容積泵零部件液壓與滲漏試驗檢測概述
容積泵作為工業流體輸送的核心設備,其性能穩定性直接關系到生產系統的安全與效率。液壓與滲漏試驗是容積泵零部件出廠及維修后必檢的關鍵環節,旨在驗證零部件的耐壓能力、密封性能及長期運行的可靠性。該檢測通過模擬實際工況下的壓力載荷和介質滲透條件,精準識別泵體、密封件、閥組等部件的潛在缺陷,確保其符合國家標準(如GB/T 7784)及行業技術要求。試驗過程中需結合泵型特點(如齒輪泵、柱塞泵、螺桿泵等),針對關鍵零部件設計差異化的檢測方案,以覆蓋材料疲勞、密封失效、接口滲漏等主要風險點。
核心檢測項目及技術要求
1. 泵體承壓測試
采用水壓或油壓介質進行,試驗壓力通常為額定工作壓力的1.5倍,保壓時間≥30分鐘。需監測泵體變形量(≤0.05%)、表面滲漏及異常振動,重點檢查鑄造缺陷區域和焊縫連接處。
2. 密封裝置滲漏檢測
包括機械密封、填料密封等組件,需在動態工況下驗證密封效果。使用氦質譜檢漏法或氣泡法檢測泄漏率,要求靜態泄漏量≤5mL/h,動態泄漏量≤10mL/h(依據API 682標準)。
3. 連接部件密封性驗證
對法蘭接口、螺紋連接等部位進行氣壓試驗(0.6-1.0MPa),通過涂刷檢漏液觀察氣泡形成情況,要求所有連接點30分鐘內無連續氣泡產生。
4. 安全閥與壓力補償機構測試
驗證安全閥啟閉壓力精度(誤差≤±2%設定值),檢測壓力補償裝置的響應時間(≤0.5秒)。使用流量計記錄溢流狀態下壓力波動,確保系統壓力穩定性。
試驗流程與判定標準
試驗流程包括預處理(清潔度檢查)→分級加壓(按20%階梯遞增)→保壓監測→降壓觀察→數據記錄五個階段。判定依據需滿足:①無可見塑性變形;②壓降率≤3%/h;③滲漏點數量≤3處且單點泄漏量<0.1mL/min。對于齒輪泵需額外檢測齒面接觸區的微滲漏,柱塞泵則重點關注缸體與滑靴配合面的油膜完整性。
常見失效模式及改進措施
試驗中常發現密封圈老化(占比42%)、鑄件砂眼(28%)、裝配間隙偏差(20%)三類問題。針對性地采取表面納米涂層強化、激光熔覆修復、裝配公差優化(控制到±0.01mm)等措施,可顯著提升零部件合格率。某案例顯示,通過改進柱塞桿硬化工藝,泵體耐壓能力提升37%,運行壽命延長至8000小時以上。
檢測設備與技術發展
現代檢測已集成PLC控制系統、高精度壓力傳感器(±0.25%FS)和紅外熱成像技術,實現實時數據采集與智能診斷。基于機器視覺的自動滲漏識別系統可將檢測效率提升60%,同時AI算法能預測零部件剩余壽命,推動檢測從被動驗證向主動預防轉型。

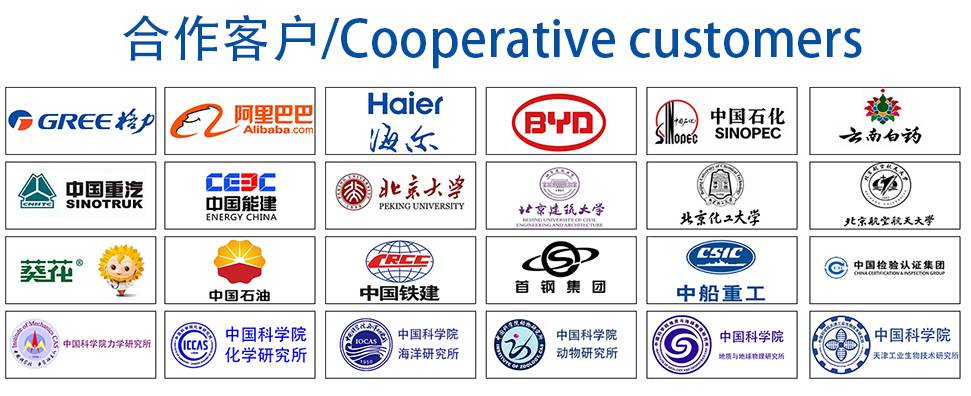