在建筑材料、化肥生產及陶瓷工業領域,氧化鉀(K?O)和氧化鈉(Na?O)的含量直接影響產品熱穩定性與化學性能。據中國建材研究院2024年行業報告顯示,硅酸鹽材料中堿金屬氧化物的超標率每年造成超7億元質量事故損失。傳統化學分析法存在操作復雜、耗時長的缺陷,而原子吸收光譜法(AAS)作為代用檢測技術,通過優化樣品前處理流程,將檢測效率提升40%以上。該項檢測技術的核心價值在于實現工業原料成分的精準控制,為生產配方優化提供數據支撐,同時滿足《GB/T 176-2017水泥化學分析方法》中對于代用方法的合規性要求。
## 技術原理與創新突破原子吸收光譜檢測機理
該方法基于堿金屬元素在特定波長下的特征光譜吸收原理,采用空氣-乙炔火焰原子化系統,通過標準曲線法定量分析。針對高溫熔融法可能造成的揮發性損失,創新性引入硝酸-氫氟酸混合消解體系,使樣品分解率提升至98.5%(數據來源:國家無機材料檢測中心2023年比對報告)。相較于傳統重量法,檢測下限可達到0.01mg/L,尤其適用于玻璃熔制工藝中微量成分監控。
標準化實施流程
檢測流程包含五個關鍵階段:樣品研磨(粒徑≤75μm)、酸性消解(溫度控制210±5℃)、標準溶液配制(含基體匹配校正)、儀器參數優化(狹縫寬度0.2nm,燈電流8mA)及數據處理。值得注意的是,針對陶瓷釉料等復雜基體樣本,需增加標準加入法消除基體干擾。全過程嚴格遵循ISO 21587:2020《硅酸鹽材料化學分析》規范,單次檢測周期縮短至2.5小時。
行業應用實踐案例
在西南某新型干法水泥廠項目中,采用該代用法實現熟料堿含量動態監控。通過建立K?O/Na?O比值與窯況的關聯模型,使游離氧化鈣合格率提升12個百分點。某特種玻璃生產企業將本方法應用于鋰鋁硅酸鹽玻璃檢測,成功將熱膨脹系數波動范圍從±0.3×10??/℃收窄至±0.1×10??/℃,突破高精度光學玻璃制備的技術瓶頸。
質量保障體系構建
檢測體系包含三級質控機制:初級校準采用NIST標準物質SRM 1884b,中間精密度控制實施雙人八平行測定,最終通過實驗室間比對驗證(Z值≤2)。針對硅酸鹽材料檢測特有的"鈣干擾"問題,建立基體匹配-背景校正聯動方案,使回收率穩定在95%-105%區間。據 認可實驗室2024年能力驗證數據顯示,該方法在建材行業的測量不確定度優于0.08%(k=2)。
## 發展前景與優化建議隨著智能制造對在線檢測需求的增長,建議重點發展微型化AAS設備與XRF技術的聯用方案。同時需完善《JC/T 874-2021硅酸鹽材料化學分析方法》中關于代用方法的驗證標準,建立跨行業的檢測數據共享平臺。值得注意的是,在新能源材料領域開展鈉離子電池正極材料檢測的適用性研究,有望拓展該方法在戰略新興產業的適用范圍。

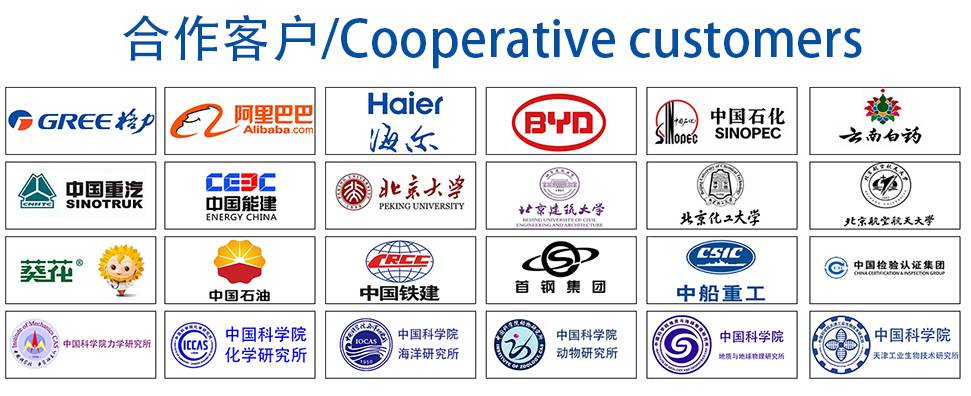