航空用鈦及鈦合金鍛件檢測的重要性
在航空工業中,鈦及鈦合金因其高強度、耐腐蝕性、耐高溫和低密度等優異性能,被廣泛應用于發動機部件、機身結構件及起落裝置等關鍵部位。然而,鍛件的制造工藝復雜,任何微小的缺陷都可能對航空器的安全性和可靠性造成嚴重影響。因此,對鈦及鈦合金鍛件進行系統性檢測是保障航空裝備質量的核心環節,需要覆蓋材料性能、加工工藝及成品質量的全流程驗證。
檢測項目及技術要求
1. 化學成分分析
通過光譜分析(OES)、X射線熒光光譜(XRF)等方法,驗證鈦合金中主元素(Ti、Al、V等)及雜質元素(O、N、H等)的含量是否符合AMS 4928、GB/T 3620等標準要求。例如,氧含量超過0.20%會顯著降低材料韌性。
2. 力學性能測試
包括拉伸試驗(抗拉強度、屈服強度、延伸率)、沖擊試驗(夏比沖擊功)及硬度測試(布氏/洛氏硬度)。需參照ASTM E8/E23標準,確保鍛件在-50℃至300℃工況下的性能穩定性。
3. 微觀組織檢測
采用金相顯微鏡、掃描電鏡(SEM)觀察α相、β相分布及晶粒度(ASTM E112評級)。例如,航空發動機壓氣機葉片要求晶粒度達到5-8級,以平衡強度與疲勞性能。
4. 無損檢測(NDT)
綜合應用超聲波檢測(UT)檢測內部裂紋、夾雜;滲透檢測(PT)識別表面缺陷;X射線檢測(RT)驗證復雜結構的完整性。依據NAS 410標準,缺陷尺寸需嚴格控制在0.8mm以下。
5. 尺寸與幾何公差檢測
使用三坐標測量機(CMM)、激光掃描儀等設備,驗證鍛件的輪廓度、平面度及關鍵裝配尺寸是否符合設計圖紙要求,公差通常需控制在±0.05mm以內。
6. 殘余應力分析
通過X射線衍射法或盲孔法測定鍛件內部殘余應力分布,避免因應力集中導致后期變形或開裂。航空級鍛件殘余應力值一般需低于材料屈服強度的30%。
7. 腐蝕與表面質量檢測
進行鹽霧試驗(ASTM B117)、應力腐蝕試驗(ASTM G36)評估耐蝕性;同時檢查表面氧化層、污染及裂紋,確保符合AMS 2488D規定的表面處理標準。
檢測流程標準化管理
航空鍛件的檢測需嚴格遵循AS9100質量管理體系,實施批次追溯制度,并通過數字化檢測報告(含原始數據、圖譜及3D模型對比)實現全生命周期質量監控。檢測機構需獲得NADCAP認證,確保檢測結果的國際互認性。

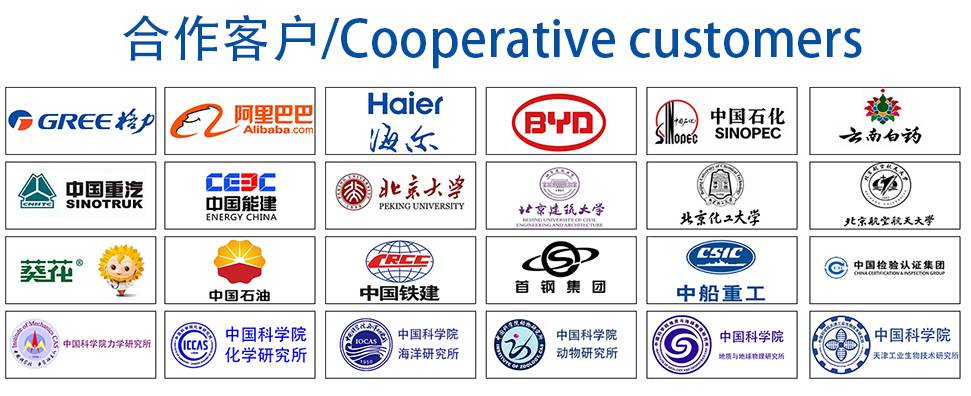