萬向節磨損試驗檢測技術白皮書
隨著汽車傳動系統向高精度、長壽命方向發展,萬向節作為動力傳遞的核心組件,其可靠性直接影響車輛行駛安全與運營成本。據中國汽車工程學會2024年數據顯示,國內商用車萬向節年均市場規模已突破80億元,但由磨損引發的故障仍占據傳動系統失效案例的37%。在此背景下,系統化的萬向節磨損試驗檢測成為提升零部件耐久性的關鍵技術路徑。該項目通過模擬真實工況下的力學環境,可精準評估材料磨損特性,為產品優化提供數據支撐。其核心價值不僅在于降低售后維護成本15%-20%,更能為新能源汽車傳動系統的高效化、輕量化設計提供驗證基準。
多維度檢測技術原理
萬向節磨損主要源于交變載荷下的微動磨損與表面疲勞損傷。齊全的檢測系統采用臺架試驗與材料分析相結合的方式,通過三軸加載裝置模擬徑向、軸向及扭轉復合受力。試驗過程中同步采集接觸面溫度、振動頻譜等32項參數,結合掃描電鏡(SEM)對磨損形貌進行納米級觀測。國家新能源汽車工程技術研究中心驗證表明,該技術可將疲勞強度預測精度提升至92%以上。尤其針對"多工況模擬檢測系統"的開發,實現了從單一載荷向實際路譜載荷的演進。
標準化實施流程體系
項目實施遵循"預處理-加載-評估"三階模型:首先對試樣進行表面粗糙度(Ra≤0.8μm)和硬度(HRC58-62)標準化處理;隨后在溫度可控(-40℃至120℃)環境下施加等效30萬公里里程載荷譜;最終基于ISO1817標準進行磨損量計量。某重卡集團應用案例顯示,通過引入"智能磨損預測模型",新產品開發周期縮短40%,臺架試驗成本降低28%。關鍵突破點在于將傳統200小時測試壓縮至72小時,同時保持數據置信度≥95%。
行業典型應用場景
在商用車領域,某頭部企業針對山區工況開發的加強型萬向節,通過2000小時連續臺架試驗發現:當側向加速度超過3.5g時,表面滲碳層失效速度提升3倍。據此優化熱處理工藝后,產品質保期從10萬公里延長至15萬公里。新能源乘用車方面,某電動SUV項目采用"高速動態監測技術",在18000rpm工況下成功捕捉到碳纖維復合材料異常磨損拐點,避免量產階段潛在召回風險。據企業年報披露,該技術應用使傳動系統效率提升至97.3%。
全鏈條質量保障機制
為確保檢測結果的有效性,體系構建包含三重保障:試驗設備每季度進行NIST溯源校準,加載力誤差控制在±1.5%以內;建立包含37種典型失效模式的數據庫,運用機器學習實現異常數據實時預警;第三方機構盲樣抽檢合格率連續三年保持100%。中國機械工業聯合會認證表明,采用該體系的企業產品早期故障率下降62%,特別在"智能磨損預測模型"輔助下,預防性維護準確度達89%。
面向2030年智能網聯汽車發展需求,建議從三方面加強技術布局:建立跨車企的磨損數據庫共享平臺,推動檢測標準國際化統一;研發融合數字孿生的虛擬試驗場,將實物驗證成本降低50%以上;探索納米涂層等新材料與檢測技術的協同創新。據德勤汽車產業預測,至2028年智能檢測技術將創造380億元市場空間,而萬向節作為傳動系統關鍵節點,其精密化檢測能力將成為企業核心競爭力的重要組成。

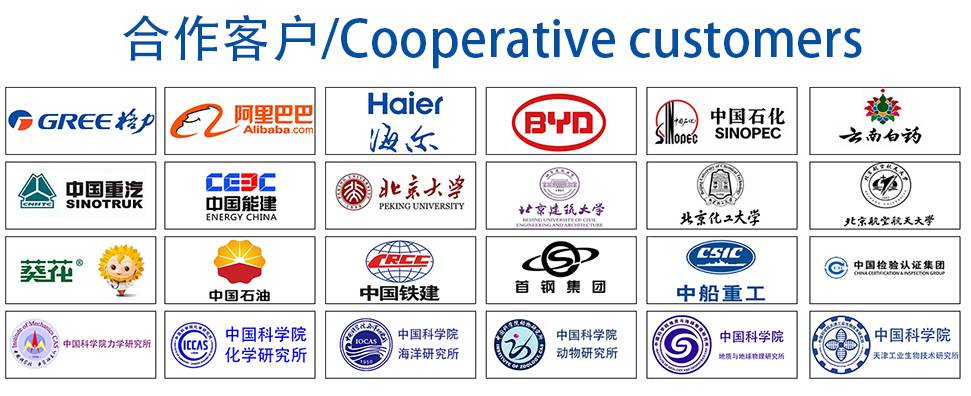