汽車發電機軸承檢測的重要性與檢測項目解析
汽車發電機軸承作為發電機核心部件之一,承擔著支撐轉子旋轉、降低摩擦損耗的重要作用。據統計,約35%的發電機故障源于軸承異常,輕則導致異響、發電量下降,重則引發轉子卡死甚至發動機熄火。因此,定期開展軸承檢測是保障車輛電力系統穩定運行的關鍵環節。本文將從靜態檢測到動態性能分析,系統梳理發電機軸承檢測的核心項目與技術要點。
一、外觀與尺寸精度檢測
通過目視和測量工具檢查軸承表面是否存在劃痕、銹蝕、變形等缺陷,使用千分尺測量內外圈直徑、寬度及滾道圓度。允許公差需參照ISO 492標準,軸向游隙應控制在0.05-0.15mm范圍內。特殊情況下需通過三維坐標儀對軸承座進行同心度掃描,確保安裝面的同軸度誤差≤0.03mm。
二、運轉性能動態檢測
在模擬負載條件下,采用振動加速度傳感器(頻率范圍5-10kHz)監測軸承運行狀態。正常工況下振動值應低于4.5mm/s(RMS值),若出現高頻尖峰則提示滾道剝落。同步使用紅外熱像儀監測溫升,連續運轉30分鐘后溫度不得超過環境溫度+45℃。對于帶密封件的軸承,還需檢測旋轉扭矩變化,異常阻力增大可能預示潤滑失效。
三、潤滑狀態與材料分析
通過光譜儀檢測潤滑脂中的金屬磨粒成分,鐵元素含量超過150ppm即需預警。采用傅里葉紅外光譜分析潤滑劑氧化程度,酸值(TAN)升高0.5mgKOH/g表明需更換油脂。對于高里程軸承,可取樣進行金相檢測,觀察是否存在顯微裂紋或貝氏體轉變等材料劣化現象。
四、智能化檢測技術應用
新型MEMS傳感器可實時監測軸承運行參數,結合機器學習算法實現早期故障預警。實驗數據顯示,基于聲發射技術的檢測系統對微點蝕的識別準確率達92%,比傳統方法提前300小時發現異常。此外,采用工業內窺鏡可對裝機軸承進行免拆解檢查,大幅提升檢測效率。
通過上述多維度的檢測體系,可精準判斷軸承剩余壽命,建議每行駛5萬公里或出現異常噪音時進行專項檢測。規范的檢測流程不僅能預防突發故障,更能延長發電機整體使用壽命30%以上,為行車安全提供可靠保障。

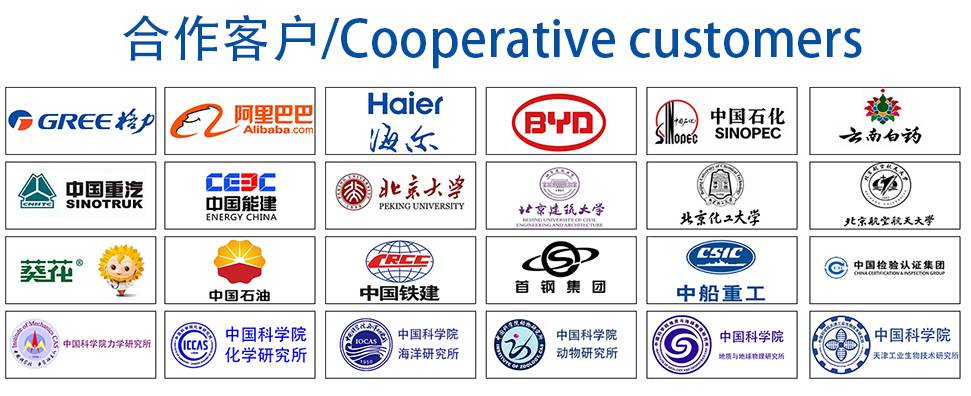