套筒型直線球軸承作為精密機械傳動系統中的核心部件,廣泛應用于自動化設備、數控機床、精密儀器等領域。其通過鋼球在套筒內外圈之間的滾動實現低摩擦直線運動,具有高精度、低噪音、長壽命等特點。隨著工業自動化對運動精度和可靠性的要求日益提高,軸承的檢測成為確保設備性能的關鍵環節。科學規范的檢測流程不僅能及時發現制造缺陷,還能為軸承選型和應用提供數據支撐,有效預防設備異常磨損和失效風險。
一、主要檢測項目及方法
1. 尺寸精度檢測:使用三坐標測量儀對套筒內徑、外徑、長度、圓度、圓柱度等關鍵尺寸進行全檢,公差范圍需嚴格控制在ISO 286標準規定的H6/g5精度等級內。
2. 表面質量檢測:通過高倍顯微鏡或表面粗糙度儀檢測套筒內壁、鋼球接觸面的Ra值(表面粗糙度),要求Ra≤0.4μm。同時目視檢查是否存在劃痕、毛刺、銹蝕等表面缺陷。
3. 旋轉靈活性測試:將軸承安裝在模擬工作臺上,使用扭力計測量啟動扭矩和運行扭矩,標準工況下啟動扭矩應≤0.03N·m,運行扭矩波動幅度不超過±15%。
二、性能可靠性驗證
1. 載荷能力測試:通過萬能試驗機進行靜態徑向載荷試驗,記錄額定動載荷(C值)和靜載荷(Co值),驗證軸承在極限載荷下的變形量是否超出允許范圍(通常≤0.05mm)。
2. 材料硬度分析:采用維氏硬度計檢測套筒材料的表面硬度(HRC58-62)和芯部硬度(HRC45-50),確保材料經過適當熱處理,兼具耐磨性和韌性。
3. 金相組織檢驗:通過金相顯微鏡觀察材料晶粒度(要求8-10級)、碳化物分布狀態,避免出現淬火裂紋、脫碳層等冶金缺陷。
三、裝配質量與壽命評估
1. 游隙測量:使用塞規或激光測微儀檢測鋼球與軌道之間的徑向游隙(通常控制在0.005-0.015mm),確保運動平穩性。
2. 潤滑性能測試:在恒溫恒濕箱中模擬不同工況,評估潤滑脂的保持能力和抗析油特性,高溫(120℃)持續運轉200小時后油脂流失量應<15%。
3. 加速壽命試驗:通過高頻往復試驗機進行100萬次循環測試,監測摩擦系數變化(波動幅度≤±20%),評估軸承的磨損速率和疲勞壽命。
四、檢測流程管理
建立三級質量檢測體系:原材料進場檢測(化學成分光譜分析)→ 加工過程檢測(每工序首檢+抽檢)→ 成品出廠檢測(100%全項目檢驗)。采用MES系統實現檢測數據實時采集,建立每套軸承的數字化質量檔案,確保全程可追溯。
結語:通過規范化的檢測體系,可有效控制套筒型直線球軸承的制造質量,降低設備故障率。建議企業依據GB/T 307.2-2020《滾動軸承 測量和檢驗的原則及方法》建立檢測標準,結合工況需求制定差異化的檢測方案,為設備長周期穩定運行提供可靠保障。

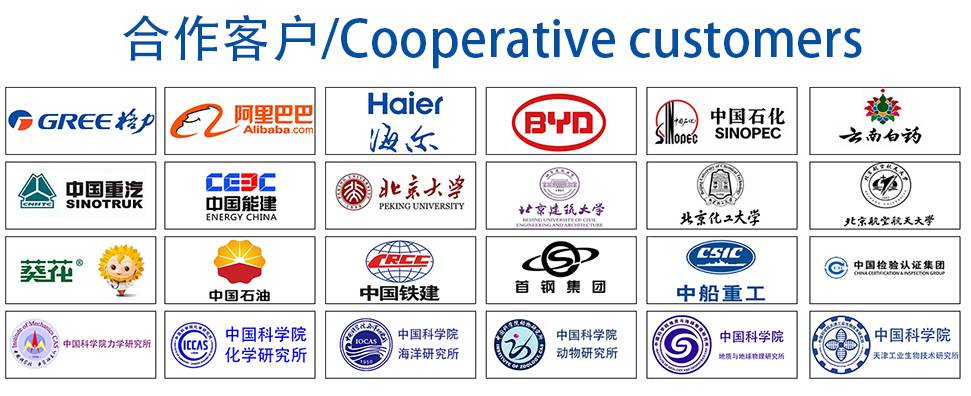