初軋坯和鋼坯檢測的重要性
在鋼鐵生產流程中,初軋坯和鋼坯作為軋制工藝的關鍵中間產品,其質量直接決定了后續型材、板材等終軋產品的性能指標。初軋坯是指通過初軋機對鋼錠進行開坯加工后形成的矩形或方形截面的半成品,而鋼坯則泛指經過連鑄或軋制工藝形成的各類斷面形狀(如方坯、板坯、圓坯)的中間材料。由于這些坯料需要經歷高溫軋制、冷卻等多道工序,其內部組織、表面缺陷、尺寸精度等參數必須經過系統性檢測,才能確保成品鋼材的力學性能、加工性能及使用壽命符合行業標準要求。
核心檢測項目及技術方法
1. 化學成分分析
采用光譜分析儀對坯料進行元素含量檢測,重點監控C、Mn、Si、S、P等主量元素及微量合金元素的配比是否符合鋼種要求。通過鉆孔取樣或表面直讀技術,確保材料成分均勻性滿足GB/T 223系列標準。
2. 表面質量檢測
通過目視檢查結合渦流探傷、磁粉探傷等無損檢測技術,系統排查表面裂紋、折疊、結疤等缺陷。采用三維激光掃描儀可實現0.1mm級精度的表面形貌數字化建模,特別適用于檢測高溫坯料的氧化鐵皮殘留情況。
3. 尺寸精度測量
使用高精度卡尺、激光測距儀等設備對坯料的長度、寬度、厚度等幾何尺寸進行全截面檢測。方坯對角線偏差需控制在±2mm/m以內,板坯寬度公差應滿足±5mm的行業規范要求。
4. 內部缺陷檢測
采用超聲波探傷(UT)技術對坯料內部進行分層、氣孔、夾雜物等缺陷的立體檢測,可發現最小0.5mm當量的內部缺陷。對于特殊用途坯料,需配合工業CT進行三維成像掃描,檢測精度可達50μm級別。
5. 力學性能測試
通過取樣進行拉伸試驗、沖擊試驗等,測定坯料的屈服強度、抗拉強度、延伸率等關鍵指標。試驗需嚴格按照GB/T 228.1金屬材料室溫拉伸試驗方法執行,試樣加工需保證與軋制方向的一致性。
6. 金相組織分析
采用光學顯微鏡和掃描電鏡(SEM)觀察晶粒度、珠光體比例、帶狀組織等微觀結構特征。通過EBSD技術可精確分析晶粒取向分布,為優化軋制工藝提供數據支持。
7. 殘余應力檢測
使用X射線衍射法或鉆孔法測定坯料內部殘余應力分布,特別關注軋制過程中因溫度梯度產生的熱應力。應力值需控制在材料屈服強度的30%以下,避免后續加工出現變形或裂紋擴展。
檢測體系的質量控制
現代鋼鐵企業普遍建立三級檢測體系:在線檢測(如熱態表面檢測系統)、過程抽檢(每批次取樣)和實驗室精密分析。通過建立MES系統實現檢測數據實時上傳,結合SPC統計過程控制技術,可動態優化軋制參數,將坯料不合格率降低至0.3%以下。同時需定期對檢測設備進行計量校準,確保超聲波探傷儀靈敏度誤差≤1dB,光譜分析儀的重復性偏差≤0.5%。

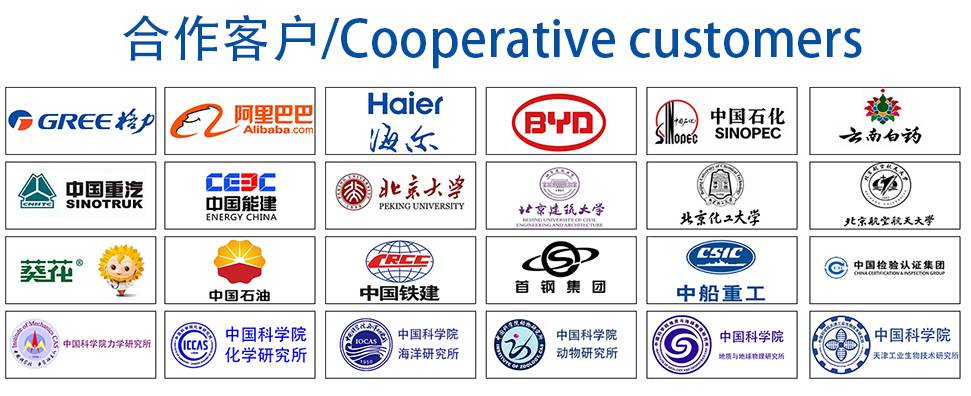