精密數控臥式車床與車削中心檢測的核心價值
在高端裝備制造領域,精密數控臥式車床和車削中心作為復雜零部件加工的核心設備,其性能直接關系到航空航天、汽車制造、精密模具等行業的加工精度與生產效率。隨著現代制造業對μ級甚至納米級精度的嚴苛要求,系統性檢測成為確保設備穩定性、延長使用壽命的核心環節。通過科學的檢測流程,可精準識別設備誤差源,優化切削參數,降低廢品率,為高附加值產品提供技術保障。
幾何精度檢測體系
幾何精度檢測是評價設備基礎性能的首要環節,包含主軸系統、導軌系統及傳動系統的綜合檢測。關鍵項目包括:主軸徑向/軸向跳動(ISO 230-1標準)、滑板移動直線度(激光干涉儀測量)、X/Z軸垂直度(方形規配合千分表)、尾座軸線與主軸同軸度(三點接觸法)。對于車削中心還須檢測B/C軸回轉定位精度(球桿儀測試),確保多軸聯動時空間軌跡的幾何一致性。
位置精度與動態性能檢測
通過激光干涉儀執行ISO 230-2標準的位置精度檢測,測量內容包括各軸定位精度、重復定位精度及反向間隙補償。動態檢測則聚焦于加減速特性(圓度測試)、伺服系統響應頻率(頻響分析)以及多軸聯動輪廓精度(NAS 979標準試件加工)。特別針對車削中心的動力刀具系統,需驗證換刀重復定位精度(≤0.005mm)和刀具端面跳動(≤0.008mm)。
熱穩定性與振動分析
構建溫度-形變關聯模型,采用紅外熱成像儀監測主軸溫升曲線(連續8小時空載試驗),通過位移傳感器記錄關鍵部件的熱膨脹量。振動檢測涵蓋主軸箱固有頻率分析(FFT頻譜儀)和切削工況下的振動烈度檢測(三向加速度傳感器),確保設備在寬頻域范圍內的動態剛性。
智能化檢測技術拓展
近年興起的數字孿生技術為設備檢測開辟新路徑,通過植入式傳感器網絡實時采集振動、溫度、電流等多維度數據,結合AI算法實現磨損預測與精度補償。例如利用數字雙軸自準直儀進行在線導軌磨損量監測,或通過聲發射技術識別刀具崩刃等異常工況,顯著提升檢測時效性與預測準確性。

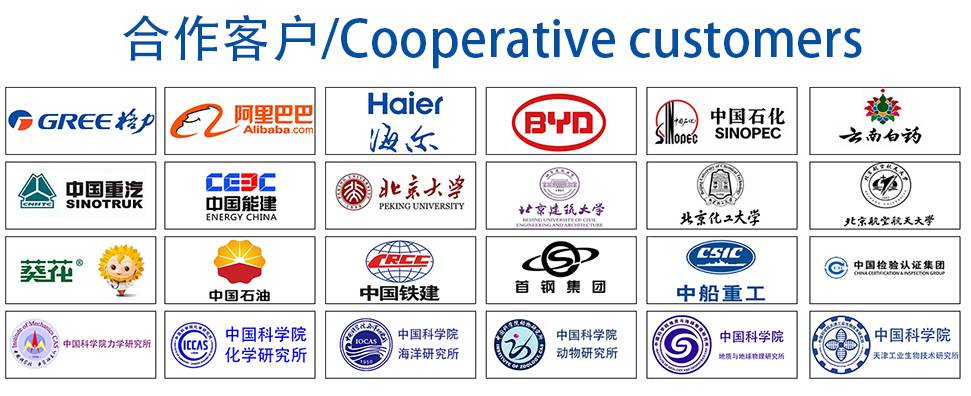