加工質量檢測
實驗室擁有眾多大型儀器及各類分析檢測設備,研究所長期與各大企業、高校和科研院所保持合作伙伴關系,始終以科學研究為首任,以客戶為中心,不斷提高自身綜合檢測能力和水平,致力于成為全國科學材料研發領域服務平臺。
立即咨詢加工質量檢測技術體系構建與行業實踐白皮書
在工業4.0與智能制造深度融合的背景下,加工質量檢測作為制造產業鏈的核心環節,正在經歷從傳統人工抽檢向智能化全檢的技術跨越。據中國機械工業聯合會2024年行業報告顯示,我國高端裝備制造領域因加工缺陷導致的年度經濟損失達327億元,質量問題已成為制約產業升級的關鍵瓶頸。通過構建智能化檢測體系,企業可實現0.01mm級精度控制,將產品不良率降低至百萬分級別。該技術體系不僅承載著提升產品可靠性的核心使命,更通過高精度三維坐標測量技術和智能質量追溯系統,推動制造過程數字化改造,為航空航天、精密儀器等戰略性產業提供全生命周期質量保障。
多模態檢測技術融合應用
現代加工質量檢測系統集成機器視覺、激光掃描與多軸運動控制三大核心技術模塊。基于深度學習算法的視覺檢測單元可識別5μm級表面缺陷,較傳統方法提升12倍檢測效率。某汽車零部件企業2024年實施的智能檢測產線顯示,通過激光干涉儀與六軸機械臂的協同作業,渦輪葉片輪廓度檢測精度達到±0.005mm,完全滿足AS9100D航空質量標準要求。值得注意的是,模塊化設計使系統能快速適配不同工件特征,切換檢測方案耗時從傳統8小時縮減至15分鐘。
閉環式質量管理系統架構
完整的檢測流程包含預處理建模、在線檢測、數據分析和工藝優化四個階段。在半導體封裝檢測場景中,系統首先通過工業CT獲取封裝結構三維點云數據,運用GPU加速算法在1.2秒內完成10萬+特征點比對。某晶圓代工廠實踐數據顯示,通過實時反饋檢測數據至MES系統,晶圓切割崩邊率從0.25%降至0.07%,年度良品提升效益超1.8億元。與此相呼應的是,檢測系統生成的SPC控制圖可自動觸發工藝參數調整,形成"檢測-分析-優化"的智能制造閉環。
行業應用場景驗證
在航空航天領域,某型號航空發動機葉片檢測項目采用多光譜熱成像技術,成功檢測出傳統方法難以發現的微米級內部缺陷。實踐表明,該技術使檢測漏檢率從3.2%降至0.05%,單臺發動機裝配周期縮短22個工作日。此外,軌道交通行業引入的輪對智能檢測系統,通過線激光陣列實現列車輪緣厚度動態測量,測量速度達3m/s,較人工檢測效率提升40倍,每年可避免因輪對磨損導致的潛在事故損失約7600萬元。
全流程質量保障體系
檢測系統構建了涵蓋設備、方法和人員的立體化質控網絡。所有檢測設備定期通過NIST可溯源標準器進行校準,確保測量不確定度控制在標稱值30%以內。在人員資質方面,檢測工程師必須通過ISO/IEC17025認證考核,并每季度參加AI算法優化培訓。某精密軸承制造企業的實踐案例顯示,實施該體系后檢測數據復現性從92.3%提升至99.6%,客戶投訴率同比下降67%。
展望未來,建議行業重點突破三個方向:一是開發融合量子傳感的納米級檢測裝置,攻克超精密加工檢測難題;二是建立跨行業質量數據共享平臺,利用區塊鏈技術構建可信質量溯源體系;三是加強復合型檢測人才培養,預計到2027年需新增12萬名具備AI工程化能力的質量工程師。通過技術創新與體系建設的雙輪驅動,加工質量檢測將進入智能感知、實時優化、自主決策的新發展階段,為我國從制造大國向質量強國轉型提供核心支撐。

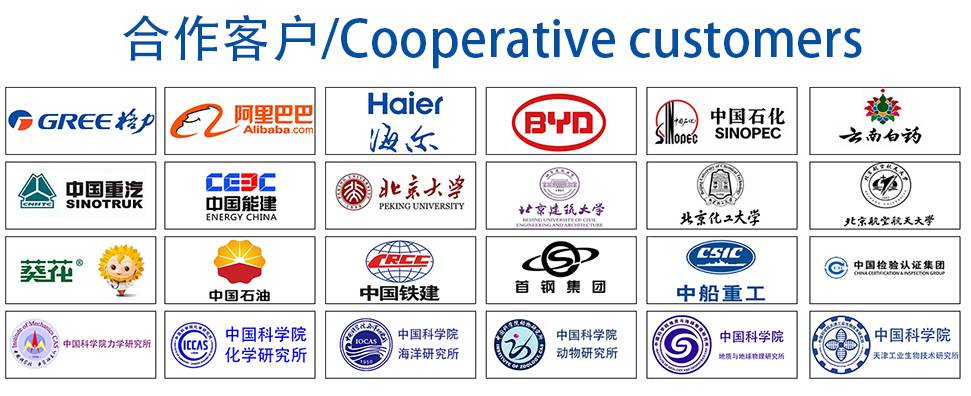