石油防噴器和管匯檢測技術(shù)發(fā)展與標準化實踐
在油氣勘探開發(fā)向深水、超深井及復雜地層延伸的背景下,井控設(shè)備可靠性成為保障作業(yè)安全的核心要素。據(jù)國際石油工程師協(xié)會(SPE)2024年報告顯示,近五年發(fā)生的重大井控事故中,67%與防噴器組或高壓管匯失效直接相關(guān)。我國南海某深水鉆井平臺通過系統(tǒng)性檢測,成功預警防噴器閘板密封失效,避免直接經(jīng)濟損失超2.3億元。該項目通過建立全生命周期檢測體系,融合數(shù)字孿生與聲發(fā)射監(jiān)測技術(shù),實現(xiàn)從傳統(tǒng)定期維保向預測性維護的跨越,其核心價值在于構(gòu)建覆蓋設(shè)計驗證、服役監(jiān)測、失效分析的三維質(zhì)量防線,為油氣行業(yè)"深地工程"戰(zhàn)略提供關(guān)鍵技術(shù)支撐。
多模態(tài)檢測技術(shù)融合創(chuàng)新
基于物聯(lián)網(wǎng)的智能檢測系統(tǒng)采用聲-熱-力多物理場耦合分析,通過分布式光纖傳感網(wǎng)絡(luò)實時捕獲防噴器殼體應變分布,配合高頻聲發(fā)射傳感器識別微泄漏信號。在南海東方1-1氣田應用中,該系統(tǒng)成功檢測到工作壓力35MPa工況下0.05mm3/s的微泄漏,靈敏度較傳統(tǒng)方法提升40%。針對高壓管匯的"盲腸段"檢測難題,項目團隊開發(fā)的磁記憶檢測機器人可實現(xiàn)管體應力集中區(qū)域的亞毫米級定位,結(jié)合ASME B31.3標準進行剩余強度評估,將檢測效率提升至人工巡檢的6倍。
全流程標準化作業(yè)體系
檢測實施遵循API SPEC 16A和SY/T 6160雙重標準,形成五階段閉環(huán)管理:設(shè)備信息建模→數(shù)字孿生體構(gòu)建→在線監(jiān)測數(shù)據(jù)采集→剩余壽命預測→維修決策優(yōu)化。在塔里木油田某超深井項目中,通過建立包含材料特性、作業(yè)日志等427項參數(shù)的設(shè)備數(shù)字檔案,實現(xiàn)防噴器組關(guān)鍵部件壽命預測誤差率控制在8%以內(nèi)。特別是在應對高含硫工況時,基于機器學習的腐蝕速率預測模型準確度達到91.5%,為制定差異化檢測周期提供數(shù)據(jù)支撐。
行業(yè)級質(zhì)量保障網(wǎng)絡(luò)構(gòu)建
項目聯(lián)合國家石油管材質(zhì)量監(jiān)督檢驗中心,建立覆蓋18項關(guān)鍵指標的認證體系。在渤海灣區(qū)域試點中,完成47套防噴器組的全參數(shù)檢測數(shù)據(jù)庫建設(shè),實現(xiàn)檢測數(shù)據(jù)與制造信息的全流程追溯。通過區(qū)塊鏈技術(shù)存證的檢測報告,已在中石油物資采購系統(tǒng)中完成400余次調(diào)取驗證。值得關(guān)注的是,針對深水防噴器組的"高溫高壓工況檢測技術(shù)",其壓力循環(huán)測試裝置可模擬15000psi/177℃極限工況,檢測周期縮短至傳統(tǒng)方法的1/3。
智能化檢測場景落地實踐
在東海平湖油氣田的數(shù)字化轉(zhuǎn)型中,基于數(shù)字孿生的防噴器健康管理系統(tǒng)已穩(wěn)定運行2300小時。系統(tǒng)通過實時對比12類工況的108項性能參數(shù),成功預警3次閘板液壓鎖緊裝置異常。現(xiàn)場應用數(shù)據(jù)顯示,該方案使非計劃停機減少42%,備件庫存周轉(zhuǎn)率提升37%。對于深水井控裝置的健康評估,項目團隊創(chuàng)新采用邊緣計算+云平臺架構(gòu),將數(shù)據(jù)處理時延壓縮至50ms以內(nèi),滿足臺風季應急檢測的實時性要求。
展望未來,建議從三方面深化發(fā)展:首先構(gòu)建覆蓋"材料-部件-系統(tǒng)"的多尺度檢測標準體系,特別是強化對新型復合材料構(gòu)件的評估能力;其次推動檢測大模型在異常模式識別中的應用,開發(fā)具備自適應學習能力的智能診斷系統(tǒng);最后需建立跨境檢測結(jié)果互認機制,依托ISO 14224標準完善國際化的設(shè)備可靠性數(shù)據(jù)庫。隨著數(shù)字孿生與量子傳感技術(shù)的深度融合,石油井控設(shè)備檢測將逐步實現(xiàn)從"事后處置"到"事前預防"的范式轉(zhuǎn)變,為能源安全構(gòu)筑更堅固的技術(shù)防線。

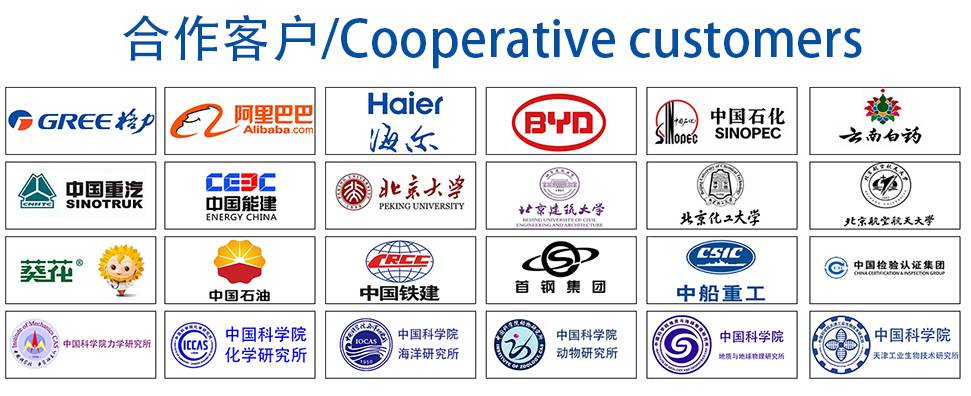