燈泡用氬氣檢測的重要性與技術要點
在現代照明工業中,惰性氣體氬氣(Ar)被廣泛應用于白熾燈泡和節能燈的填充工藝中。氬氣的化學惰性能有效減緩鎢絲在高溫下的氧化速率,同時降低熱量損耗,從而延長燈泡使用壽命并提升發光效率。為確保燈泡性能與安全性,氬氣的純度、填充壓力及密封性檢測成為生產過程中不可或缺的關鍵環節。根據國際電工委員會(IEC)標準及各國行業規范,氬氣檢測需覆蓋氣體成分分析、泄漏測試、壓力穩定性驗證等多個維度,并通過精密儀器與標準化流程實現精準控制。
氬氣純度檢測
氬氣純度直接影響燈泡的性能表現,通常要求工業級氬氣純度≥99.996%。檢測時采用氣相色譜儀(GC)或質譜分析儀,通過分子篩分離技術對氣體中的氧氣(O?)、氮氣(N?)、水分(H?O)等雜質進行定量分析。若雜質含量超標,會導致燈絲氧化加速、光效降低甚至玻璃殼體破裂風險。專業實驗室還會通過紅外光譜法檢測痕量碳氫化合物,確保氣體符合無污染填充要求。
氬氣填充壓力檢測
燈泡內部氬氣壓力需嚴格控制在0.3-0.5MPa范圍內,過高會導致玻璃外殼承壓過大,過低則無法抑制鎢絲蒸發。檢測使用高精度壓力傳感器配合自動化充氣系統,實時監測充氣過程中的壓力變化曲線。量產環節中,壓力衰減測試是核心項目:將燈泡置于恒溫環境中靜置24小時后復測壓力值,衰減率需低于0.5%/年,以此驗證密封結構的可靠性。
氬氣泄漏檢測
泄漏檢測分為宏觀與微觀兩個層級。宏觀檢測采用負壓氣泡法,將燈泡浸入特制檢測液后觀察氣泡生成情況;微觀檢測則使用氦質譜檢漏儀,通過氦氣示蹤法檢測細微泄漏(靈敏度可達10?? Pa·m3/s)。近年新興的激光吸收光譜技術(TDLAS)能實現非接觸式在線檢測,特別適用于高速生產線中實時監控氬氣泄漏率。
工藝環境交叉污染檢測
在燈泡封裝過程中,需同步監測生產環境中氬氣的濃度分布。通過便攜式氣體分析儀對充氣工位、儲存區進行多點采樣,確保環境氬氣濃度維持在安全閾值(通?!?9.5%體積分數)以下,避免因局部富集導致缺氧風險。同時需檢測殘留的焊接保護氣體(如氮氣)是否混入氬氣系統,防止交叉污染影響燈泡性能。
總結
氬氣檢測貫穿燈泡生產的原料驗收、充裝工藝、成品質檢全流程,其技術指標直接關聯產品的光效、壽命及安全性。通過氣相色譜、質譜分析、壓力傳感與氦檢漏等綜合檢測手段,配合ISO/IEC 17025認證實驗室的質量管理體系,可確保氬氣參數完全符合照明器具的嚴苛要求。隨著智能化檢測設備的普及,氬氣檢測正朝著更高精度、更快響應、全流程自動化的方向持續升級。

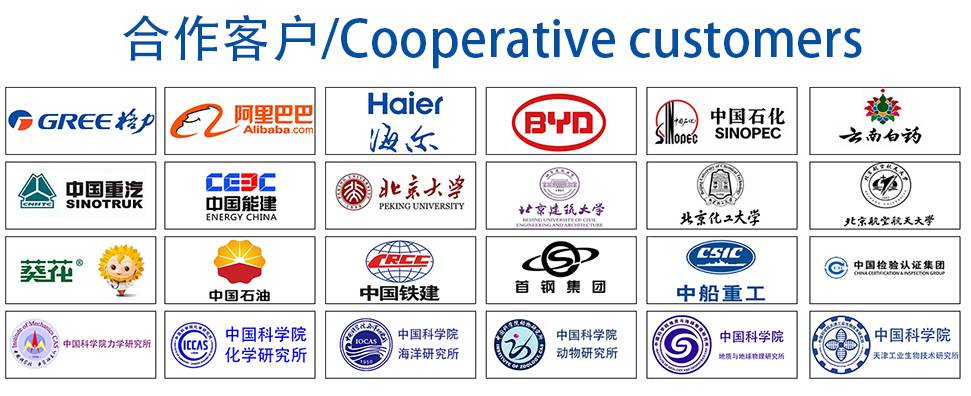