尺寸測定檢測在工業生產中的關鍵作用
尺寸測定檢測作為現代制造業質量控制的核心環節,直接影響產品精度、裝配性能和使用壽命。在機械制造、汽車工業、航空航天、電子元件等領域,通過系統化的尺寸檢測流程,可有效驗證產品的幾何參數是否符合設計要求,確保零部件互換性,避免因尺寸偏差引發的功能性故障。隨著智能制造和精密加工技術的發展,檢測精度已從毫米級提升至微米甚至納米級別,檢測方法也呈現出多樣化、智能化和在線化的新趨勢。
常規接觸式測量方法
傳統接觸式測量仍是基礎工業的主力檢測手段:
1. 量具檢測:游標卡尺、千分尺、塞規等通用量具適用于車間現場快速檢測,可完成長度、直徑、間隙等基礎尺寸測量,經濟實用但依賴操作者技能
2. 三坐標測量機(CMM):通過接觸式探針獲取三維坐標數據,可測量復雜曲面和空間幾何尺寸,重復精度可達±1.5μm,配備專用夾具后實現自動化檢測
3. 輪廓測量儀:采用金剛石探針掃描表面輪廓,特別適用于螺紋、齒輪等精密部件的微觀形貌分析,分辨率可達0.01μm
齊全非接觸式檢測技術
新型檢測技術大幅提升檢測效率和適用場景:
1. 激光掃描測量:基于三角測量原理的激光位移傳感器可進行高速三維掃描,單點測量頻率達50kHz,適用于渦輪葉片等復雜曲面的全尺寸檢測
2. 機器視覺檢測:采用高分辨率工業相機配合圖像處理算法,可完成微小電子元件(如芯片焊點)的亞像素級尺寸測量,檢測速度達3000件/小時
3. 白光干涉儀:利用光學干涉原理測量納米級表面粗糙度,在光學元件和半導體晶圓檢測中實現Ra≤0.1nm的測量精度
智能化在線檢測系統
工業4.0推動檢測技術向數字化方向發展:
1. 在線SPC系統:集成傳感器網絡實時采集生產數據,通過統計過程控制(SPC)自動識別尺寸波動趨勢,實現質量預警和工藝優化
2. 數字孿生檢測:建立虛擬樣機的三維數字模型,通過MBD(基于模型的定義)技術實現設計-測量-修正的全流程閉環管理
3. 機器人測量單元:搭載6軸機械臂的柔性檢測站,可自動切換測量工具,適應多品種產品的快速換線檢測需求
檢測標準的體系化建設
完善的標準化體系保障檢測結果可靠性:
1. 執行ISO/ASME標準:依據ISO 14253(產品幾何量規范)和ASME Y14.5(尺寸公差標注)建立檢測規范
2. 測量系統分析(MSA):通過重復性&再現性(GR&R)研究評估檢測系統能力,要求量具R&R≤10%方可投入使用
3. 實驗室認證體系:通過 /ISO17025認證的檢測實驗室需定期進行量值溯源,確保測量結果國際互認
隨著5G通信和AI技術的融合應用,尺寸檢測正朝著智能診斷、預測維護的方向發展。企業應建立涵蓋設計驗證、過程監控、成品檢驗的全生命周期質量管理系統,通過精確的尺寸測定檢測持續提升產品競爭力和品牌價值。

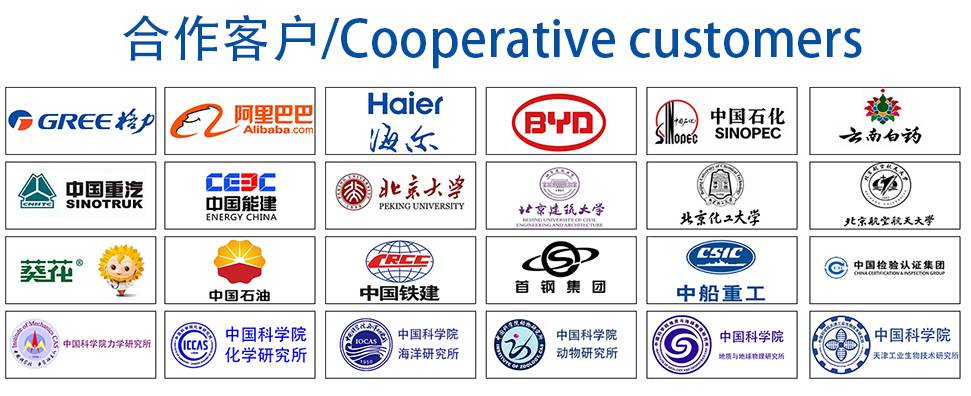