流量控制閥檢測的重要性與技術要點
流量控制閥作為工業管道系統、液壓傳動設備及自動化控制領域的核心組件,其性能直接影響系統穩定性、能效和安全運行。由于長期承受介質壓力、溫度變化及機械磨損,閥體可能出現泄漏、卡滯或調節精度下降等問題。因此,定期開展流量控制閥檢測是保障設備可靠性的必要措施。檢測項目需覆蓋功能性、安全性和耐久性三大維度,同時結合國際標準(如ISO 15848、API 598)與行業規范,通過科學方法評估閥體狀態并提供精準維護依據。
關鍵檢測項目解析
1. 密封性能測試
通過氣壓或水壓試驗驗證閥座與閥芯的密封性,檢測壓力通常為設計壓力的1.1-1.5倍。使用滲漏檢測儀記錄單位時間內泄漏量,對比GB/T 13927標準判定密封等級。高壓差工況下的微泄漏檢測需采用氦氣質譜法等精密手段。
2. 流量特性驗證
在標準實驗臺上模擬不同開度狀態,測量閥門流量系數(Cv值)與開度曲線。利用流量計、壓力傳感器實時采集數據,分析線性特性、等百分比特性是否符合設計要求,偏差超過±5%需進行校準或更換閥芯組件。
3. 耐壓強度試驗
通過液壓試驗臺施加2.5倍額定壓力并保壓5分鐘,觀測閥體是否發生變形、裂紋或滲漏。重點關注鑄造缺陷區域和焊接接縫處,同時檢測法蘭連接面的平面度變化。
4. 材料性能分析
采用光譜儀進行材質成分驗證,防止材料錯用;通過金相顯微鏡檢查閥體內部晶相結構,評估高溫高壓環境下的抗蠕變能力;硬度測試可檢測表面硬化處理效果,確保耐磨性達標。
5. 動態響應測試
在電液伺服測試系統中模擬實際工況,檢測閥門啟閉時間、階躍響應特性及調節精度。對于智能閥門還需驗證4-20mA控制信號的線性度和滯后誤差,確保與DCS系統協同工作的可靠性。
檢測數據應用與維護決策
完整的檢測報告應包含性能參數趨勢分析、剩余壽命評估及維修建議。例如密封面磨損量超過原始厚度30%需進行堆焊修復,彈簧剛度衰減20%以上建議更換。通過建立閥群健康檔案,可實現預測性維護,降低非計劃停機風險達60%以上。

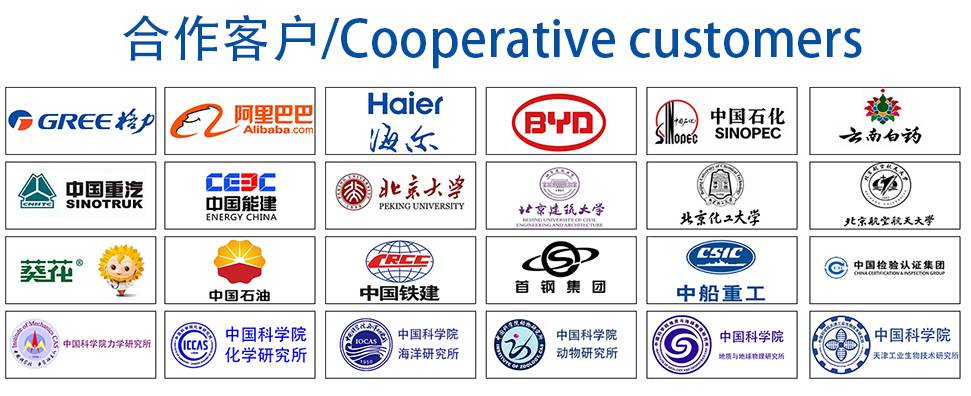