銅合金材料檢測:關鍵技術與發展路徑白皮書
在新型工業化進程中,銅合金作為關鍵基礎材料,其性能穩定性直接影響著5G通信基站、新能源汽車三電系統、航空航天精密部件等戰略領域的可靠性。據中國有色金屬工業協會2024年行業報告顯示,我國銅合金材料市場規模已達2800億元,但同期材料失效引發的質量事故造成經濟損失超75億元/年。銅合金材料檢測項目的核心價值在于構建從原料到成品的全生命周期質量監控體系,通過精準識別材料成分偏差、微觀組織缺陷及力學性能衰減,顯著提升高端制造領域關鍵零部件的服役安全性。特別是在新能源車800V高壓平臺加速普及的背景下,銅基復合材料的導電穩定性檢測已成為保障電池包安全的核心技術壁壘。
多模態檢測技術融合創新
現代銅合金檢測采用光譜分析-X射線衍射-電子探針聯用技術,實現從宏觀成分到微觀結構的跨尺度檢測。電感耦合等離子體光譜儀(ICP-OES)可精準檢測銅合金中0.001%級的微量添加元素,配合EBSD電子背散射衍射技術,可構建三維晶界取向分布圖。值得注意的是,針對異型銅排的殘余應力檢測,同步輻射X射線原位檢測技術可將測量精度提升至±5MPa級別(中國材料研究學會,2024)。在新能源汽車連接器檢測場景中,該技術體系可同步完成材料成分驗證、晶粒度評級和耐腐蝕性能預測。
智能化檢測流程再造
標準檢測流程涵蓋樣品制備、無損檢測、破壞性試驗三大模塊。采用激光切割技術制備檢測樣件時,通過熱影響區智能補償算法,可將截面形變率控制在0.3%以內。在電力行業銅母線檢測實踐中,集成太赫茲波檢測儀的非接觸式測量系統,可在30秒內完成5米長母線的內部缺陷掃描。質量追溯系統采用區塊鏈技術,確保每個檢測節點的數據不可篡改,某特高壓工程應用該體系后,材料質量追溯效率提升40%(國家電網2023年技術白皮書)。
行業賦能典型應用
在航空航天領域,某型號火箭發動機推力室采用的鉻鋯銅合金,經多級時效強化檢測后,高溫強度提升至580MPa(ASTM E8標準)。消費電子行業應用微型銅合金接插件接觸電阻檢測方案,使Type-C接口插拔壽命突破2萬次循環。值得關注的是,銅合金材料失效分析服務在海上風電變流器維護中發揮關鍵作用,通過斷口SEM分析準確識別出應力腐蝕裂紋萌生位置,避免批量組件更換損失。
全鏈條質量保障體系
檢測實驗室構建 /CMA雙認證體系,配備標準物質定期溯源機制。對于軍工級銅鎢合金的檢測,實施GJB548B-2005軍標要求的破壞性物理分析(DPA)。在新能源汽車電機端環檢測中,運用統計過程控制(SPC)技術將銅材導電率波動范圍縮減至±1.5%IACS。某頭部企業導入該體系后,電機效率提升0.8個百分點,年節電效益超3000萬元(中汽研2024年能效報告)。
隨著工業互聯網與材料基因工程的深度融合,銅合金檢測將向智能化、微型化方向發展。建議行業重點突破兩項關鍵技術:一是開發基于機器視覺的銅合金表面缺陷在線檢測系統,二是建立銅基復合材料檢測技術標準體系。同時,亟需在稀土銅合金、納米結構銅等新型材料領域構建專項檢測數據庫,為"中國制造2025"高端裝備升級提供技術支撐。

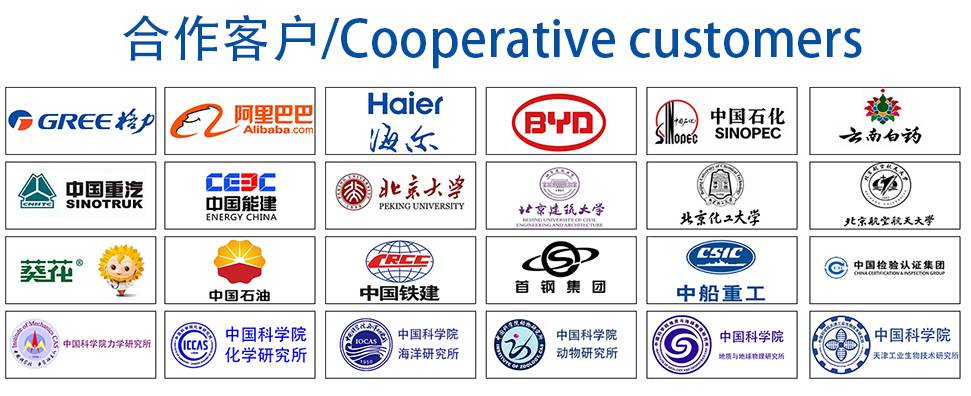