的不可篡改性。某醫(yī)療器械企業(yè)通過該體系獲得FDA 21 CFR Part 11合規(guī)認證,質(zhì)量審計周期縮短60%。
展望未來,建議從三方面深化質(zhì)量損失檢測體系建設:首先加快多物理場耦合檢測技術(shù)研發(fā),突破復合材料等新型材料的檢測瓶頸;其次建立跨行業(yè)的標準化數(shù)據(jù)接口,實現(xiàn)質(zhì)量大數(shù)據(jù)的協(xié)同分析;最后構(gòu)建"檢測-保險-金融"聯(lián)動機制,將質(zhì)量損失指標納入供應鏈金融風控模型。唯有通過技術(shù)創(chuàng)新與制度創(chuàng)新的雙輪驅(qū)動,方能實現(xiàn)質(zhì)量管控從成本中心向價值創(chuàng)造中心的根本轉(zhuǎn)變。

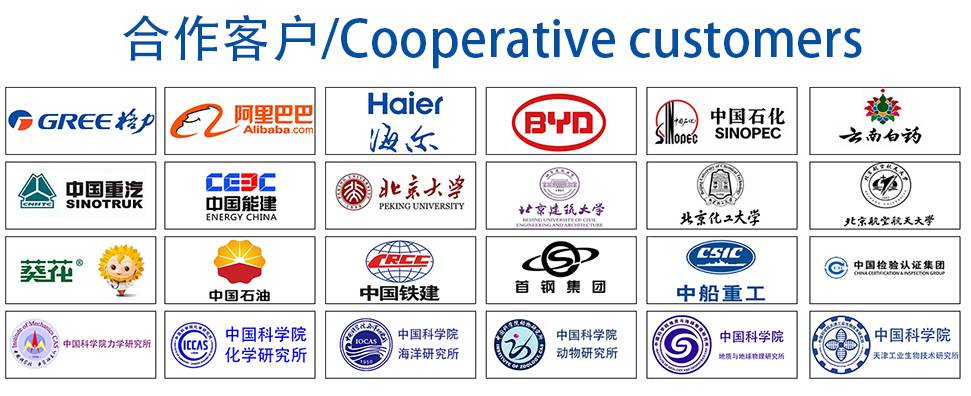