石油管檢測的重要性與技術(shù)發(fā)展
在石油天然氣工業(yè)中,管道作為能源輸送的核心載體,其安全性與可靠性直接關(guān)系到生產(chǎn)效率和環(huán)境安全。據(jù)統(tǒng)計,每年因管道腐蝕、裂紋或焊接缺陷導(dǎo)致的泄漏事故造成的經(jīng)濟損失超過50億美元。石油管檢測技術(shù)通過系統(tǒng)性評估管道完整性,成為預(yù)防事故、延長使用壽命的關(guān)鍵環(huán)節(jié)。當(dāng)前行業(yè)采用的檢測體系已涵蓋材質(zhì)分析、力學(xué)性能測試、無損檢測及智能化監(jiān)控等20余項核心指標(biāo),形成了覆蓋全生命周期的質(zhì)量管控網(wǎng)絡(luò)。
1. 化學(xué)成分與冶金性能檢測
采用直讀光譜儀(OES)和電感耦合等離子體(ICP)技術(shù)對石油管的C、Mn、Cr、Mo等元素進行定量分析,確保符合API 5CT標(biāo)準(zhǔn)。金相顯微鏡觀察晶粒度級別(通常要求6-8級),配合顯微硬度計測量HV值,評估熱處理工藝對微觀組織的影響。X射線衍射(XRD)用于檢測殘余奧氏體含量,預(yù)防氫致開裂風(fēng)險。
2. 幾何尺寸與形位公差檢測
三維激光掃描系統(tǒng)實現(xiàn)0.05mm精度的外徑、壁厚測量,結(jié)合數(shù)字圖像處理技術(shù)自動識別橢圓度和彎曲度。特殊設(shè)計的通徑規(guī)(最小通過直徑≥95%標(biāo)稱值)驗證管道直線度,超聲波測厚儀在圓周方向設(shè)置32個采樣點,構(gòu)建壁厚分布云圖。對于螺紋連接部位,使用三坐標(biāo)測量機檢測錐度、齒高和緊密距,確保API螺紋的密封性能。
3. 力學(xué)性能綜合測試
依據(jù)ASTM A370標(biāo)準(zhǔn)進行拉伸試驗,重點監(jiān)控屈服強度(Rt0.5)、抗拉強度(Rm)和屈強比(通常≤0.93)。夏比V型缺口沖擊試驗在-46℃低溫環(huán)境下測定沖擊功,確保管材的低溫韌性。擴口試驗要求達到15%擴口率無裂紋,彎曲試驗采用芯棒直徑3倍于管徑的測試條件。全尺寸疲勞試驗?zāi)M管道實際應(yīng)力條件,循環(huán)次數(shù)需超過10^7次。
4. 腐蝕與缺陷無損檢測
漏磁檢測(MFL)技術(shù)可識別最小0.5mm深的腐蝕坑,檢測速度達到3m/s。超聲波相控陣(PAUT)實現(xiàn)多角度掃查,對橫向裂紋的檢出率提升至99%。遠(yuǎn)場渦流(RFET)穿透厚壁管檢測內(nèi)部缺陷,電磁聲傳感器(EMAT)實現(xiàn)非接觸式氧化層下裂紋探測。近年來發(fā)展的管道內(nèi)檢測器(智能清管器)集成慣性導(dǎo)航和GIS定位,可構(gòu)建管道三維缺陷圖譜。
5. 環(huán)境適應(yīng)性專項檢測
HIC氫致開裂試驗在NACE TM0284溶液中進行96小時浸泡,斷面裂紋率需<2%。SSC硫化應(yīng)力腐蝕試驗采用四點彎曲法,加載80%YS應(yīng)力評估開裂敏感性。高溫高壓模擬裝置可復(fù)現(xiàn)150℃、35MPa工況下的應(yīng)力腐蝕行為。對于海底管道,還需開展陰極保護電位檢測和AC干擾評估,確保保護電位維持在-850mV~-1100mV(CSE)區(qū)間。
6. 智能檢測技術(shù)新趨勢
數(shù)字射線檢測(DR)取代傳統(tǒng)膠片技術(shù),缺陷識別效率提升70%。基于深度學(xué)習(xí)的圖像分析系統(tǒng)可自動分級缺陷類型,準(zhǔn)確率超過95%。分布式光纖傳感(DTS)實現(xiàn)管道全線溫度/應(yīng)變實時監(jiān)測,空間分辨率達到1米。衛(wèi)星InSAR技術(shù)監(jiān)測地面沉降,每年可預(yù)警毫米級位移風(fēng)險。2023年發(fā)布的API 1163新版標(biāo)準(zhǔn)已將數(shù)字化檢測數(shù)據(jù)管理納入強制要求。
通過構(gòu)建"材料基礎(chǔ)檢測+服役性能評價+智能在線監(jiān)控"的三維質(zhì)量體系,現(xiàn)代石油管檢測技術(shù)已將管道事故率降至0.3次/千公里·年以下。隨著數(shù)字孿生、量子傳感等新技術(shù)的應(yīng)用,石油管道的檢測精度和效率將進入新的發(fā)展階段。

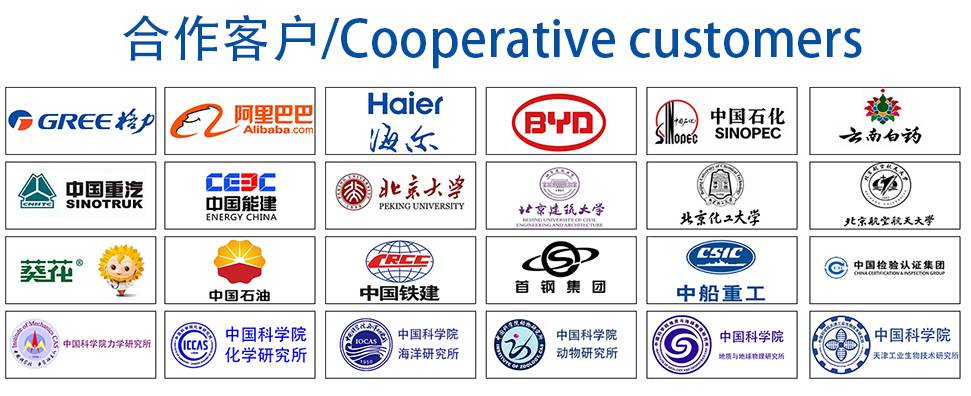