煙草機械檢測:守護生產質量的核心防線
在現代化煙草工業生產體系中,機械設備的性能直接決定了卷煙產品的質量和生產效率。煙草機械檢測作為全產業鏈質量控制的關鍵環節,承擔著確保設備精度、安全性和穩定性的重要使命。從煙葉預處理設備到卷接包裝機組,從濾棒成型機到自動化物流系統,每個環節的機械狀態都需要通過科學嚴謹的檢測體系進行驗證。根據國家煙草專賣局頒布的《煙草機械產品檢驗規程》(YC/T 318-2018),檢測工作必須覆蓋設備全生命周期,包含出廠檢驗、安裝調試檢驗和定期維護檢驗三個階段,確保機械系統在復雜工況下持續滿足GB/T 228.1-2021等國家標準要求。
核心檢測項目體系
1. 機械性能綜合測試
通過三維振動分析儀和激光對中系統,檢測設備運行時的振幅、頻率響應及部件同軸度。采用德國申克公司DMC動態測試系統,模擬滿載工況下的機械應力分布,確保關鍵傳動部件在5萬次循環測試中變形量不超過0.02mm。重點監測齒輪箱溫升曲線,要求連續運行8小時溫度波動不超過±3℃。
2. 電氣安全專項檢測
依據GB 5226.1-2019機械電氣安全標準,使用FLUKE 1587絕緣測試儀進行2500V耐壓測試,漏電流需控制在5mA以下。對控制系統進行EMC抗干擾測試,模擬車間復雜電磁環境,確保PLC系統在4kV靜電放電和10V/m射頻干擾下仍能穩定運行。
3. 氣密性精準驗證
針對卷煙機煙支成型系統,采用氦質譜檢漏法檢測負壓管路的密封性,要求泄漏率≤1×10^-7 Pa·m3/s。使用英國愛德華真空計監測負壓波動,在2000支/分鐘生產節奏下,負壓穩定性需控制在設定值的±2%范圍內。
4. 自動化功能驗證
通過工業總線協議分析儀,對設備的3000個I/O點進行信號完整性測試。模擬斷料、卡紙等22種異常工況,驗證自動剔除系統的響應速度,要求故障識別到執行動作的延遲不超過0.3秒。使用機器視覺系統檢測煙支排列精度,搭口錯位誤差需≤0.15mm。
5. 材料耐腐蝕性檢測
對接觸煙末的304不銹鋼部件,按照GB/T 10125-2021標準進行480小時鹽霧試驗。檢測表面鈍化膜完整性,要求鎳元素含量≥8%,鉻元素含量≥18%,點蝕深度不超過10μm。同步進行煙草萃取液浸泡實驗,評估材料在有機酸環境中的抗腐蝕性能。
檢測技術發展趨勢
隨著工業4.0技術的深度融合,煙草機械檢測正在向智能化方向轉型。基于數字孿生技術的虛擬調試系統,可在設備投產前完成90%的故障模擬檢測;采用紅外熱成像技術實時監測軸承溫升趨勢,結合大數據分析實現預測性維護;激光干涉儀配合AI算法,可將設備幾何精度校準效率提升40%。這些創新檢測手段的運用,正在重塑煙草機械質量保證體系的新格局。

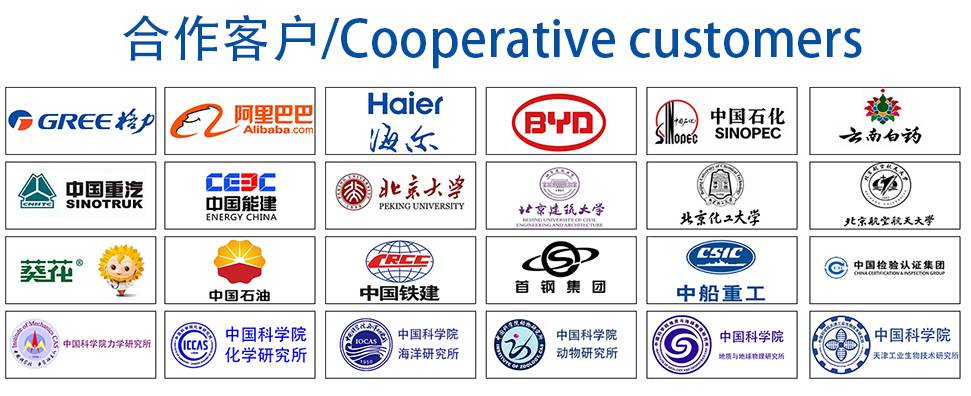