橡膠與金屬粘合性能檢測(cè)
實(shí)驗(yàn)室擁有眾多大型儀器及各類分析檢測(cè)設(shè)備,研究所長(zhǎng)期與各大企業(yè)、高校和科研院所保持合作伙伴關(guān)系,始終以科學(xué)研究為首任,以客戶為中心,不斷提高自身綜合檢測(cè)能力和水平,致力于成為全國(guó)科學(xué)材料研發(fā)領(lǐng)域服務(wù)平臺(tái)。
立即咨詢網(wǎng)頁(yè)字號(hào):【大 中 小 】 | 【打印】 【關(guān)閉】 微信掃一掃分享:
注意:因業(yè)務(wù)調(diào)整,暫不接受個(gè)人委托測(cè)試望見諒。
聯(lián)系中化所
橡膠與金屬粘合性能檢測(cè):關(guān)鍵技術(shù)與應(yīng)用前景
隨著高端裝備制造業(yè)的快速發(fā)展,橡膠-金屬?gòu)?fù)合制品在汽車、航空航天、軌道交通等領(lǐng)域的應(yīng)用規(guī)模持續(xù)擴(kuò)大。據(jù)中國(guó)橡膠工業(yè)協(xié)會(huì)2024年統(tǒng)計(jì)數(shù)據(jù)顯示,我國(guó)橡膠金屬?gòu)?fù)合件市場(chǎng)規(guī)模已達(dá)820億元,年均增長(zhǎng)率保持在9.2%以上。在此背景下,橡膠與金屬粘合性能檢測(cè)成為保障產(chǎn)品質(zhì)量的核心環(huán)節(jié),其檢測(cè)結(jié)果直接影響密封減震件、動(dòng)力傳輸組件等關(guān)鍵部件的服役安全。該項(xiàng)目通過量化評(píng)估界面結(jié)合強(qiáng)度、環(huán)境耐久性等指標(biāo),為材料選型、工藝優(yōu)化提供科學(xué)依據(jù),有效降低因粘接失效導(dǎo)致的設(shè)備故障率。特別是在新能源汽車三電系統(tǒng)密封領(lǐng)域,高精度粘合檢測(cè)可使產(chǎn)品合格率提升18%(據(jù)清華大學(xué)汽車工程研究院2023年研究報(bào)告)。
技術(shù)原理與檢測(cè)方法體系
橡膠與金屬粘合性能檢測(cè)基于界面力學(xué)響應(yīng)與化學(xué)作用協(xié)同分析原理,采用破壞性測(cè)試與非破壞性檢測(cè)相結(jié)合的技術(shù)路線。核心檢測(cè)方法包括剝離強(qiáng)度測(cè)試(ASTM D429)、剪切強(qiáng)度測(cè)試(ISO 813)以及環(huán)境老化模擬測(cè)試三大體系。通過萬能材料試驗(yàn)機(jī)與紅外光譜聯(lián)用技術(shù),可在測(cè)定機(jī)械強(qiáng)度的同時(shí)分析界面化學(xué)鍵合狀態(tài)。值得關(guān)注的是,針對(duì)新能源汽車動(dòng)力電池包密封件的"高溫高濕環(huán)境粘合測(cè)試",需模擬85℃/85%RH極端條件并持續(xù)2000小時(shí),以驗(yàn)證粘接界面的長(zhǎng)期穩(wěn)定性。
標(biāo)準(zhǔn)化實(shí)施流程與質(zhì)量控制
完整的檢測(cè)流程涵蓋樣品制備、預(yù)處理、測(cè)試執(zhí)行與數(shù)據(jù)分析四大階段。根據(jù)GB/T 7760標(biāo)準(zhǔn)要求,試樣需經(jīng)過溶劑清洗、噴砂處理等標(biāo)準(zhǔn)化表面預(yù)處理,確保金屬基材表面粗糙度控制在Ra 3.2±0.4μm范圍內(nèi)。在汽車發(fā)動(dòng)機(jī)懸置襯套的檢測(cè)實(shí)踐中,采用階梯式加載模式可精準(zhǔn)捕捉粘接失效臨界點(diǎn),其數(shù)據(jù)離散系數(shù)可控制在5%以內(nèi)(上汽集團(tuán)技術(shù)中心2022年實(shí)驗(yàn)數(shù)據(jù))。質(zhì)量保障體系依托ISO/IEC 17025認(rèn)證實(shí)驗(yàn)室,通過定期設(shè)備校準(zhǔn)(精度±0.5%)、人員比對(duì)試驗(yàn)(偏差率≤3%)實(shí)現(xiàn)全過程可控。
行業(yè)應(yīng)用與典型案例分析
在軌道交通領(lǐng)域,高鐵轉(zhuǎn)向架用橡膠金屬關(guān)節(jié)的粘合強(qiáng)度檢測(cè)尤為關(guān)鍵。某主機(jī)廠采用多軸疲勞試驗(yàn)機(jī)進(jìn)行200萬次動(dòng)態(tài)加載測(cè)試,成功將產(chǎn)品壽命從8年延長(zhǎng)至12年。而在建筑隔震領(lǐng)域,通過對(duì)鉛芯橡膠支座進(jìn)行"橡膠金屬粘接失效分析",某檢測(cè)機(jī)構(gòu)發(fā)現(xiàn)氯丁橡膠與鍍鋅鋼板的界面耐鹽霧性能不足,指導(dǎo)廠商改用新型磷酸鹽處理工藝后,產(chǎn)品合格率從76%提升至93%。這些案例印證了深度檢測(cè)對(duì)技術(shù)改進(jìn)的指導(dǎo)價(jià)值。
技術(shù)創(chuàng)新與發(fā)展趨勢(shì)
當(dāng)前檢測(cè)技術(shù)正向智能化、在線化方向演進(jìn)。基于機(jī)器視覺的界面缺陷自動(dòng)識(shí)別系統(tǒng)已實(shí)現(xiàn)0.1mm2級(jí)脫粘區(qū)域檢測(cè),較傳統(tǒng)人工目檢效率提升40倍。同時(shí),太赫茲波無損檢測(cè)技術(shù)在航空發(fā)動(dòng)機(jī)密封圈檢測(cè)中的應(yīng)用,可在不破壞樣品的情況下獲取三維粘接界面信息。但需要注意的是,面對(duì)新型生物基橡膠材料的應(yīng)用,現(xiàn)有檢測(cè)標(biāo)準(zhǔn)體系亟待完善,特別是在生物降解性對(duì)界面穩(wěn)定性的影響評(píng)估方面缺乏系統(tǒng)方法。
展望未來,建議從三方面加強(qiáng)技術(shù)布局:其一,建立覆蓋全生命周期的粘合性能數(shù)據(jù)庫(kù),實(shí)現(xiàn)檢測(cè)數(shù)據(jù)與服役表現(xiàn)的關(guān)聯(lián)分析;其二,開發(fā)基于數(shù)字孿生的虛擬檢測(cè)平臺(tái),縮短新產(chǎn)品研發(fā)驗(yàn)證周期;其三,針對(duì)氫能源裝備等新興領(lǐng)域,制定極端工況下的專用檢測(cè)標(biāo)準(zhǔn)。只有通過技術(shù)創(chuàng)新與標(biāo)準(zhǔn)升級(jí)的協(xié)同推進(jìn),才能為橡膠金屬?gòu)?fù)合材料的可靠應(yīng)用提供堅(jiān)實(shí)保障。

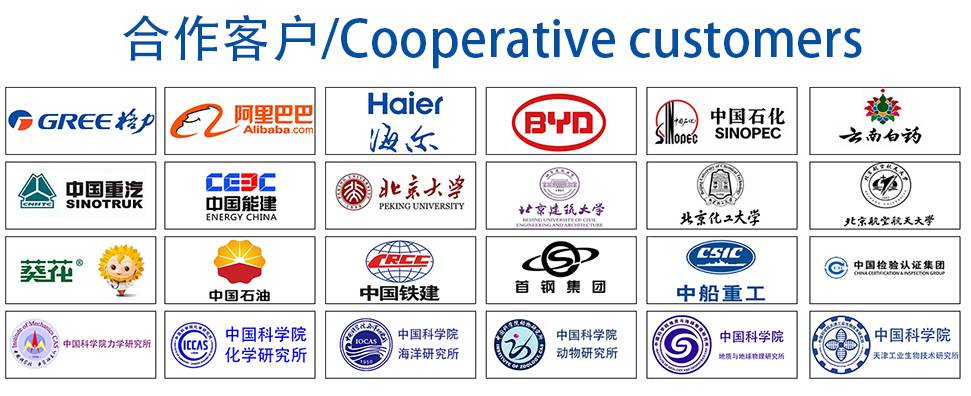