硼鑄鐵氣缸套檢測的必要性與流程分析
硼鑄鐵氣缸套作為柴油發動機、船用發動機等大型動力裝置的核心部件,其質量直接影響發動機的使用壽命和運行效率。由于該部件長期承受高溫、高壓和活塞高頻往復運動的復雜工況,對材料的耐磨性、耐腐蝕性和尺寸穩定性要求極高。通過系統化的檢測流程,可有效驗證硼鑄鐵氣缸套的化學成分、物理性能及加工精度是否滿足行業標準(如GB/T 1150-2010、ASTM A532等),確保產品在極端工況下的可靠性。
1. 材料成分檢測
采用直讀光譜儀對硼元素含量進行定量分析,確保硼含量控制在1.8-3.5%的工藝范圍。同步檢測碳(2.8-3.6%)、硅(1.8-2.5%)、錳(0.5-1.2%)等合金元素的配比,借助X射線熒光光譜(XRF)驗證元素分布的均勻性。硼元素作為關鍵強化劑,其含量直接影響碳化物的生成形態和分布密度。
2. 金相組織分析
通過400倍金相顯微鏡觀察基體組織形貌,重點評估珠光體含量(≥95%)、球狀石墨形態(球化率>90%)以及硼碳化物(Fe23(C,B)6)的分布特征。使用圖像分析軟件定量統計碳化物面積占比(8-15%),確保硬質相呈彌散均勻分布,避免出現網狀或塊狀偏析。
3. 機械性能測試
按照ISO 6507標準進行維氏硬度(HV220-280)檢測,采用萬能材料試驗機測定抗拉強度(≥250MPa)和延伸率(≥1.5%)。特別設置高溫硬度測試(300℃下HV≥180),模擬實際工況下的材料性能變化。通過超聲波探傷儀檢測鑄造缺陷,要求孔隙率<0.2%。
4. 尺寸精度檢測
使用三坐標測量儀對缸套內徑(Φ150-400mm)進行多截面測量,圓度誤差≤0.02mm,圓柱度≤0.03mm/m。采用激光輪廓儀檢測珩磨網紋夾角(40-60°)及溝槽深度(3-8μm),確保儲油能力達標。內表面粗糙度要求Ra≤0.4μm,波紋度Wt≤0.8μm。
5. 表面質量檢查
通過10倍放大鏡檢查鑄造表面,嚴格控制冷隔、縮松等缺陷。采用熒光滲透檢測(PT)驗證微觀裂紋,要求表面缺陷深度不超過壁厚的5%。使用白光干涉儀評估平臺珩磨的表面支承率(≥85%),確保活塞環的密封性能。
6. 耐磨性試驗
在專用摩擦磨損試驗機上模擬活塞環-缸套配副工況,載荷3-5MPa,線速度0.5-1.5m/s,持續120分鐘。檢測質量磨損率(≤0.8mg/cm2·h),表面硬度下降值不超過初始值的15%。同步檢測摩擦系數變化曲線,要求穩定在0.08-0.12區間。
7. 密封性檢測
采用氦氣質譜檢漏法進行壓力密封試驗,在0.6MPa氮氣壓力下保持30分鐘,泄漏率應<1×10-7 Pa·m3/s。水壓試驗壓力為工作壓力的1.5倍,保壓10分鐘無滲漏。通過氣缸套-機體模擬裝配試驗驗證熱態密封性能。
通過上述系統的檢測流程,不僅可精準把控硼鑄鐵氣缸套的生產質量,更能通過檢測數據優化鑄造工藝參數(如澆注溫度、冷卻速度等)和機加工方案,推動產品性能的持續改進。建議生產企業建立包含SPC統計過程控制的數字化檢測體系,實現質量數據的全生命周期管理。

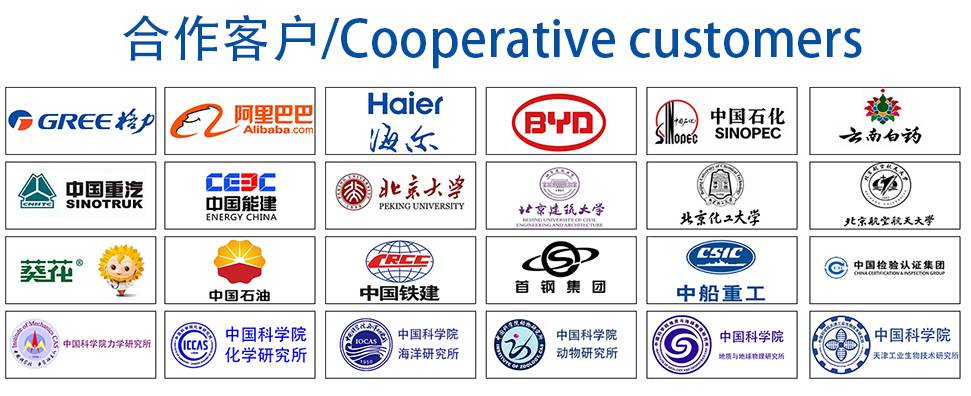