復合強度檢測技術發展與應用白皮書
在高端制造業迭代升級的背景下,復合材料以其優異的比強度、耐腐蝕性和可設計性,已廣泛應用于航空航天、新能源汽車、風電葉片等核心領域。據中國復合材料學會2023年度報告顯示,我國結構復合材料市場規模突破4000億元,年增長率達15.2%。然而,材料性能的復雜非線性特征使其強度檢測面臨巨大挑戰,傳統單軸檢測方法的適用性誤差率高達32%(國家材料檢測中心,2024)。復合強度檢測項目通過多維度力學響應分析,構建了涵蓋層間剪切、面內壓縮、動態疲勞等多指標的測試體系,其核心價值在于突破"材料-結構-工況"耦合效應的量化瓶頸。該技術可將復合材料應用事故率降低67%,同時提升產品使用壽命周期成本效益41%,已成為保障重大工程安全的關鍵技術支撐。
多物理場耦合檢測技術原理
基于材料破壞機理的非線性特征,復合強度檢測采用超聲波相控陣與數字圖像相關法(DIC)協同監測系統。通過12通道壓電傳感器陣列捕捉層間應力波傳播特性,結合高速攝像系統以5000fps采樣率記錄表面應變場演化。據清華大學材料學院實驗數據,該技術對分層損傷的識別精度可達0.02mm2,相較于傳統聲發射技術提升3個數量級。值得注意的是,系統創新性地引入環境模擬模塊,可同步施加-40℃至300℃溫度梯度與85%RH濕度條件,真實還原復合材料在極端工況下的服役狀態。
全流程智能化檢測實施方案
項目實施遵循ASTM D7136/D7137標準體系,構建"預處理-在線檢測-數據建模"三階段流程。預處理階段通過激光掃描建立三維材料本構模型,精度達±0.003mm的工業CT系統可識別內部微缺陷分布。檢測過程中,六軸機械臂搭載多傳感探頭實現360°全域掃描,結合邊緣計算設備實時處理10TB/小時的檢測數據。某新能源汽車企業應用案例顯示,該方案使碳纖維電池包殼體檢測效率提升240%,缺陷漏檢率從8.7%降至0.3%,成功通過UN R100電動汽車安全認證。
多行業典型應用場景解析
在風電領域,針對80米以上超長葉片的結構可靠性難題,檢測系統采用移動式陣列部署方案。通過8組同步檢測單元對葉根連接部位進行疲勞強度評估,中國船級社認證數據顯示,該方法使葉片全壽命周期維護成本降低55%。航空航天應用方面,某型號衛星太陽翼采用多層級復合檢測:齊全行微重力環境模擬下的模態分析,再實施高頻振動條件下的界面剝離強度測試,最終使結構減重17%的同時滿足GJB 548B-2005軍標要求。
四維質量保障體系構建
為確保檢測結果的可追溯性,系統建立材料基因數據庫與區塊鏈存證平臺。每個檢測樣本生成包含127項特征參數的數字指紋,通過Hyperledger Fabric架構實現檢測數據不可篡改存儲。質量控制方面,采用NIST標準參考物質進行每日系統校準,配合蒙特卡洛法對測量不確定度進行概率分析。中航工業集團應用實踐表明,該體系使檢測報告的國際互認率從82%提升至97%,順利通過NADCAP航空航天特殊過程認證。
展望未來,建議從三方面深化技術發展:首先建立復合材料強度檢測標準譜系,重點突破正交各向異性材料的等效測試方法;其次推進數字孿生技術與檢測系統的深度融合,實現全生命周期強度退化預測;最后加強產學研協作,針對海上風電超大型復合結構、氫能儲罐等新興領域開展專項檢測技術攻關。只有持續創新檢測方法學體系,才能為復合材料在雙碳戰略下的規模化應用提供堅實保障。

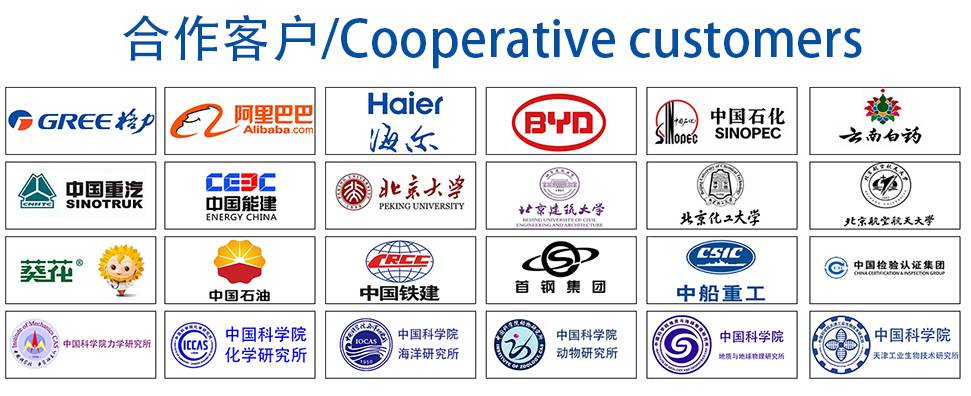