內燃機氣缸套檢測的重要性
內燃機氣缸套作為發動機的核心部件,承擔著密封燃燒室、引導活塞運動以及傳遞熱量的關鍵功能。其工作環境極其惡劣,長期承受高溫、高壓、腐蝕性氣體和機械磨損的考驗。氣缸套的質量和性能直接影響發動機的功率輸出、燃油效率、排放水平及使用壽命。因此,針對氣缸套的系統化檢測是保障發動機可靠運行、預防故障、延長維護周期的重要技術手段。現代工業中,氣缸套檢測已貫穿于制造、裝配、維修全生命周期,涉及幾何尺寸、材料性能、表面狀態等多維度分析。
核心檢測項目及方法
1. 尺寸精度檢測
通過三坐標測量儀(CMM)或專用量具對氣缸套的內徑、外徑、長度等關鍵尺寸進行精密測量,確保其符合設計公差要求。對于磨損后的舊缸套,需重點檢測內徑橢圓度、錐度變化,判斷是否超出允許修復范圍。
2. 表面粗糙度與形貌分析
使用表面輪廓儀或原子力顯微鏡(AFM)對缸套內壁進行微觀形貌掃描,評估珩磨網紋的均勻性、溝槽深度及分布密度。表面粗糙度(Ra/Rz值)直接影響潤滑油膜形成能力,需控制在0.4-1.6μm范圍內。
3. 硬度與耐磨性測試
采用洛氏硬度計或顯微硬度計測定缸套基體及表面鍍層(如鎳基碳化硅涂層)的硬度值,驗證熱處理工藝效果。通過摩擦磨損試驗機模擬實際工況,評價材料的抗磨粒磨損和黏著磨損性能。
4. 金相組織檢驗
對缸套材料進行剖切、研磨、腐蝕后,利用金相顯微鏡觀察石墨形態(鑄鐵缸套)、晶粒度、碳化物分布等微觀結構,排查鑄造缺陷(縮孔、夾渣)或熱處理異常導致的組織不均勻問題。
5. 耐腐蝕與密封性檢測
通過鹽霧試驗、電化學腐蝕測試評估缸套在酸性燃燒產物環境中的耐蝕能力。使用氣壓/水壓試驗裝置檢查缸套與缸體裝配后的密封性能,確保冷卻水腔無滲漏風險。
6. 裂紋與缺陷探傷
綜合運用磁粉探傷(MT)、超聲波探傷(UT)或工業CT掃描技術,檢測缸套表面及內部的微裂紋、氣孔、夾雜物等缺陷,尤其關注應力集中區域(如法蘭過渡處)。
智能化檢測技術發展趨勢
隨著工業4.0技術的普及,激光掃描三維重建、AI圖像識別算法、在線監測傳感器等新技術逐步應用于氣缸套檢測領域。例如,基于機器視覺的自動缺陷分類系統能實現毫秒級裂紋識別,而嵌入式溫度/振動傳感器可實時監控缸套工況。這些創新手段顯著提升了檢測效率和數據可靠性,為發動機健康管理提供精準決策支持。

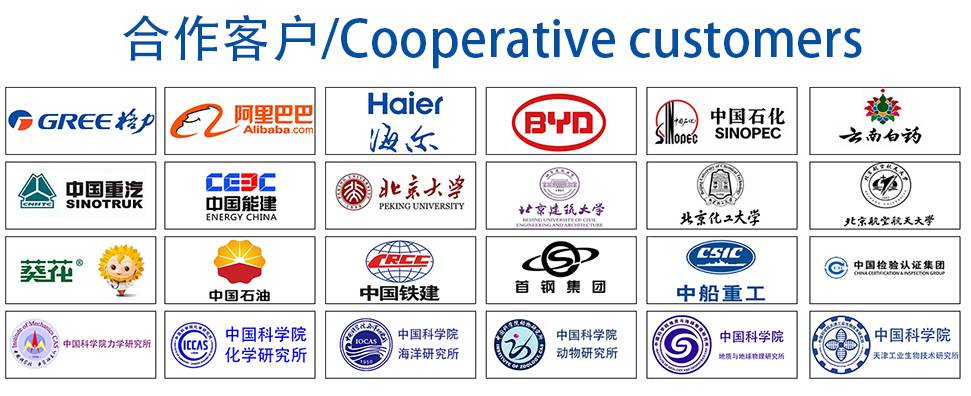