微型球軸承檢測關鍵技術及核心項目解析
在精密機械制造領域,微型球軸承(通常指內徑≤10mm的微型滾動軸承)作為關鍵基礎零部件,其性能直接影響精密儀器、醫療器械、無人機舵機等設備的運行精度與使用壽命。隨著工業4.0時代的到來,微型軸承的檢測技術已從傳統人工測量發展到智能檢測階段,檢測范圍覆蓋幾何精度、材料性能、動態特性等二十余項關鍵指標。嚴格的檢測流程可有效避免因軸承失效導致的設備停機,據統計,規范的檢測程序可提升產品良率35%以上,延長使用壽命超2000小時。
核心檢測項目體系
1. 幾何精度檢測:使用三坐標測量機(CMM)進行精密尺寸測量,重點檢測內徑、外徑、寬度尺寸公差(通常要求±0.001mm),溝道圓度誤差(≤0.3μm),以及內外圈端面平行度。采用激光干涉儀檢測旋轉精度時,徑向跳動需控制在0.5μm以內。
2. 材料性能檢測:通過顯微硬度計測試套圈硬度(HRC58-62),使用金相顯微鏡分析GCr15軸承鋼的碳化物分布(要求帶狀組織≤2級)。振動頻譜分析可檢測材料內部缺陷,異常頻譜峰值超過基準線15%即判定為不合格。
3. 動態性能測試:在專用試驗機上模擬實際工況,檢測啟動力矩(通常≤0.3mN·m)、額定轉速下的溫升(ΔT≤15℃)及振動值(速度型振動≤0.8mm/s)。噪音檢測需在消音室內進行,A計權聲壓級不超過35dB。
齊全檢測技術應用
工業CT斷層掃描技術可非破壞性檢測內部裝配質量,準確識別保持架間隙(≤0.02mm)和鋼球分布均勻性。智能圖像處理系統通過2000幀/秒的高速攝像捕捉潤滑脂分布狀態,油脂覆蓋率需達到95%以上。最新研發的納米級表面輪廓儀可檢測溝道表面粗糙度Ra值(目標≤0.05μm),比傳統觸針式儀器精度提升10倍。
質量控制關鍵節點
在量產階段實施SPC統計過程控制,對關鍵尺寸進行CPK能力指數監控(要求≥1.67)。每批次抽樣進行300小時加速壽命試驗,故障率超過0.5%即觸發質量追溯程序。出廠前100%進行氣密性檢測,確保防水軸承在0.2MPa壓力下無泄漏。
通過構建涵蓋設計驗證、過程監控、成品檢驗的全維度檢測體系,配合MES系統實現檢測數據實時上傳與智能分析,可使微型球軸承的故障返修率降低至0.02%以下,為高端裝備制造提供可靠的基礎件保障。

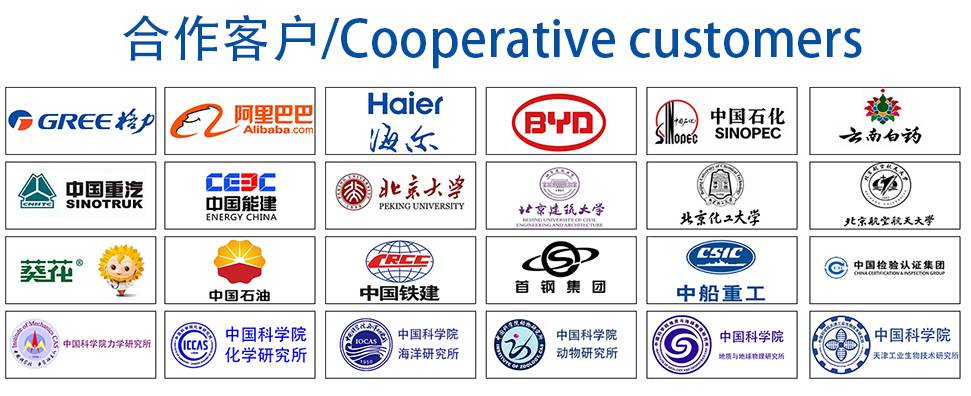