可鍛鑄鐵管路連接件檢測的重要性
可鍛鑄鐵管路連接件作為工業管道系統中廣泛應用的組件,其質量直接影響管道系統的密封性、耐壓性和使用壽命。這類連接件常用于水暖、燃氣、石油化工等領域,主要承擔管道連接、轉向和分流功能。由于可鍛鑄鐵材料兼具鑄造便利性和機械強度優勢,其檢測需重點關注材料性能、加工精度及耐腐蝕能力。規范的檢測流程不僅能確保產品符合國際標準(如ASTM A197、GB/T 3287),更能有效預防因連接件失效引發的泄漏或安全事故,對保障工業生產和公共安全具有重要意義。
核心檢測項目及方法
1. 化學成分分析
通過光譜分析儀檢測材料中碳、硅、錳、硫、磷等元素的含量,確保符合可鍛鑄鐵的材質標準(碳當量2.2%-2.8%)。重點監控硫磷含量以防止脆性斷裂。
2. 機械性能測試
采用萬能試驗機進行抗拉強度(≥330MPa)、延伸率(≥10%)和硬度(HRB 65-90)檢測,驗證材料韌性與強度的平衡性。沖擊試驗需滿足-20℃低溫下的韌性要求。
3. 尺寸與形位公差檢測
使用三坐標測量儀、螺紋規等工具,對連接件的螺紋精度、法蘭平行度、端口垂直度等關鍵尺寸進行全檢,確保與標準管件的兼容性。
4. 耐腐蝕性能評估
通過鹽霧試驗(72小時中性鹽霧)、濕熱試驗等模擬惡劣環境,結合金相顯微鏡觀察表面鍍鋅層或涂層的致密性,評估長期抗銹蝕能力。
5. 密封性壓力測試
在1.5倍工作壓力下進行靜壓試驗(通?!?.4MPa),保壓30分鐘無滲漏。動態脈沖試驗需模擬實際工況進行10萬次壓力循環。
特殊檢測項目
1. 金相組織分析
通過顯微鏡觀察石墨形態(要求團絮狀石墨占比>85%),確認退火工藝是否充分消除白口組織,避免脆性缺陷。
2. 無損探傷檢測
采用磁粉探傷(MT)或滲透探傷(PT)檢測表面微裂紋,超聲波探傷(UT)則用于內部氣孔、夾渣等缺陷的深度定位。
3. 裝配兼容性驗證
在實際管路中模擬安裝,測試不同批次連接件與閥門、管材的配合松緊度,防止因公差累積導致密封失效。
質量控制標準與趨勢
當前檢測技術已逐步引入數字化手段,如基于機器視覺的自動尺寸檢測系統和在線光譜分析儀。企業需嚴格遵循ISO 5922、EN 10242等國際標準,同時結合智能化檢測設備提升質量控制效率。定期比對ASTM與國標差異(如GB/T 3287的延伸率要求更嚴格),對出口產品實施雙重標準驗證,將成為行業質量管控的新常態。

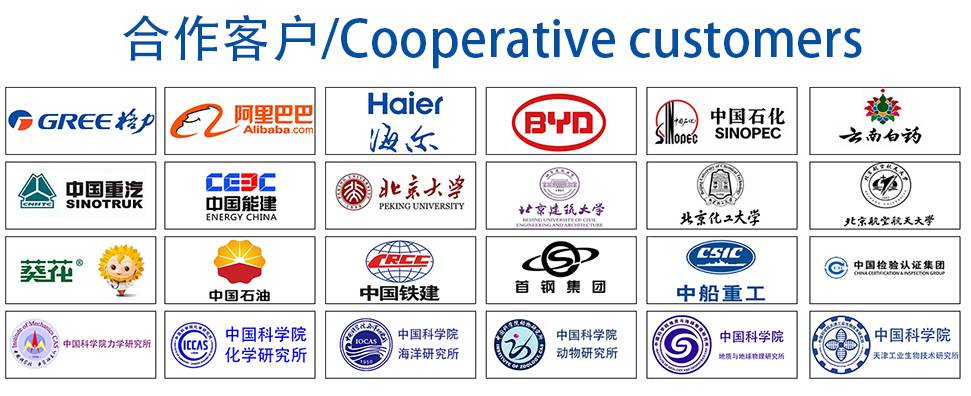